Micro Drills Offer Precise Machining Performance
A new generation of Sandvik Coromant micro drills, the CoroDrill 462 and 862, are ideal for holemaking 1-3 mm in diameter.
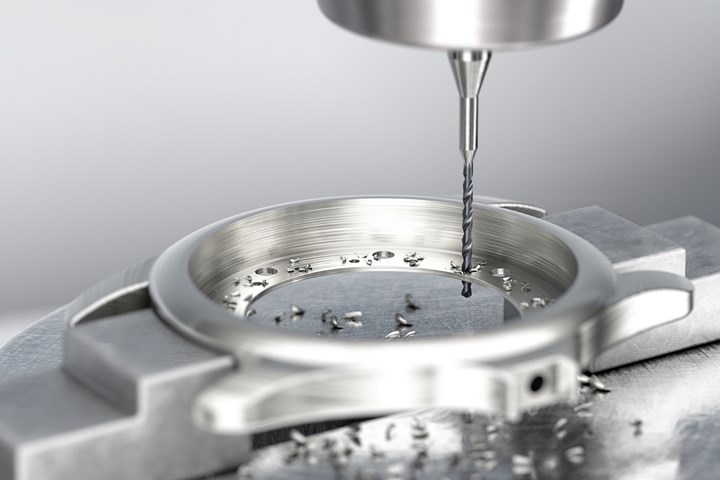
Photo Credit: Sandvik Coromant
Sandvik Coromant has launched two new micro drill families specifically designed for precision machining. The CoroDrill 462 with -XM geometry and the CoroDrill 862 with -GM geometry support industries with high demand for small part manufacturing, including medical, automotive, electronics, aerospace and mold and die making. Designed to cover a variety of workpiece materials, the micro drills offer precise performance where accuracy is key.
According to Sandvik Coromant, the drills have been adapted to overcome the challenges of micro drilling. Both the CoroDrill 462 and 862 can easily drill hole depths of up to 9xD when using external coolant; a through-coolant option is also available for drilling diameters of 1 mm and above, and hole depths of up to 16xD. This effective use of coolant help the tools to drill deeper holes, extends tool life and reduces the risk of chip jamming.
Individually, the CoroDrill 462 offers high-performance holemaking up to 3 mm and a drill depth of 6xD. Ideal for drilling both blind and through holes, the drill is capable of machining a variety of ISO materials, including ISO P, M, K, N, S, O and H.
The CoroDrill 862 is ideal for making holes from 1-3 mm in diameter in all materials, when used with internal coolant. In addition to conventional drilling, the CoroDrill 862 supports a variety of other drilling activities, including cross holes, stack drilling and drilling of convex and concave surfaces.
The micro drills are available as both off-the-shelf and customizable solid carbide tools. As part of the range, Sandvik Coromant has made it possible to configure the tools based on diameters, usable length, step-diameter length and shank diameter, for manufacturers who require a bespoke approach to micro drilling.
Customers also have the option of purchasing the CoroDrill 862 with a polycrystalline diamond (PCD) vein cutting edge. PCD is up to 100 times more wear-resistant than solid carbide, according to the company. In addition, PCD tooling is more accurate and can produce tighter tolerances than solid carbide tools. Applications include difficult-to-machine materials, such as titanium, aluminum, glass and ceramics.
The CoroDrill 462 and CoroDrill 862 will replace Sandvik Coromant’s existing R840 and current 862 micro drill assortments.
Related Content
-
Revisiting Some Hot Runner Fundamentals
What exactly does a hot runner do? If you’ve been in the injection molding industry for any length of time, you might think the answer is obvious, but it is not.
-
The Benefits of Hand Scraping
Accuracy and flatness are two benefits of hand scraping that help improve machine loop stiffness, workpiece surface finish and component geometry.
-
Moldmakers Deserve a Total Production Solution
Stability, spindle speed and software are essential consideration for your moldmaking machine tool.