Minimization of Core Shift Enhances Part Quality
The Mold-Master Symfill technology allows the melt to enter the nozzle runner channel from multiple sides, which has been proven to reduce barrel bow by up to 90%.
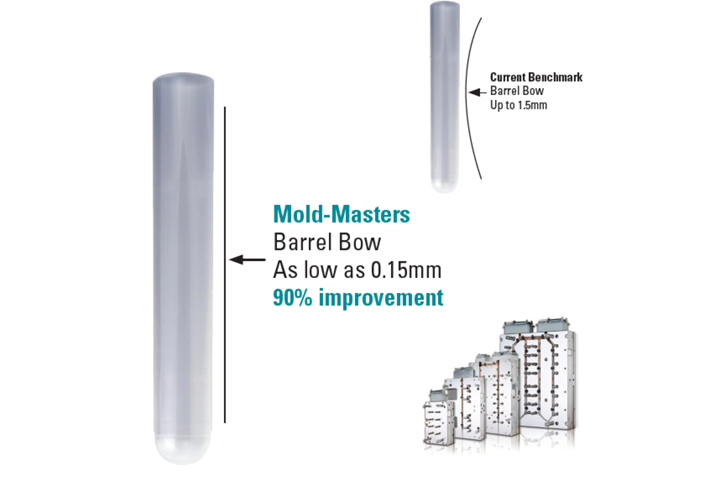
Photo Credit: Mold-Masters
According to Mold-Masters, its Symfill technology minimizes core shift to improve part quality (straightness) of cylindrical, center-injected components with an aggressive L/D ratio. This is achieved by enabling the melt to enter the nozzle runner channel from multiple sides, as opposed to the single-entry point of traditional designs.
Minimizing barrel bow offers many downstream processing advantages, Mold-Masters notes:
- Tubes roll concentrically in the labeling machine;
- Final stage throughput is increases;
- Machine downtime is minimized.
Examples of such components that would benefit from this technology include blood tubes, needle shields, over caps and other similar parts from the medical, cosmetic and stationary industries.
According to a European customer with a demanding container application, Symfill “delivered the tightest concentricity tolerance and perfect gate quality from the first shot.”
A recent blood vial application that leveraged Symfill is said to have reduced barrel bow by up to 90% (as low as 0.15 mm) by eliminating core shift. Symfill is exclusively available with Mold-Masters hot runner systems.
Related Content
-
The Secrets to Hard Milling Success
The Secrets to Hard Milling Success
-
Moldmakers Deserve a Total Production Solution
Stability, spindle speed and software are essential consideration for your moldmaking machine tool.
-
Revisiting Some Hot Runner Fundamentals
What exactly does a hot runner do? If you’ve been in the injection molding industry for any length of time, you might think the answer is obvious, but it is not.