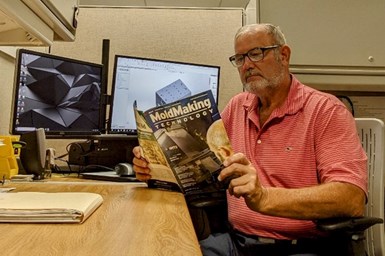
Medline Industries’ Engineering Manager Rick Seaberg looks through MoldMaking Technology at work.
Photo Credit: Medline Industries
Rick Seaberg has 10 years of experience as an injection mold designer, 15 years as a tooling engineer, 12 years as an engineering manager and two years as a plant manager across the consumer packaging, medical, automotive and optical industries.
Today, Rick is the engineering manager at Medline Industries, a private American healthcare company based in Northfield, Illinois. His participation on the EAB includes leadership, processing and procuring molds, training around mold maintenance and trends in Europe, Japan, China and Singapore.
Here, he continues this year’s EAB series by sharing his three all-time favorite MoldMaking Technology articles and key takeaways that have been valuable to his work.
1. January 2022 — Save Time, Money: Use a Mold Design Checklist
Here are 15 examples of common molding issues that occur during an initial mold trial. Many of them could be avoided or corrected with a proactive checklist.
I like this article because it speaks to my roots as a mold designer. It also touches on standardization, critically important to every aspect of mold design, manufacturing and project management. And lastly, it stresses the importance of being proactive — a little extra effort at the beginning of a project may take more time, but down the road, it will actually save time and avoid headaches.
The article focuses on a new mold startup and moving into production, but the same thought process applies to mold safety and preventative maintenance. For example, the article refers to checklists as “living” documents the team should update frequently, and I agree. At Suncast Corp., we had rigorous design reviews across all departments (setup, processing, product design, quality, maintenance). As a result of these meetings, we would update the specifications and checklists immediately when an issue arose and the team wanted to make a new standard, keeping our best practices current.
2. October 2016 — Do Scheduled PMs Really Work?
True preventative maintenance is accurately monitoring and counting issues and corrective actions over time.
I enjoy every article that Steve Johnson writes. He is a true visionary in the often-neglected world of mold maintenance. He is the first person I reference when trying to persuade upper management to focus on better mold maintenance best practices and take the time to understand the impact proper maintenance can have on operations and the bottom line.
This article offers essential steps of a solid maintenance program, which can produce real bottom-line results. First is data collection. Johnson notes that “the critical ingredient to real improvement lies in the ability to monitor and count issues accurately and corrective actions over time, with “time” being mold cycle counts or parts produced. Mold performance does not rely solely on molds being cleaned more often, but on monitoring defects and mold issues to create a viable list of targets that users can focus on when molds are taken out for PM.”
The article also reviews standardization. For example, standardizing terminology and training the team, standardizing data collection and analysis (e.g., work orders, last shots, etc.) and standardizing data entry in maintenance logs for future technicians to understand the mold and its maintenance history clearly.
I recommend handing this article to upper management and signing up for one of Steve’s seminars to help move your maintenance plan to the next level.
3. February 2017 — Maintenance Matters: It’s the Manager’s Fault
Improving worker engagement starts with the leadership at the manager level or, in our case, the toolroom manager.
When I looked at this article again, I was pleasantly surprised to see that the author was Steve Johnson. So, while this article pertains more to managing mold repair operations, plenty of information can be applied across an organization.
When I first became a manager, I struggled to figure out my new role in managing employees and came across a book, Why Employees Don't Do What They’re Supposed To Do, And What To Do About It, written by Ferdinand Fournies. I thought this book would be exactly what I needed to understand people. Well, the joke was on me. Most of the book is about what a manager needs to do to better train, understand, communicate with and motivate their personnel.
Johnson’s article touches upon those same themes — training, providing opportunities and ensuring employees are in the right job to provide the most satisfaction and performance. It also covers standardization (there it is again!), data collection and communication via KPIs. “Measurement without targeted action is useless.” Highly skilled employees like mold builders must have real and meaningful work and data to stay engaged and motivated.
The article ends with a list to measure employee engagement and performance. Do you have the confidence to share that list and evaluate where you are as an organization?
Related Content
Generational Quality: Balancing Tradition, Innovation and Continuous Improvement
Q&A with Corey Fox, an MMT EAB member and Operations Manager at Accede Mold and Tool.
Read MoreEditorial Advisory Board 2023-2026: Meet New Board Member Adam Nartker, Diversified Technologies International
The 2023-2026 version of MoldMaking Technology’s EAB features a new crew of industry professionals. Meet Adam Nartker.
Read MoreEditorial Advisory Board 2023-2026: Camille Sackett, Vice President of Sales and Marketing for Accede Mold & Tool
The 2023-2026 version of MoldMaking Technology's EAB features a new crew of industry professionals. Meet Camille Sackett
Read MoreThe Intersection of Robotics, Hands-on Training in Mold Design Curriculum
A Q&A with Nicholas Vitelli, MoldMaking Technology EAB member and engineering lecturer at Penn State Erie, The Behrend College.
Read MoreRead Next
Do Scheduled PMs Really Work?
True preventive maintenance lies in accurately monitoring and counting issues and corrective actions over time.
Read MoreMaintenance Matters: It's the Manager's Fault
Improving worker engagement starts with leadership at the manager level or, in our case, the toolroom manager.
Read MoreSave Time, Money: Use a Mold Design Checklist
Here are 15 examples of common molding issues that occur during an initial mold trial. Many of them could be avoided or corrected with a proactive checklist.
Read More