Zeiss, ORNL Introduce Fast, Automated Print Parameter Qualification at RAPID + TCT 2021
Zeiss ParAM (Parameter for Additive Manufacturing) comprehensively evaluates a set of parameters in less than 12 hours, reduces build failure rate, cost per part and improves reliability.
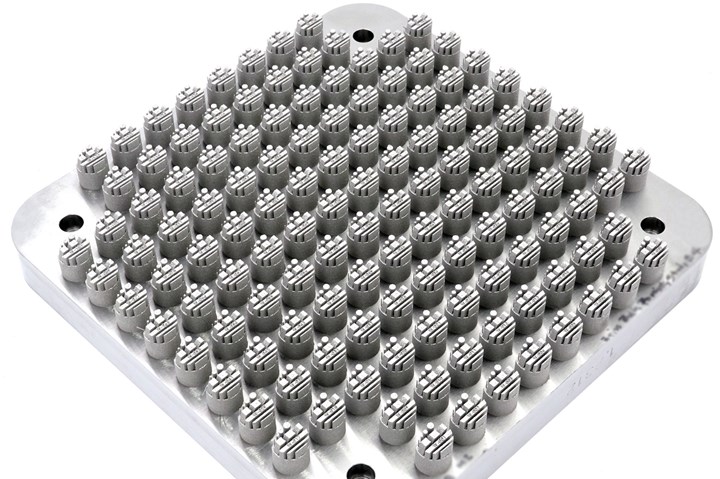
AM samples on a build plate. Photo Credit: Zeiss
Zeiss (Maple Grove, Minnesota) is featuring a new additive manufacturing (AM) solution service, ParAM (Parameter for Additive Manufacturing), at The RAPID + TCT Event in Chicago, Illinois this week, Sept. 13-15. Zeiss notes that print parameters are at the heart of AM to produce defect-free parts—the ability to print with a new material, adapt to change in powder characteristics, and increase print speed by increasing layer thickness to even placement of parts on the build plate are dictated by optimum print parameters.
Developed in collaboration with Oak Ridge National Laboratory (ORNL, Oak Ridge, Tennessee) at the Manufacturing Demonstration Facility—a Department of Energy national user facility at ORNL—the novel, fully automated solution is able to comprehensively evaluate a set of parameters in less than 12 hours.
“Our goal is for the user to start with a design of experiments, print coupons and evaluate best print parameters from the design of experiments plan in the same day, so they are ready to print parts the next morning,” says Pradeep Bhattad, product manager for Zeiss ParAM, a rapid parameter qualification solution.
According to Ryan Dehoff, section head for secure and digital manufacturing at ORNL, “Currently only a handful of alloys are qualified for printing and the majority of these are used in conventional manufacturing. However, there is tremendous benefit in developing and qualifying novel alloys specifically designed for AM. The current challenge is the qualification process and technologies that can accelerate the development of new materials are critical.”
Zeiss ParAM, using its unique test design and evaluation workflow, reportedly makes it a versatile solution for multiple applications. Examples include evaluating parameters to print defect-free parts with a change in powder quality or a degree of recycling; developing print parameters for thicker powder layers; qualification of a build envelope; evaluating or compensating for a laser performance in multi-laser systems; and creating a parameter to print deformation-free parts. One or a combination of these parameter optimizations can help reduce the build failure rate and make AM processes reliable, Zeiss says, while reducing the cost per part.
To learn more about Zeiss ParAM, visit booth# E8601 during RAPID + TCT, attend the October 21 webinar, or contact Zeiss at additive@zeiss.com.
Related Content
-
How to Supply Cooling to Additive Tooling
Additive tooling provides limitless options for cooling a mold’s difficult-to-cool areas.
-
Products and Services for Multiple Moldmaking Needs
New year, new technology roundup! Featured here is a collection of product offerings, from profile milling cutters to industry-specific CAD/CAM software to innovative hot work tool steels.
-
A 3D Printing Retrospective
A personal review of the evolution of 3D printing in moldmaking throughout the past 25 years.