Horizontal Machining Center Showcases Upgraded Features, Design and Specs
Okuma has launched the 55,000-pound MA-600HIII with added X-axis travel capabilities and automatic tool change operations in less than four seconds.
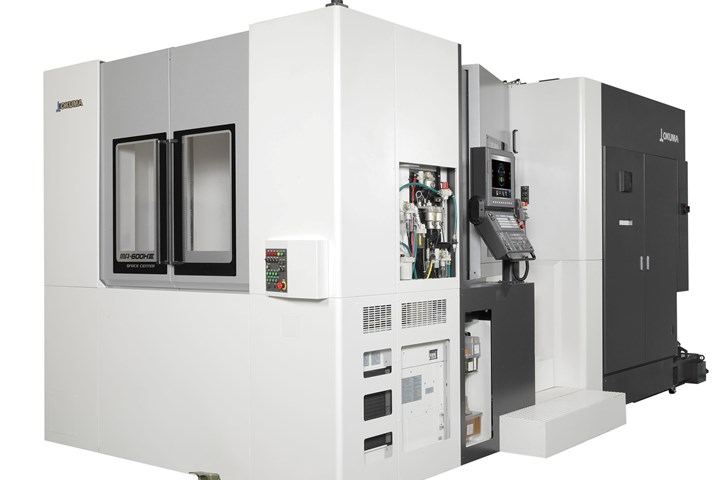
Photo Credit: Okuma America Corp.
Members of the management team at Okuma America Corp. have launched the Okuma MA-600HIII to join the company’s horizontal machining center (HMC) lineup. The new HMC adds to the MA-600H family’s machining capabilities by offering several new features in terms of specs, design and upgraded systems.
The MA-600HIII, boasting a table size of 24.80" x 24.80" and max loadable size of 41.34" x 47.24", weighs in at 55,000 pounds, ensuring structural stability and consistent precision machining operations. This machine has a larger work envelope than its predecessor, Okuma notes, with added X-axis travel capabilities. Additionally, the MA-600HIII is said to be able to perform automatic tool change operations in less than four seconds. Additional enhancements have also been made to Okuma’s thermal management technology, including decreased temperature deviation of the machine to an improved 7μ dimensional change per 24-hour period. This is particularly effective when faced with severe swings in the ambient temperature.
A 10K rpm standard spindle effectively handles a wide range of applications, from heavy-duty to high-feed machining. The enhanced spindle is now equipped with a thru-spindle coolant suction feature, which removes residual coolant inside the tool and spindle.
In addition, the HMC features an enhanced coolant management system, ball screw cooling for the X, Y and Z axes, an upgraded workspace design to prevent chip accumulation and improved chip evacuation functionality. The innovations are said to maximize uptime and allow for long periods of continuous machine operation.
To mitigate chip/coolant mixture settling in the bottom of the receiving tank, reduce time-consuming tank cleaning and increase machine operation uptime, Okuma has added a sludge-less tank technology, activating optimized filtering and liquid flow patterns.
The MA-600HIII’s flexible design enables a variety of automation applications, Okuma says. The workspace area can equip up to seven part loading/unloading ports or up to eight workholding clamp ports, which can help eliminate the need for complicated circuit arrangements for hydraulic applications. Up to 16 ports are available in the machine’s setup station, expanding part capacity and the possibilities for robotic applications.
Related Content
-
How to Analyze and Optimize Cutting Conditions to Reduce Cycle Time
Plastic injection mold design and manufacturing company puts NC program optimization software module to the test. The results were surprising.
-
Moldmakers Deserve a Total Production Solution
Stability, spindle speed and software are essential consideration for your moldmaking machine tool.
-
Developments in High-Speed Machining Technology
There have been many exciting developments in high-speed machining relative to machining centers and controls, tooling and CAD/CAM systems.