Injection Mold Networking Software Application Reduces Mold Transfer Inefficiency
The Hub for Mold Transfer offered by RJG facilitates standardized processes, improves organizational efficiency and ensures proper mold and machine matching across global facilities.
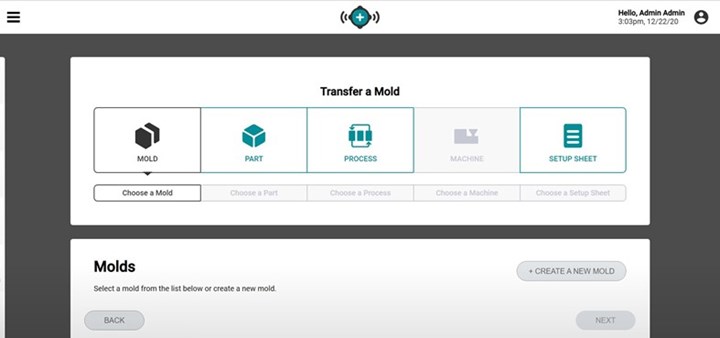
Photo Credit: RJG
RJG’s injection mold networking software, The Hub, now has a new application available: The Hub for Mold Transfer.
The Hub connects RJG’s CoPilot process monitoring systems to a single interface, enabling users to access all plant information globally, make data-driven decisions, increase visibility, decrease liability and improve operational efficiency. Alternately, RJG says the Hub for Process Analytics enables users to access real-time data from anywhere, review and export reports, view job audit reports, replay historical data and more.
Moreover, the Hub for Mold Transfer is said to permit an easy transfer of molds by automatically generating machine-specific setup sheets, recommending compatible machines and providing a database to store and share part, mold and machine documentation across the organization. According to the company, this application significantly reduces the risk of damage and poor quality by ensuring proper mold and machine matching.
The Hub for Mold Transfer also features:
- Facility asset database for machines, molds, parts and materials
- Mold match recommendations for fit and capability
- Universal process sheet database
- Machine-specific setup sheet database
- Automatically generated, machine-specific setup sheets
- Revision history.
Related Content
-
How to Make Data Work for Mold Productivity and Performance
The use of digital workflows improves the impact of mold design libraries, conformal cooling and machine learning.
-
What Is Scientific Maintenance? Part 1
Part one of this three-part series explains how to create a scientific maintenance plan based on a toolroom’s current data collection and usage.
-
Tolerancing in Mold Design, Part 2: Using GD&T to Address Conventional Tolerancing Issues
Mold designers can achieve a single interpretation of workpiece functionality when following the American Society of Mechanical Engineers Geometric Dimensioning and Tolerancing standard.