Arc Welding System Automates Weld Program Creation
Trumpf has release the TruArc Weld 1000. Equipped with a cobot, the system provides an automated alternative for parts users typically weld manually.
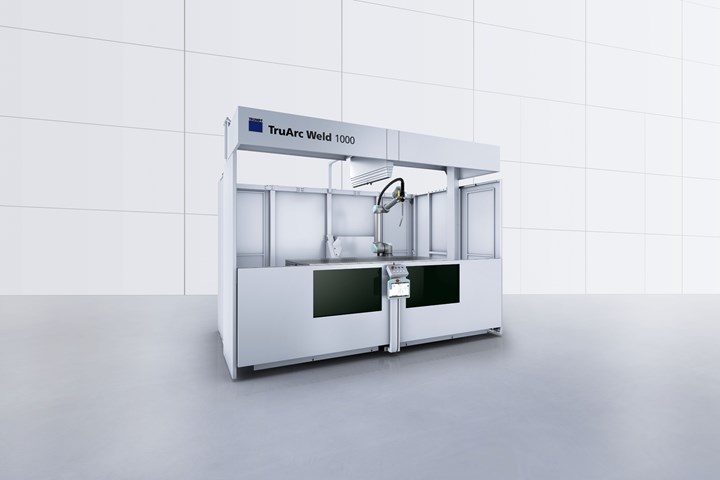
Photo Credit: Trumpf Inc.
Trumpf Inc. has released its first automated arc welding system, the TruArc Weld 1000. The system comes with a collaborative robot (cobot) which, once manually guided over the part by the operator, automatically creates the weld program, eliminating reliance on values from an offline source or entering positional data manually. CE-compliant and approved by TÜV Austria, the TruArc Weld 1000 is said to meet the highest safety standards.
A built-in sensor, ensures a smooth response from the cobot. Equipped with an operating unit, the cobot enables users to store the weld path’s start and end points as well as intermediate points in order to create the program. Furthermore, the cobot control system includes templates for welding programs and parameters that cover scenarios such as different sheet thicknesses. Combined with the operating unit on the welding torch, this reportedly simplifies the task of programming the cobot, and facilitates efficient and fast programming and welding.
The TruArc Weld 1000 is said to offer an automated alternative for many parts that users would normally weld manually and produces a high-quality weld seam. Moreover, its rapid programming provides fabricator an affordable means of tackling short production runs and single-part runs even if the parts only require a short weld seam.
Inside the TruArc Weld 1000 is a partition that can be moved up and down. This allows users to divide up the working area and choose between welding one large part (single-station operation) or several smaller ones (two-station operation). In single-station operation, the cobot can weld parts measuring up to 80 x 24 x 24 in. Other ratios of width to length are also possible depending on part dimensions. In two-station operation, the TruArc Weld 1000 can process smaller parts measuring up to 24 x 24 x 24 in. To ensure it can easily reach both stations, the cobot travels between two stations along a linear axis. While the cobot is performing welding on one side, the operator can use the time to set up a part on the other side. The cobot program can also be transferred automatically from one station to the other.
No previous experience is required to operate this system. Trumpf says customers can carry out commissioning of the CE-compliant TruArc Weld 1000 themselves within a few hours using dedicated video tutorials that contain all the information required to quickly learn how to operate and program the machine outside of a classroom.
Related Content
-
The Ins and Outs of Hot Runner Temperature Control
A training checklist that explains the why and how of proper hot runner temperature control and system management.
-
Think Safety: Eliminate Hazards Throughout the Shop
The tooling community is taking advantage of new products for safer mold shops and molding facilities.
-
Laser Welding Versus Micro Welding
The latest battle in finely detailed restoration/repair of mold materials.