5 Steps to Get Started With Digitalization
Knowledge, a strong partner, an internal champion and an active regular participation in highly visible data will help smaller mold shops with digitalization.
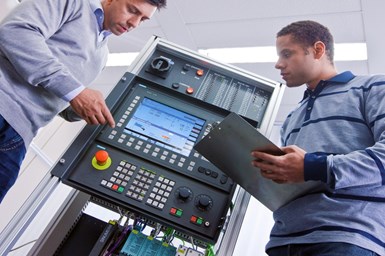
Machine operators are essential when planning and integrating digitalization on the shop floor. Photo Credit: Siemens Industry Inc.
Digitalization is all about connectivity, data gathering and analyzing the data to develop a smart action plan. Digitalization is one way to boost productivity, enhance shopfloor flexibility and preserve data security. Common digitalization tasks arise in work preparation and production itself or machining using machine tools. Recently, I was asked what smaller mold builders can do to begin their march toward digitalization and make the process as easy and fail-proof as possible The good news is that digitalization can be implemented step by step. Here are five initial steps to take:
- Learn. Dedicate one person in your shop to learn about digitalization. It should be someone with an open mind to understand what digitalization means for your specific operation. There are so many buzzwords and acronyms, such as overall equipment effectiveness (OEE), big data and Industry 4.0, so this person must get comfortable with these concepts. Talk to people inside and outside of your organization, listen to podcasts, read trade publications, and attend trade shows and conferences.
- Find a partner. Identify someone who will support you throughout the entire process, from an initial evaluation to implementation as well as the new protocols of action required. This could be a small consulting firm or someone who brings an outside perspective into your shop. Be sure it’s someone who knows your industry because that reduces startup time. There are many kinds of partners, including ones with deep experience in moldmaking. Maybe your perfect partner is someone you’re already working with or who is advising you on your CNC machines. They can educate you about digitalization and even work with your team to find the right solution. This partner must know your process flow.
Knowledge, a strong partner, an internal champion and active regular participation in highly visible data will help smaller mold shops with digitalization.
- Identify an internal digital champion. Search within your shop for somebody you can ask to play the role of digitalization consultant for your side and then start slowly. Don’t think about all of your equipment at the beginning. Pick one or two machines to focus on from which you want to get data and begin tracking it.
- Communicate the plan and share the data publicly. The digitalization process mustn’t come from one person who reports that the company is installing something to improve quality; instead, get everyone on board with the entire conversion process from the start. Make the data visible. Get a large display screen for the data you’re gathering and place it in the middle of the shop where everybody can see the data you’re capturing. This also allows employees to ask questions about the data and share feedback on its output.
- Talk about the data daily. Foster a culture of communication so people feel comfortable asking questions. For example, “Why aren’t we tracking our daily downtime?” Speak with all of your machine operators because they have different opinions on the data to track, why a particular value isn’t displayed or why cycle times vary on the same part of the same machine. Getting their input and working together ensures a return on your investment.
Related Content
What is Scientific Maintenance? Part 2
Part two of this three-part series explains specific data that toolrooms must collect, analyze and use to truly advance to a scientific maintenance culture where you can measure real data and drive decisions.
Read MoreHow to Analyze and Optimize Cutting Conditions to Reduce Cycle Time
Plastic injection mold design and manufacturing company puts NC program optimization software module to the test. The results were surprising.
Read MoreVIDEO: Perspective on A.I. and Mold Design
Bill Genc of TopSolid shares his perspective on the benefits of and barriers to using artificial intelligence in mold design.
Read MoreMMT Chats: Solving Schedule and Capacity Challenges With ERP
For this MMT Chat, my guests hail from Omega Tool of Menomonee Falls, Wisconsin, who share their journey with using enterprise resource planning (ERP)—and their people—to solve their schedule and capacity load monitoring challenges.
Read MoreRead Next
Five Ways to Tackle Tough Mold Design Tasks with Digitalization
Transform static 3D designs into animated 4D designs that simulate motion and interaction of complete mold systems to improve design workflow.
Read MoreUsing Real-Time Production Data
One approach to smart manufacturing is using a single, cloud-based tool for production scheduling, job tracking and CNC machine monitoring.
Read MoreWhat is Driving Mold Lifecycle Management Digitalization?
OEMs are looking to partner with suppliers to share and track data across the supply chain for advanced intervention and process management.
Read More