Recycling Partners Collaborate to Eliminate Production Scrap Waste at NPE2024
A collaboration between show organizer PLASTICS, recycler CPR and size reduction experts WEIMA and Conair will seek to recover and recycle 100% of the parts produced at the show.
Around 8,000 communities across the United States have some variation of a recycling program that collects plastics from homes and finds a new life for it. These programs are widely diverse in accepted materials and success rates. Equally important are postindustrial scrap management programs at thousands of production facilities across the country. This May in Orlando, a completely different community will emerge with its own unique recycling program.
On May 6, a pop-up city will assemble in the Orange County Convention Center as some 55,000 attendees assemble for NPE2024, the largest plastics event in North America. They will come to learn, educate and network, but also show what they can do and see what others can do. Exhibitors will want to show that their equipment at its best and will be churning out parts in the process.
And what will happen to those parts, will they be tossed in a dumpster and forgotten? Not at NPE2024. It wouldn’t do. But it will take a coordinated effort to collect the materials flying out of machines at breakneck speed and irregular intervals, break them down and get them on to a new owner who can turn them into new products. Fortunately, exactly the right people for the job will be on hand.
A collaborative effort between Commercial Plastic Recycling (CPR), WEIMA, Conair and the PLASTICS industry association has set the ambitious goal of collecting and recycling 100% of the demonstration products produced.
CPR will collect materials throughout the exhibition halls, tracking when demonstrations are scheduled and emptying bins as they fill. The Tampa-based recycler will have around 60 staff on hand to move recyclable demonstration products to the recycling area outside the west hall, where tents will shelter equipment, recyclers and attendees from Florida’s frequent spring rains.
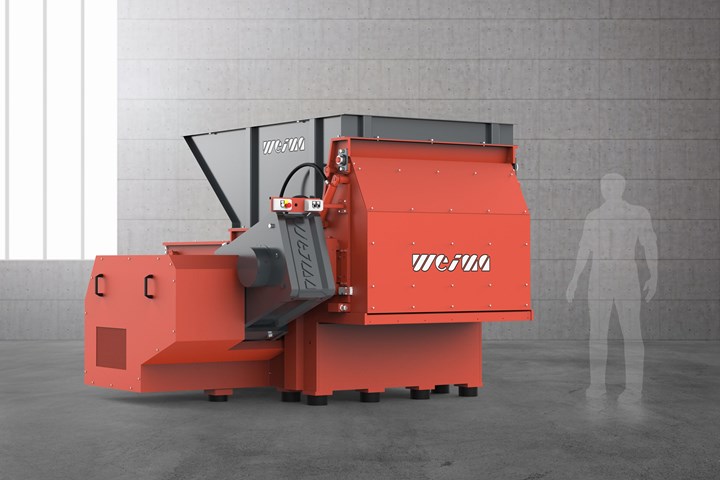
The WEIMA WLK 15 shredder is one of the machines the company will be setting up to handle plastic scrap at NPE2024. Photo Credit: WEIMA
There, WEIMA equipment will be shredding and grinding up that waste for efficient transportation. WEIMA will also be setting up a WLK 15 single-shaft shredder and two LM 600/1000 granulators. The shredder will be used in conjunction with one granulator to process bulky materials. The second granulator will be used for items that do not need to be pre-shredded.
Thanks to careful traffic planning, overhead ductwork and acrylic safety walls, NPE attendees will be able to walk through this temporary plant as it’s operating and watch as waste plastic is shredded and granulated.
From there, attendees can proceed inside to the Sustainable Solutions Showcase, located inside the west hall. There, exhibitors will demonstrate next steps in the processing of recycled materials — from regrind to pellets to new parts.
Conair will be set up in the Recycling & Sustainability Solutions Zone ( located inside the south hall), where it will use a conveyor and metal detection system to feed a Viper 1736 granulator. This granulator features Conair’s Smart Granulator control (SG Optmizer), which tracks energy use and load on the machine, controls grinder operation and enables predictive maintenance. The system will also include a negative pressure evacuation component to remove dust and fines to produce regrind that is ready for use.
“As a member of the PLASTICS industry association’s recycling committee, I have set up similar systems at NPE in the past, but not to this scale and focus. With our collaboration with other equipment suppliers and with CPR, we will meet our goal of recycling 100% of plastic scrap generated at NPE 2024,” says Dave Miller, general manager, size reduction at Conair.
Roots of Recycling at NPE Orlando
CPR immediately saw a need for on-site size reduction after being involved in the 2015 show, when 48 truckloads of material were used to carry plastics from Orlando to Tampa. “Now that WEIMA is doing the grinding operation on-site, that reduces the volume that we have to ship back to Tampa. We are shipping 1,000-lb boxes instead of 200-lb boxes. That really helps, because transporting air just kills you,” says Ben Benvenuti, CEO at CPR.
WEIMA has seen similar scenarios play out in other industries it operates in. The “Destroy Responsibly” campaign, now more than 10 years old, began with separating and compacting materials on-site at events in the wood industry.
