Injection Molding Live Demos to Highlight First-Ever PTXPO
Major suppliers will be running injection machines in the first plastics industry trade show in the Chicago area since 2009.
The first-ever Plastics Technology Expo (PTXPO), coming March 29-31 at the Donald E. Stephens Convention Center in Rosemont, Illinois, will feature an array of injection presses running parts in live demonstrations (scroll down for Live Demo schedule). The show will also feature new technology in extrusion, blow molding and additives as well as an educational program in three Tech Talk theaters (scroll down for schedule). Here’s what you can expect from the injection molding exhibits, based on information available before show time:
KraussMaffei will have an 80-ton all-electric KM80-250PX injection machine on display. Utilizing the company’s APC+ software for dynamic control of the molding process, KM plans is to mold coasters from recycled resin with the machine automatically adjusting to changes in resin viscosity. The press will also be equipped with a KM LRX-50 linear robot for part removal.
Absolute Haitian will have the U.S. debut of the third generation of its all-electric machines, unveiling the Zeres III. Available from 44 to 1551 tons, the Zeres III features improved injection and clamp units, as well as the Sigmatek control, featuring Connectivity Plus for easier integration of auxiliaries and automated processes to create full cells and production lines. The Zeres also has integrated hydraulics to power core pull, ejectors, carriage movement and hot-runner valve gates.

At the show, Absolute Haitian will run a 135-ton ZE1200-300 with a two-cavity thin-wall cup mold in an anticipated cycle time of 12 seconds. The two 0.5-ounce cups will be molded from a 35-gram shot, with the tool utilizing valve gates that are powered by the Zeres’ integrated hydraulics.
Working in conjunction with the Zeres press will be Sepro Group’s Success 11X robot, equipped with Visual 2 controls. Part of the revamped Success Line, the 11X reportedly offers reliability, quality performance and 5-axis capabilities at an affordable price. The robot will stack parts on the non-operator side of the machine. Rounding out the machine cell will be a Conair chiller integrated into the Zeres’ Sigmatek control.

Engel will feature two molding machines in its PTXPO booth highlighting fast mold changes and LSR molding, with the assistance of booth collaborators Stäubli and Roembke Mfg. & Design Inc. For the quick mold-change demonstration, a hydraulic 85-ton victory tiebarless machine will be running two separate tools. By utilizing quick-change technology from Staübli, these molds will be swapped out in just 10 minutes from the last good part from mold “a” to the first good part from mold “b.” Both these molds, plus the duckbill valve mold for the LSR machine, were supplied by Roembke.

The quick-change tools will be molding a pair of tongs and a bowl, respectively. The tongs have 30-second cycle time and are molded from ABS in a 46.2-gram shot, with the two parts weighing 23 and 21.1 grams, and the remaining resin making up the sprue and runner. The fruit bowl has a cycle time of 31.2 seconds and a shot and part weight of 55 grams.
When switching tools, operators utilize Staübli’s mold-loading vehicle (MLV), which carries the new tool and receives the old one without the need for an overhead crane. Before sliding the old mold out, operators detach the Staübli quick-coupling water system. The molds and robot EOAT both utilize quick connects and RFID to ensure the proper tool and robot gripper are in place. The machine utilizes Engel’s iQ weight control for shot-to-shot consistency, and the parts are demolded and positioned on a conveyor by an Engel viper 12 linear robot.

The second machine in Engel’s booth, also running a Roembke tool, will be a 145-ton, all-electric e-mac 170-145 equipped for processing LSR. The application here is a duckbill valve molded from liquid silicone provided by Shin Etsu with a dosing system from Nexus. The machine is part of Engel’s stock program, comprising equipment it keeps at the ready in the U.S. for fast lead times. A viper 20 linear robot handles part removal. The all-electric machine with a compact footprint is well suited for cleanroom production.

