Four Industry 4.0 Tech Adoption Insights from Indiana Plastics Manufacturers
As more plastics manufacturers step into the Fourth Industrial Revolution, insights have emerged about how best to approach the digital transformation journey.
In Indiana, successful Industry 4.0 implementation strategies have been revealed through more than 50 interviews with early adopters, many of which are in the plastics industry.
The interviews come from companies that have received matching grants from a state-supported program launched in mid-2020 to help Indiana manufacturers deploy Industry 4.0 technologies in their production processes. To date, the Indiana Manufacturing Readiness Grants program and the state of Indiana have awarded $45 million in matching grants to more than 420 Indiana manufacturers, supporting $628 million in technology-enabled capital investment.
It’s no surprise to those familiar with manufacturing in the Midwest that plastics manufacturers have benefited from this program. Plastics is Indiana’s sixth largest advanced manufacturing sector and is expected to grow over the next five years by nearly 1,400 jobs supporting many critical industry subsectors, including automotive, transportation and medical. Nationally, Indiana ranks seventh in plastics industry employment, according to the Plastics Industry Association.
As Conexus Indiana, a nonprofit organization dedicated to strengthening Indiana’s advanced manufacturing industry, and the state of Indiana continue to support manufacturers on their Industry 4.0 journeys — including cobots, additive manufacturing, robotics and the Industrial Internet of Things (IIoT) — several best practices have been established. Four examples from plastics companies are:
Develop an Industry 4.0 technology adoption road map: DeKalb Molded Plastics in Butler, Indiana, a firm that specializes in large, multicomponent plastic products for the medical, safety and transportation, and material handling industries, installed a new industrial robot to decrease operators’ direct interaction with injection molding machines. For DeKalb Molded Plastics, having a technology road map helped it prioritize its investments in automation technologies: first robotics, then collaborative robots (cobots).
Take time to identify the right technology use case: With more than a dozen technologies associated with Industry 4.0, the array of choices can complicate selection. Metro Plastics Technologies in Noblesville, Indiana, invested in a robot cell for high-volume, high-speed assembly to reduce labor costs and increase capacity. Cobots were not deployed in this situation as they are often better suited for low-volume, high-mix applications where manufacturing flexibility is required.
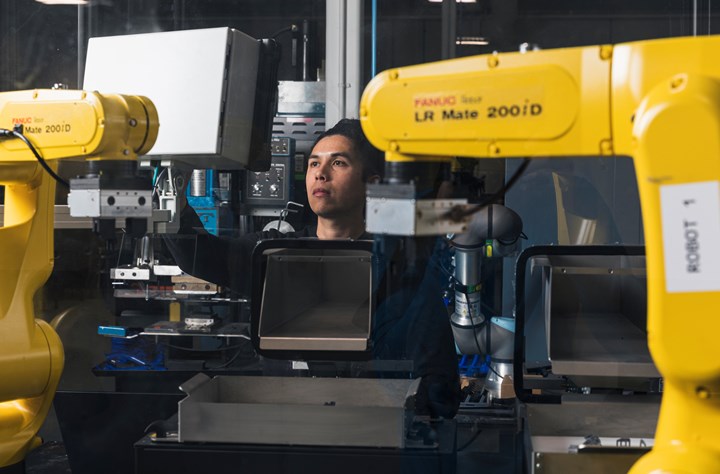
Metro Plastics created a high-volume, high-speed assembly cell to boost production. Photo Credit: Conexus
Engage the ecosystem of technology integrators: Dozens of companies have benefited from working with a technology integrator or automation solution provider. These trusted partners have specific expertise in delivering and deploying Industry 4.0 solutions into production environments, and they often assist through the full life cycle of planning, implementation and workforce training. For Konrady Plastics in Portage, Indiana, deploying two cobots paired with their HAAS lathes for machine tending was completed with the help of Fusion Robotics/RoboJob-USA. More specifically, Fusion provided software integration support between the lathes and cobots.
