Laser Workstation Facilitates Surface Enhancement of Tooling
Trumpf introduces the TruMark Station 7000. Available as a turnkey solution or integrated laser source, the workstation can be applied to a variety of materials and surface treatment processes.
Trumpf Inc. announces that it has developed laser technology, the TruMark Station 7000, that can be used for a variety of applications, from part marking, cutting and welding, to 3D metal printing and surface modification. Trumpf laser systems are used to process a range of materials including metals, plastics, glass, rubber, leather and many more. Mold builders can also utilize the laser to enhance the surface of their molds.
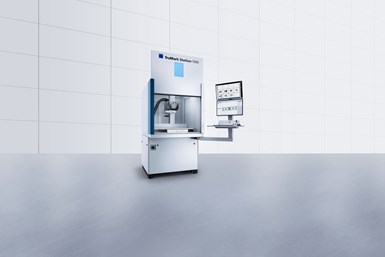
Photo Credit, all images: Trumpf
In the tooling industry, Trumpf notes, lasers are being used for part finishing, functional surface structuring, as well as creating hydrophilic and hydrophobic surfaces for plastic mold release. Solutions now offer average powers and shorter pulse durations ranging from femtosecond, picosecond and nanosecond pulses. Moreover, traditional machining methods used to create a polished, blasted, grained or ground surface can be improved with the use of a laser. Lasers enable complex part geometries to be processed with high throughput and repeatability, and without a consumable tool.
Trumpf’s TruMark Station 7000 is available as a turnkey solution or laser source that can be integrated into a production line. Said to have the largest work area out of Trumpf’s marking workstation products, the laser solution is ideal for automated batch production and large lot sizes. This cabinet can be equipped with TruMark and TruMicro laser sources ranging from 2W to 200W of average power.
Surface treatments that can performed on various metals. Left to right: Laser processing of titanium, stainless steel, copper and aluminum.
Related Content
-
What You Need to Know About Hot Runner Systems and How to Optimize Their Performance
How to make the most out of the hot runner design, function and performance.
-
Machine Hammer Peening Automates Mold Polishing
A polishing automation solution eliminates hand work, accelerates milling operations and controls surface geometries.
-
Questions and Considerations Before Sending Your Mold Out for Service
Communication is essential for proper polishing, hot runner manifold cleaning, mold repair, laser engraving and laser welding services.