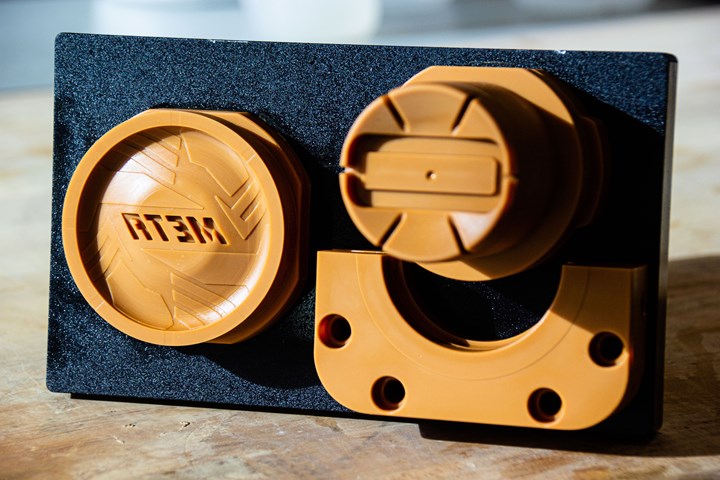
By 3D printing prototype molds with the Fortify process, DeMarini Sports has given its traditional moldmakers more time to work on production tooling, shortening lead times and increasing the company’s development capacity. Photo Credit: Fortify
Glen Mason, manager of advanced innovation and industrialization at DeMarini Sports (Hillsboro, Oregon), a subsidiary of Wilson Sporting Goods, went digital to solve his prototyping and workforce challenges.
“I started with the company in 1997, at a time when there were no injection-molded parts in baseball bats,” he says. “Today, they're an integral part of our success. DeMarini is the only U.S. manufacturer of baseball, fastpitch and slowpitch bats, many of which we make to order. We’re also vertically integrated, controlling the entire process from art to finished part. That means we own all the functions of manufacturing, from design and prototyping, to tooling and production.”
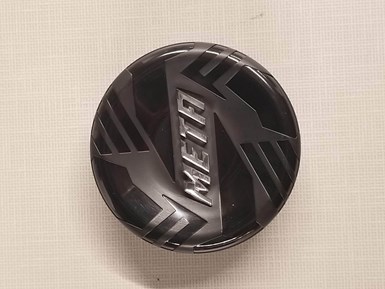
The mold for this DeMarini bat end cap required 12 hours to print and produced the desired 20 parts, cutting weeks off the development cycle.
Mason has felt the labor shortage pinch for some time now, a situation made even more painful by the need to iterate new part designs more quickly than ever before. He felt that additive manufacturing (AM, 3D printing) would solve many of these challenges but also knew that using direct printing of prototypes was not an option.
That’s because he needed to evaluate and test a range of polymers—many of them proprietary—which in turn meant he had to 3D print the molds used to make the parts rather than the parts themselves.
“I've solved much of my labor problem, but I also went into this to make more tools in less time.”
After extensive research and testing, he’s been proven right on all counts. “Fortify’s Fluxprint technology has greatly accelerated our product development cycle while also allowing me to save my moldmaking talent for where it’s needed most, our production tooling,” he says.
Combining Advanced Materials and Processes
Like the other 100+ employees at DeMarini Sports, Mason is proud to be part of the 80,000 square-foot “madhouse” in Hillsboro, Oregon. The team is responsible for every aspect of the design and manufacturing process, delivering continuous fiber and composite bats with names like Paraflex Plus, FNX Rising and Corndog 2.0, many with customizable knobs and end caps, handles and grips, and all of which are available with “sick” graphics and color combinations.
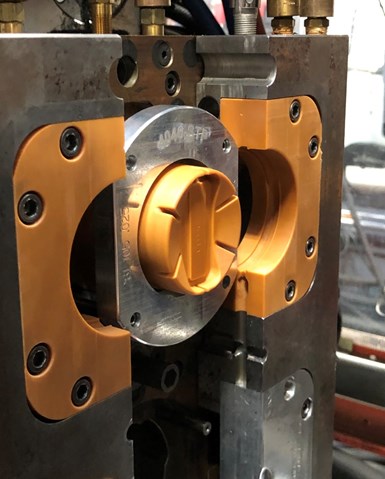
By incorporating ceramic fibers in the printing process and then aligning those fibers to the optimal orientation, this 3D-printed mold assembled in the press frame offers increased strength, stiffness and heat deflection.
“DeMarini and Wilson also support strategic customers outside of sporting goods with our advanced molding and manufacturing technology,” Mason says. “Our specialties are overmolding multiple materials and colors, including metal inserts, all in the same part to tune stiffness, performance, sound, feel and cosmetics. We combine that with film-insert molding, also known as in-mold graphics, where printed film is stretched into the mold and assembled onto the part during the molding process to create complex, durable graphics not possible with a secondary process. In general, we like to focus on parts that otherwise cannot be built—not just a lighter or cheaper version of a metal part, but a part that could only be created by combining advanced materials and processes.”
All of these manufacturing permutations are what keeps Mason awake at night. Not only must he and his moldmakers meet the ongoing demand for personalized, one-of-a-kind bats, but keep up with the company’s quest to stay ahead of the competition by designing new and more high-performance products. “We needed a way to iterate rapidly,” he says. “If we were to fail on a prototype, I wanted us to fail as quickly as possible, then move on to the next design. That’s what the Flux One has done for us.”