According to Audrey Brewer, marketing manager at WEIMA, the companies’ areas of expertise complement each other well. Education, coordination, size reduction, logistics and market identification will all be critical to success.
“CPR has such a knowledge base of where plastic can go and what it can become, which is beautiful, because WEIMA focuses on getting it to the state where it can be taken elsewhere,” Brewer says.
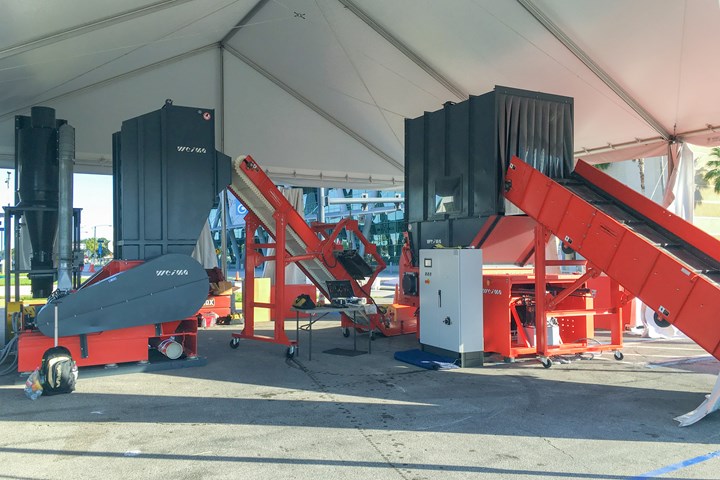
WEIMA equipment just outside the exhibit hall at NPE2018. NPE2024 partners are planning an even larger and more visible recycling effort for this year’s show. Photo Credit: WEIMA
In 2018, 89% of plastic produced at the show was collected for recycling. Recycling plans for 2021 were well under way when that show was canceled, and the team had already decided to go even bigger.
“We went through a mourning stage for all the planning work that had already been done, and then we asked them ‘are we still going to do this in 2024?’, and PLASTICS emphatically said, ‘Absolutely’,” Brewer recalls.
Patrick Krieger is vice president for sustainability at PLASTICS. “If you compare NPE to other trade shows, we have far and away the highest waste diversion rates,” Krieger says. “But we don’t want to stop there. One of our values is to move toward and promote a circular plastics economy. So, we want to make sure that we are diverting, reusing and repurposing as much plastic as possible at our show.”
Organizers, Exhibitors and Educators Contribute to Multifaceted Sustainability Conversation
The recycling effort at NPE 2024 will need many more collaborators to be a success, especially participating exhibitors. Exhibitors can register on the NPE website. The recycling team will also be reaching out to exhibitors to sign them up, with requests for 480-volt power supply serving as a key to which will be running equipment and may be making parts.
“Once an exhibitor signs up, our partner CPR will reach out to them to find out how much waste they will have, how many bins they will need. And the team will deliver the bins and pick them up when their ready to be emptied. So it’s going to be a hands-off experience for the exhibitor once they’ve signed up,” says Maureen Cameron, senior director of operations at PLASTICS. “We are telling all exhibitors that it is our goal for 100% of plastic on the show floor to be recycled, and we’re hopeful they will share that commitment.”
The recycling initiative will be part of a much wider conversation about sustainability at NPE. “NPE is going to offer a really interesting experience for the wide variety of people who show up, including over 30 educational sessions on recycling and sustainability,” Krieger says. NPE attendees can choose sessions from the “Sustainability, Recycling and Circularity” track, which will include topics such as new materials, advanced recycling technologies and spill prevention.
Related Content
Mold Slides, Traceability Device Save Space and Streamline Production
NPE2024: CUMSA is offering attendees a look at the Long Stroke Slide and its In-Mold Traceability technology, designed to provide more reliable and readable traceability on molded parts.
Read MoreUnveiling the Future: Dive Into NPE2024's Moldmaking Marvels
Get ready for the ultimate moldmaking extravaganza! Explore exclusive previews of cutting-edge technologies and solutions shaping the industry at NPE: The Plastics Show.
Read MoreLocalized Mold Temperature Control Reduces Knit Lines, Optimizes Melt Flow
NPE2024: Dynamic localized mold temperature control Heat-Inject Technology by Incoe Corp. demonstrates how the part surface quality and the filling of the cavity is optimized with relatively little effort using targeted heat pulses.
Read MoreHydraulic Gating Cutting Reliably Separates Molded Parts
NPE2024: Material displacement technology offered by Ermanno Balzi Srl enables precise separation of the molded part from the gate during the molding cycle.
Read MoreRead Next
How is an Aluminum Mold Energy-Efficient?
Nine ways aluminum molds save energy and production costs.
Read MoreTop Grade Molds Is All About Innovation and Collaboration
Top Grade Molds develops technology solutions with a heavy emphasis on R&D, recyclable material trends and collaboration.
Read MoreCertified Quality Management for Plastics Professionals – Materials to Tooling to Recycling
Why is certification of a shop’s quality management system to ISO 9001, AS9100, IATF 16949 or ISO 13485 so special? What does the certification signify? And what supports the paper behind the framed certificate?
Read More