Valve Gate Nozzle Offers Exceptional Wear Resistance
Adding to Husky Injection Molding Systems’ Ultra Helix Valve Gate nozzle lineup, the Ultra Helix 250 T2’s advanced design minimizes wear, provides high gate quality and longevity.
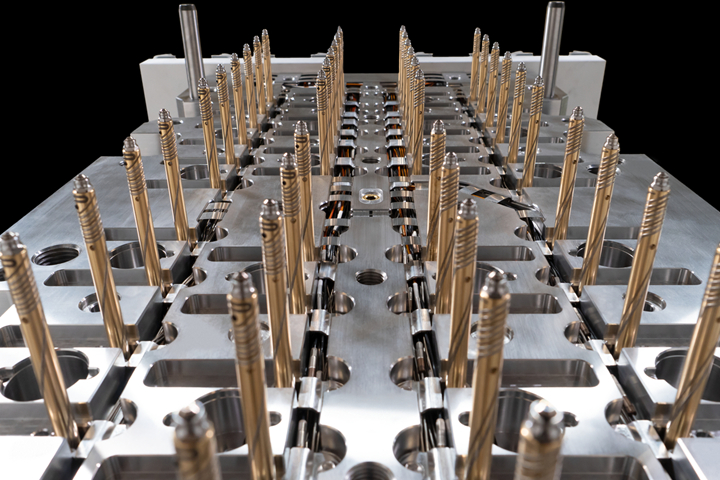
Photo Credit: Husky Injection Molding Systems
Adding to Husky Injection Molding Systems’ Ultra Helix Valve Gate nozzle lineup, the Ultra Helix 250 T2’s advanced design minimizes wear, provides high gate quality and longevity and was specifically developed to extend the benefits of the Ultra Helix technology to jobs for small part weights and difficult-to-access gate locations.
The Ultra Helix 250 T2 has a 12-mm nozzle bore for direct gating in locations that are said to be not typically achievable with larger nozzles, and pitch spacing down to 15 mm for high cavitation density and a small mold footprint.
Extended maintenance PX actuation is another added feature, designed for applications with leakage-prone resins such as TPE and PE. The addition of a stem seal paired with enhanced thermal management heater technology improves performance and is said to significantly optimize maintenance requirements, lowering risk and ownership costs.
Husky offers three actuation options for the Ultra Helix 250 T2. The Individual Pneumatic option, for example, offers pitch spacing down to 25.4 mms, providing easy access for maintenance with the ability to individually access valve stems without removing the backing plate. According to the company, both the plate actuated UltraSync-P or servo driven UltraSync-E options can achieve 15-mm pitch spacing.
Since the Ultra Helix 250 T2’s launch, Husky adds, the product has been applied to make high-quality precision parts from medical barrier closures and flow regulation valves to personal care products, food and beverage packaging, flip top closures and multi-material parts with limited gate access.
Part weights produced are said to range from less than 0.1 g to more than 4 g and are being made from resins that are prone to leakage including PP, HDPE, LDPE, TPE and TPV, in both single injection and multi-material applications.
Related Content
-
Solving Mold Alignment Problems with the Right Alignment Lock
Correct alignment lock selection can reduce maintenance costs and molding downtime, as well as increase part quality over the mold’s entire life.
-
Laser Welding Versus Micro Welding
The latest battle in finely detailed restoration/repair of mold materials.
-
The Ins and Outs of Hot Runner Temperature Control
A training checklist that explains the why and how of proper hot runner temperature control and system management.