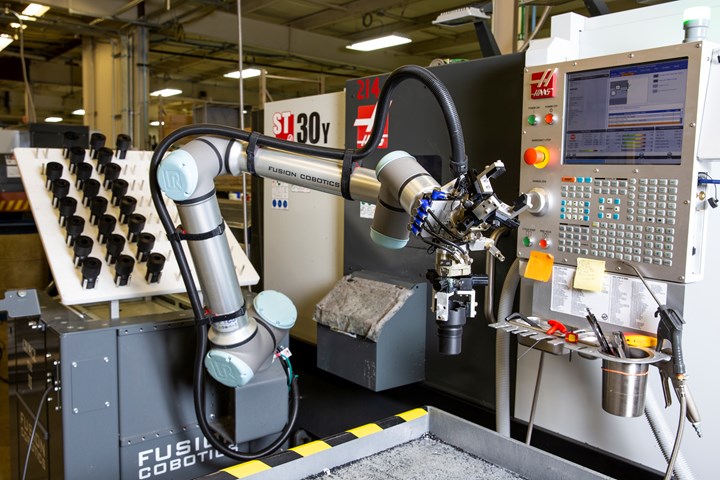
Konrady Plastics pairs cobots with a lathe to automate some machining operations. Photo Credit: Conexus
Invest in workforce development: The existing workforce is ready to learn digital skills and operate Industry 4.0 job functions. Emphasizing workforce development alongside the procurement of technology is the best way to maximize productivity. Michiana Global Mold in Mishawaka, Indiana, partners with the National Tooling & Machining Association (NTMA) to teach digital and technical skills to its Michiana workforce. The company relies heavily on NTMA’s educational opportunities for workforce development alongside technology adoption. Called NTMA University, the program provides classroom training sessions to the workforce and leads to official credentials.
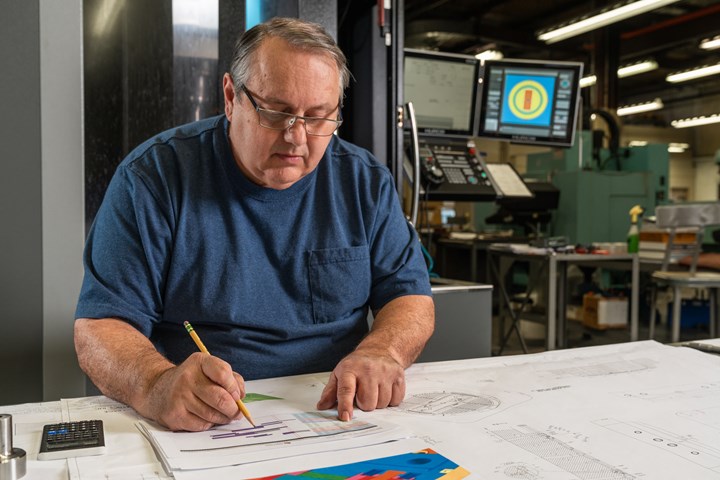
Michiana Global Mold partners with the National Tooling & Machining Association on workforce development.
Photo Credit: Conexus
While these best practices can create value for any manufacturing company looking to adopt new technologies, they are especially applicable for the plastics manufacturing subsector. With many end users and customers operating in the packaging, automotive and construction industries, supply chain partners may formally or informally request the adoption of Industry 4.0 technologies and systems. Plastics companies that don’t follow suit may risk the loss of future business contacts, and therefore should be willing to embrace digital transformation.
Related Content
Achieving Flexible Capacity with Automation
This high-mix, low-volume manufacturer embarked on a year and a half program to introduce robotics to its manufacturing process.
Read MoreAdvancing Moldmaking and Plastics: Trends in 3D Printing, Automation and Sustainability
NPE 2024 showcased the latest trends and technologies in innovation, efficiency and sustainability for moldmakers and molders, featuring advancements in 3D printing, automation, design and virtual reality/augmented reality/artificial intelligence.
Read More5 Ways to Make Your Tooling Assets Smarter
Global mold monitoring and asset management solutions can maximize productivity and efficiency.
Read MoreWhat is Driving Mold Lifecycle Management Digitalization?
OEMs are looking to partner with suppliers to share and track data across the supply chain for advanced intervention and process management.
Read MoreRead Next
Michiana Global Mold’s Director of Business Development Shares Three Favorite People-Focused Articles
MMT’s Editorial Advisory Board shares its top MoldMaking Technology articles of all time and how this content has been valuable to their businesses.
Read MoreHow to Use and Protect Remote Machine Monitoring Data
Collecting, analyzing and securing machine data in real time can substantially improve productivity, profitability and customer satisfaction.
Read More5 Steps to Get Started With Digitalization
Knowledge, a strong partner, an internal champion and an active regular participation in highly visible data will help smaller mold shops with digitalization.
Read More