Thermally Sensitive or Corrosive Applications are Combatted by Hot Runners
Combined with Husky Technologies’ experience, guidelines and analysis tool, the company’s new UltraMelt hot runner technology meets the processing needs of challenging resins and demanding applications.
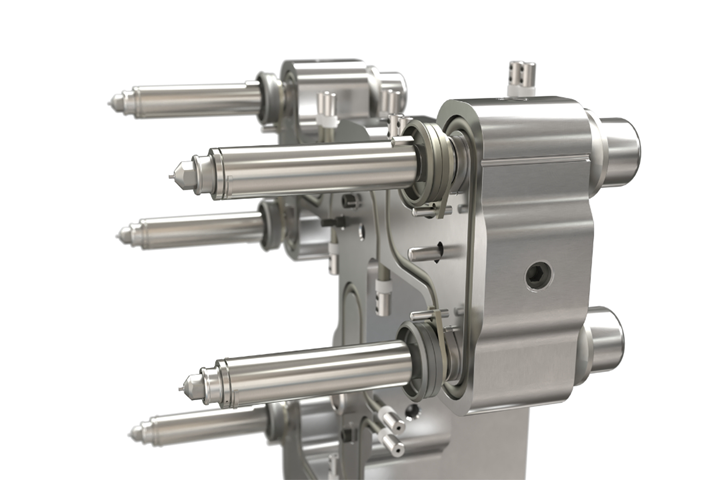
Photo Credit: Husky Technologies
UltraMelt is Husky Technologies’ premium solution for thermally sensitive or corrosive applications which require excellent process and thermal control, with a minimal effect to the resin chemistry.
The hot runner technology is suited for very small technical or medical parts made from different grades of polycarbonate, which can easily degrade at certain temperatures or residence times. These parts typically allow for minimal to no variation in surface finish, part quality or color, Husky says, and therefore must be processed with carefully designed equipment and technology. UltraMelt is also designed for bioresin applications such as polylactic acid (PLA), polyhydroxyalkanoate (PHA) and cellulose acetate (CA) which are challenging to mold due to resin chemistry.
According to the company, all of UltraMelt’s molten resin contact surfaces are made from non-reactive materials. These materials reportedly extend component longevity against the corrosive effects of certain resins and provide optimized control over thermal profile. UltraMelt also ensures the lowest risk for melt degradation, oxidization and discoloration, Husky says. Now available globally, the hot runner technology is customized for each application and available with a variety of gating methods, nozzle sizes, manifold pitches and actuation styles. It can be used in both low- and high-cavity applications.
Related Content
-
How to Eliminate Chatter
Here are techniques commonly used to combat chatter and guidelines to establish a foundation for optimizing the moldmaking process.
-
Hands-on Workshop Teaches Mold Maintenance Process
Intensive workshop teaches the process of mold maintenance to help put an end to the firefighting culture of many toolrooms.
-
Machining Center Spindles: What You Need to Know
Why and how to research spindle technology before purchasing a machining center.