Digital Platform Enables Remote Machine Troubleshooting
GF Machining Solutions’ My rConnect provides a virtual link between a machine and the company’s service and support team, giving live and historical data without the need to travel to a customer’s shop.
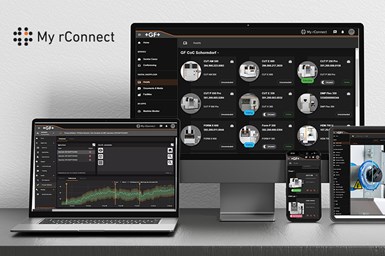
Source | GF Machining Solutions
GF Machining Solutions (GFMS) has launched its new My rConnect platform engineered for the company’s EDM, milling and laser texturing machines. The platform enables shops to connect any model of GFMS machine for fast, responsive and easily accessible service and support while also providing expanded digital capabilities.
My rConnect is completely cloud-based. Regardless, GFMS machines that don’t have network access and are connected to the Internet can also use the software.
A key benefit of bypassing the need for a direct connection is security. My rConnect is password protected and includes an extended level of protection where the system verifies user identity via text message or email code.
The GFMS My rConnect provides a virtual link between a machine and the company’s service and support team, often eliminating the need for a technician to travel to a customer’s shop. When problems occur with those machines that are networkable, shops create an event for that issue, and a service engineer will log in and ask for permission to access and view the machine via the live Remote Assist function to diagnose problems at the machine level. For non-networkable GFMS machines, the process is basically the same.
Within My rConnect, users can create groups, such as for the machines in various production facility locations. Once done, they can request any related documentation, such as manuals, for a particular machine. Instead of service having to send it, customers with My rConnect-connected machines can download needed documentation.
With a machine network connected to My rConnect, shops gain more digital capability. This includes access to current and future-developed applications that enhance the capabilities of customer machines, and the platform makes new or updated apps easy to acquire. GFMS can push the new apps or application update directly to a customer’s machines, notifying them when they log into a particular machine.
One such app is a new version of the company’s Job Recorder for wire EDMs and a version for its milling machines. The app lets shops record all the jobs they’ve done to generate efficiency reports based on how much time during the course of a day a machine worked on certain jobs.
Another app is the Machine Dashboard. It shows real-time machine status — whether it’s running, paused or off. For machines running, it shows the job being done and how long the machine has been working on it, in addition to all the previous jobs that have been processed on that particular machine and how long each of those have taken.
Related Content
-
CAM Automation Increases Mold Production, Quality
Mold builder switches CAM software package after 20 years to take advantage of innovative programming strategies that reduce mold machining programming and processing times.
-
What is Driving Mold Lifecycle Management Digitalization?
OEMs are looking to partner with suppliers to share and track data across the supply chain for advanced intervention and process management.
-
MMT Chats: Predictable Manufacturing and Incremental Gains Can Transform Moldmaking
MoldMaking Technology Editorial Director Christina Fuges catches up with the president of Eden Tool and Eden Manufacturing, Dave Tomic. We talk about predictable performance in moldmaking and the value of small incremental gains in an organization versus big change via disruptive technology. This episode is brought to you by ISCAR with New Ideas for Machining Intelligently.