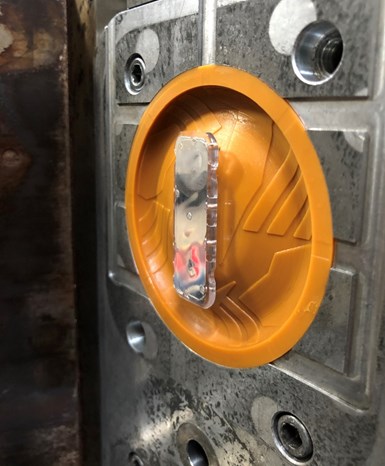
Overmolding is but one of DeMarini Sports’ many specialties. The company is said to focus on combining advanced materials and processes to produce parts that otherwise cannot be built, a goal made much easier with 3D printing technology from Fortify.
Fortify is a digital manufacturing company based in Boston, Massachusetts, and maker of the Flux One 3D printer. “We specialize in fiber-reinforced and filled photopolymers,” Fortify’s Vice President of Business Development Ben Arnold says. “These materials offer many benefits in terms of strength and functionality, but they can be challenging to print. For example, the particles within the fill material tend to clump together and settle to the bottom of the reservoir. It also isn't easy to get them to align in ways that increase product strength. Our system solves these problems.”
It does this via two patented technologies, the first being Continuous Kinetic Mixing (CKM). As its name implies, CKM prevents the clumping and sedimentation just mentioned by continuously recirculating the resin and its flakes of metal, flame-retardant materials and carbon or ceramic fibers. Depending on the resin and the additive used, the resulting mix might also be heated during the printing process, allowing the use of high-viscosity materials and further ensuring print consistency.
“We needed a way to iterate rapidly. If we were to fail on a prototype, I wanted us to fail as quickly as possible, then move on to the next design. That's what the Flux One has done for us.”
There’s also the technology that gives the Flux One its name. Fluxprint uses a magnetic field to align the individual fibers while printing. It comes equipped with pre-determined alignment patterns that generate optimized mechanical properties within the part, greatly reducing the chance of failure while providing increased strength and stiffness at strategic locations beyond what is possible with most 3D-printed components. This technology is suitable for applications where high strength-to-weight ratios are required or where surface hardness and wear resistance are critical.
One of these applications is 3D printing mold inserts and other mold components. Mason notes that the components coming out of the Flux One are both highly accurate and robust enough to meet his prototyping and product development needs. Ironically, though, one of the most significant benefits of 3D printing at DeMarini Sports has less to do with mold performance and more to do with the problem outlined at the start of this article: an industry-wide shortage of skilled labor.
Solving Labor Challenges
By taking a digital approach to prototyping, Mason can free up his moldmakers for the machining, assembly and testing production tooling. At the same time, he’s finding it easier to find people with the mindset and capabilities needed to operate a 3D printer. Because much of the machine setup and operation is automated, even an entry-level engineer or trained technician can turn a CAD model into a 3D-printed part without too much difficulty.
That's not to say that Mason has only been concerned about the allocation of human resources. Quite the contrary. “It’s been a twofer for me,” he says. “Yes, I’ve solved much of my labor problem, but I also went into this to make more tools in less time. The Fortify process is roughly twice as fast as machining, so not only can we build mold components much more quickly but use a less-skilled person to do it. It makes me labor independent, has reduced my costs significantly and if the tool design is flawed and doesn’t work, we can fix it and print another one.”
As a result, DeMarini Sports is actively looking for other customers to fill its production molding capacity. “When we can go faster, we need more designs to fill our mold-print capacity, so we can then look outside our internal creative process and entertain customer projects that we wouldn't normally have the bandwidth to consider.”
For More Information
Fortify / 857-274-0483 / 3dfortify.com
Related Content
How to Supply Cooling to Additive Tooling
Additive tooling provides limitless options for cooling a mold’s difficult-to-cool areas.
Read MoreA 3D Printing Retrospective
A personal review of the evolution of 3D printing in moldmaking throughout the past 25 years.
Read More3D Printing Enables Better Coolant Delivery in Milling Operations
Just like 3D printing enabled conformal cooling channels in molds, additive manufacturing is now being used to optimize coolant delivery in cutting tools.
Read MorePrecision Meets Innovation at IMTS 2024
After attending IMTS, it's clear that the integration of advanced technologies is ready to enhance precision, efficiency and automation in mold manufacturing processes. It’s a massive event, so here’s a glimpse of what the MMT team experienced firsthand.
Read MoreRead Next
Additive Tooling Goes Beyond Conformally Cooled Inserts to Simplify the Mold Build Process
Three ways that additive tooling is moving past conformal cooling to bring speed and efficiency to the overall tooling process.
Read MoreSelling the Value of Additive Tooling in a Mold
Gaining molder buy-in for a conformal-cooled mold insert requires communicating the mold’s total cost of ownership over the life of the project.
Read MoreWEBINAR: The Key to Digital Tooling Is Ceramic Fiber Reinforcement
If you do low-volume prototyping then this ceramic fiber-reinforced 3D-printed tooling option could be worth a look ... or listen. Check out this free webinar that presents best-use applications, part and mold design considerations and key lessons learned.
Read More