Hot Runner Cooling Design Lowers Energy Consumption, Maintenance
Oerlikon HRSflow says the HRScool Evo’s design eliminates separate, active water cooling for the hot runner pin’s hydraulic cylinder, reducing energy consumption by up to 10%.
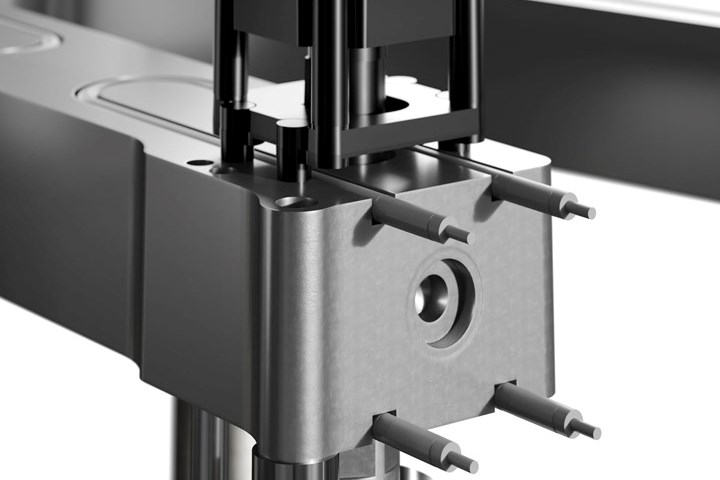
Photo Credit: Oerlion HRSflow
Hot runner supplier Oerlikon HRSflow has developed a hot runner injection molding system, HRScool Evo, in which the hydraulic cylinder that positions the pin does not require separate, active water cooling. Since the technology’s improvements announced in 2022, the company cites energy consumption reduction at the drops by up to 10%, depending on the system size and application. Moreover, eliminating active water cooling reduces the total number of components for the hot runner, cutting assembly and maintenance time.
Hot runner system cylinders act as high-precision actuators, and typically use water cooling to ensure the optimum working temperature is maintained. With HRScool Evo, a thermally insulating air gap towards the cavity is used to reduce the heating of the cylinder and the thermal loss of the manifold.
In addition, use of a highly heat-conductive cover on the opposite side ensures optimum heat dissipation towards the cold clamping platen. The company notes that the height can be adjusted via telescopic supports, enabling molders to tune heat transfer and thermal uniformity over the entire hot runner system to maximize part quality.
Massimo Rossi, R&D director at Oerlikon HRSflow, stated in a release that in addition to energy efficiency, the elimination of lines and connections required for water cooling means these components can no longer become clogged or corrode. In addition, the ability to remove the actuators while the needles remain in the hot runner system further reduces maintenance, and limiting the design to a thermally insulating and thermally conductive element allows for a more compact design, with small cut-outs in the clamping plate sufficient for installation.
Related Content
-
Machining Center Spindles: What You Need to Know
Why and how to research spindle technology before purchasing a machining center.
-
Revisiting Some Hot Runner Fundamentals
What exactly does a hot runner do? If you’ve been in the injection molding industry for any length of time, you might think the answer is obvious, but it is not.
-
Treatment and Disposal of Used Metalworking Fluids
With greater emphasis on fluid longevity and fluid recycling, it is important to remember that water-based metalworking fluids are “consumable” and have a finite life.