Plustech will be partnering with Sodick for PTXPO and bringing two injection machines to Rosemont. Plustech is a joint venture between Sodick Co. Ltd. and Yamazen to market Sodick’s two-stage plunger injection molding machines. Plustech will be running its 110-ton GL100A-LSR with a 16-cavity LSR mold from M.R. Mold, which has also equipped it with a with a valve-gated cold runner. LSR metering will be handled by a Nexus Servomix X20 system. The X20, which allows molders to swap out material drums in just five minutes, features a maximum feed rate of 1000 cubic centimeters/minute and maximum pressure of 170 bar.
Plustech will also be showing its high-response 22-ton LP20EH3 injection machine from its LP series of micro-molding presses. The machine will run a high-precision mold built by Matrix Tool Inc., reuniting the award-winning combination from Plastics Technology’s inaugural Hot Shots parts competition. The machine has an ultrafast 2-3 millisecond response time and is capable of injection speeds up to 1300 millimeters/second.
On the Sodick metalworking machinery side, the company has recently unveiled iGroove technology for its ALP and ALN wire-EDM machines. iGroove works by rotating the wire so that its entire surface is used during finishing for high-efficiency machining. This function also eliminates the need for taper and reduces wire consumption since it can be fed through at a slower rate. Sodick will showcasing a ALN400G iGroove wire-EDM machine and AL60G sinker EDM machine. The AL60G will be dry run with cut samples on hand. The ALN400G iGroove, or iGE, will execute a hybrid cut where the wire will be cutting on skim passes without being submerged in the water tank so the iGroove feature is visible.
Tederic will introduce the Neo family of injection machines to North America. All Neo presses offer Keba controls, with the option of a 12-, 15- or 21-inch touchscreen. The new machine series includes six distinct lines: Neo T, E, Ec, H, Mv and Ms. These include servohydraulic toggle, all-electric, hybrid, two-platen and multimaterial machines.
iMFLUX will be showcasing its constant-low-pressure injection technology in collaboration with Japan Steel Works America at the JSW booth in a live machine display, as well as at its own booth. iMFLUX’s technology will be displayed on a JSW JADS Series medical-grade machine for cleanroom applications. Attendees can see how iMFLUX automatically adapts to shifts in viscosity, compensates for blocked cavities and more.
At the show, iMFLUX will perform a material transition to demonstrate the AVA (Auto Viscosity Adjust) capability, switching from PP (supplied by recycler/compounder/distributor KAL-Polymers) with 10 MFI to one with 40 MFI while maintaining a stable process without operator intervention.
The JADS Series features stainless-steel rails and rollers for the safety door; bushing-free greaseless tiebars; an added duct on top of the purge cover to exhaust contaminated purge air; white powder coating; J-Mag magnetic platens for easier mold mounting; and stainless-steel covers for high-use areas of the press.
Canon Virginia will introduce a new version of its Shuttle Mold System that supports machines from 450 to 650 tons. The company notes that this is the first time this size system will be shown publicly. The booth will feature a demonstration of the Shuttle Mold System and will highlight some use cases for the technology. Canon engineers will be on site to discuss specific applications and answer technical questions.
Wittmann Battenfeld will debut its new R9.1 robot controller, featuring the Quick New Wizard programming tool. It will also feature its Innovations Roadshow Truck, which allows attendees to watch live demonstrations of its molding machine control, temperature controller, robots and various auxiliaries.
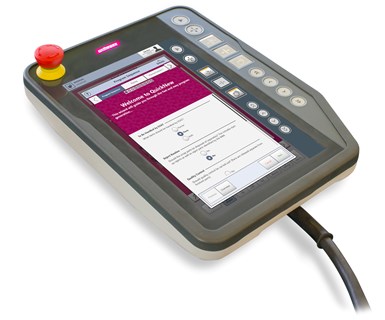
At PTXPO, Wittmann Battenfeld will introduce the new R9.1 robot controller, featuring the Quick New Wizard programming tool.
Savage Automation, which specializes in full automation cells and 3D-printed robot end-of-arm tooling (EOAT) for high-end injection molding, will showcase a unique EOAT created for a medical application. This tool was created for a four-cavity medical-device mold. The entire body of the EOAT is 3D printed in nylon 12 and features a vision system that inspects each part to ensure there are no black specks and that dimensions are within tolerance. The entire EOAT weighs just 1 pound, 9 ounces.
Beaumont Technologies will introduce a reorganization of its business into three distinct divisions. In January, Beaumont acquired a moldmaking operation in Sugar Grove, Pa., including more than 7,000 square feet dedicated to the design and development of injection molds. This will act as the hub of Beaumont’s new tooling division, giving the company what it calls a one-stop-shop for mold design and build, process validation and production, in addition to quick repairs and improved preventive maintenance for current production tools.

At PTXPO, Beaumont will introduce a new business organization, adding tooling and material characterization units to its traditional training and technology offerings.
Secondly, Beaumont will be opening a new facility in Cranesville, Pennsylvania, dedicated to material characterization. The 10,000-square-foot facility will offer Moldflow and Thermaflo material characterization and test-specimen molding. Beaumont says the facility, which has room to expand for additional material characterization services, will improve lead times on material reports.
Finally, these moves will allow Beaumont’s existing headquarters in Erie, Pennsylvania, to become dedicated to production of its injection molding technology products. Doing so will increase production capacity and improve lead times. In addition, Beaumont’s American Injection Molding (AIM) Institute will be offering a new service called Workforce Development, designed to help molders determine an individualized educational pathway that will ensure employees are proficient in their current roles and prepared to take on additional responsibilities in the future. The service is designed to identify and eliminate knowledge gaps within a company’s workforce.

