Twin-Turret Multitasking Machine Is Suitable for Superimposed Machining
Operators can use Methods Machine Tools’ Nakamura-Tome SC-100X2’s twin turrets for superimposed machining or twin-spindle machining, achieving high speed and precision with both.
Share
Read Next
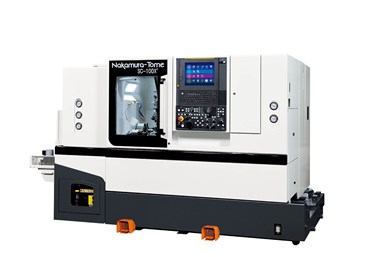
Photo Credit: Methods Machine Tools Inc.
Methods Machine Tools is now distributing Nakamura-Tome’s SC-100X2 twin-turret multitasking machine, which utilizes two tools on either side of the upper turret for superimposed machining. Methods spokespeople say this makes it well-suited for Swiss-style parts greater than 25 mm in diameter.
Superimposed machining lets shops take on complex contracts and complete them faster than other mainstream machining methods. Operators can also use the upper and lower turret simultaneously, giving the SC-100X2 the flexibility of a true twin spindle machine. The machine’s design also contributes to a faster cycle time while maintaining precision and accuracy in line with other Nakamura-Tome machines.
The SC-100X2 automatically unloads the workpiece once complete, minimizing manual intervention and downtime. When the machine completes a cycle, the parts catcher grips the part and places it on a conveyor, removing it from the machining environment.
Software from Nakamura-Tome enables users to use a FANUC 0i-TF Plus control to program superimposed and multi-turret jobs as easily as single-turret operations. The software package also includes Nakamura’s NT-Nurse system, NT-Smart Sign, NT-Navigator, oscillation turning and thermal compensation artificial intelligence.
Related Content
-
How to Analyze and Optimize Cutting Conditions to Reduce Cycle Time
Plastic injection mold design and manufacturing company puts NC program optimization software module to the test. The results were surprising.
-
Moldmakers Deserve a Total Production Solution
Stability, spindle speed and software are essential consideration for your moldmaking machine tool.
-
Tips for Tackling Mold Design, Machining, Cutting Tool and Wear Challenges
Tips for tasks ranging from reducing risk in part design and taking advantage of five-axis machining to refining cutting tool performance and reducing wear with guiding and centering systems.