Paulson Training will offer PTXPO visitors demonstrations of its new online learning platform—Paulson University. It’s said to make training employees seamless, regardless of their geographic location, with the ability to provide plastics-processing education anytime, anywhere and on any internet-enabled device. Instead of an office being set aside as a dedicated training space with specific sign-up times, the online university allows more flexible learning, including at home. Paulson University allows companies to link into their own in-house learning-management system (LMS), and it includes reporting, progress tracking and bonus training materials. At the show, Paulson will specifically be showcasing its new PET-ISBM course, which focuses on preform injection molding as well as stretch-blow molding.
Another computer station at the show will exhibit Paulson’s SimTech and SkillBuilder Active Lab Lessons. Designed by the Paulson Tech team, the custom lab lessons promote active learning so that as students progress through the course, they will solve a set of process problems based on what they’ve learned via Paulson’s simulation tools, SimTech and SkillBuilder. Skillbuilder Lab lessons offers specific guided lessons, and SimTech Lab lessons ask students to solve various setup and optimization problems.
Oerlikon HRSflow will offer information and some physical examples of its comprehensive product line running from small hot-runner nozzles to very large ones with multiple methods of actuation, including hydraulic, pneumatic, servo and servo plate. Newest is the S Series nozzle offering reduced pitch spacing for small components (see last month’s Keeping Up).
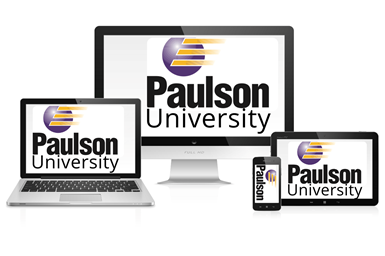
Paulson will introduce the online Paulson University at PTXPO, offering training anywhere on any web-connected device.
Progressive Components has added to its plate-sequencing product line, introducing its new Plate Retainer, designed to hold parting lines or retain floating mold plates. When molding machines vibrate, floating plates can drift from their intended location, resulting in stuck parts and mold damage. Progressive says its plate retainer is able to fit into tight spaces and keep plates secure. Progressive notes the retainer’s compact design, which requires very little machining and no timing or fitting during assembly. The SRT roller within the housing operates smoothly in greaseless applications. When installed, the plate retainer assembly is flush with the outside of the mold base and does not interfere with the machine’s tiebars.
DME will demo its new undercut thread technology and undercut applications featuring the iMold servo-driven units and controllers, as well as “S Cores” technology with collapsible cores as small as 6 mm.
Related Content
MMT's Most-Viewed March Content: Digitalization in Tooling, The Leadtime Leader Awards & More
March was a big month for MoldMaking Technology. Not only did we celebrate our 25th Anniversary, PTXPO, and announced the return of the Leadtime Leader award, we also continued to cover some of your favorite topics. Take a look at what you might have missed in March.
Read MoreMore Than Moldmaking at PTXPO 2023
The Moldmaking Pavilion returns to the Plastics Technology Expo (PTXPO) March 28-30, 2023, at the Donald E. Stephens Convention Center in Rosemont, Illinois, but there’s more to discover than moldmaking.
Read MoreSPE Mold Technologies Division Presents Moldmaking Award Winners
At PTXPO, the 2023 Mold Designer of the Year, Mold Maker of the Year and Mold Repair Technician of the Year were awarded to Chuck Heitmeyer, Pat Roussey II and John Demakis Sr., respectively.
Read MoreWhat is the Moldmaking Community Excited About?
As we continue to celebrate MoldMaking Technology’s 25th anniversary with a look back over the past quarter century, I asked readers during our recent Plastics Technology Expo (PTXPO) “What excites you about the future of moldmaking?”
Read MoreRead Next
New Online Training in PET ISBM
Paulson Training Programs adds PET injection stretch-blow molding to its library of online training courses.
Read MoreHot Runners Target Small Applications
Oerlikon HRSflow’s new S Series Nozzles can run engineering plastics and offer a compact product with a reduced pitch.
Read MoreMatrix Tool Sweeps 'Hot Shots' Competition
Working together with injection machine builder Sodick Plustech, this Pennsylvania molder and moldmaker won both prizes in Plastics Technology’s first-ever Hot Shots injection molded parts competition, held at Molding 2021.
Read More