Axiom Group Increases Long Glass Fiber Manufacturing Capabilities with Injection Molding Compounder
Axiom’s new dual-screw compounding equipment from Krauss Massei further supports its commitment to R&D of new materials for the rapidly growing electric vehicle industry.
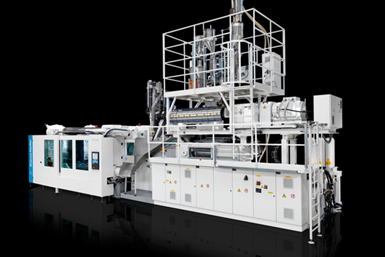
Photo Credit: Axiom, Krauss Maffei
Axiom Group (Aurora, Ontario, Canada) announced on Sept. 30 its investment in new technologies along with the University of Toronto through the purchase of a Krauss Maffei (Munich, Germany) 1300 Ton Injection Molding Compounder (IMC). This innovative technology integrates both compounding and injection molding into a single process, allowing Axiom Group to rapidly develop and test advanced materials for complete electric vehicle (EV) components.
“Engineering chassis components to the powertrain in the EV market will require new methods and solutions, and Axiom wants to be at the forefront of these technologies,” says Perry Rizzo, president and CEO of Axiom Group. “Our commitment to advanced compounding with the injection molding compounder will play a significant role in the integration of part design, advanced material strength enhancements and weight reduction.”
Axiom is currently working with various OEMs and vehicle platform developers in advanced compound integration. The new IMC machine supports this work, and the growth of new markets, by combining the benefits of both continuous extrusion and discontinuous injection molding, reportedly yielding parts with better values, increased efficiency and substantially decreased cost of raw materials by reducing the amount of additives needed. Axiom says it also enables the combination of different elements like graphene, carbon fibers and resins to create new compounds that are stronger than steel but also lightweight, cost-effective and easy to source. This engineering innovation further establishes Axiom Group as a leader in the industry for quality, cost and flexibility.
“With this innovative technology we are excited to develop new parts that can solve our customers’ toughest problems,” says Tom Gucciardi, plant manager for Axiom Group.
“The ability to rapidly develop and test new compounds for immediate production is yet another reason why Axiom’s customers can rely on us as the right partner for end-to-end product design, development and fulfillment,” adds Rizzo.
The injection molding compounder has 81-millimeter customizable twin screw extruders that are specifically designed to accommodate foaming technology. They rotate in the same direction, creating a uniform product under gentle processing conditions. The integrated long glass fiber dosing system also accommodates unusually long fiber lengths of 8-25 millimeters, which maximizes dimensional stability against shrinkage and warpage.
The compounding extruder also uses kneading blocks and tooth washers that enable the uniform dispersion of raw materials during production. The gravimetric metering system and continuously operating conveyer systems maximize efficiency by creating controlled throughput of raw materials and finished products.
Joe Daoud, laboratory coordinator at University of Toronto’s Department of Mechanical & Industrial Engineering will be consulting on the setup and initial trials of the injection molding compounder. The Krauss Maffei injection molding compounder arrived at Axiom Group’s Markham plant, where subsequent trials to create new compounds for the automotive industry will begin. Carbon fiber is one of the first materials Axiom Group plans to trial, with parts expected to be tested by the end of 2021.
Related Content
-
Design Strategy Tackles Big and Small Complexity Challenges for Southeastern Mold Builder
Delta Mold Inc.’s core values, engineering expertise, five-axis machines and molding capabilities help the team turn a proposal into a manufactured mold or part with custom design, finishing and assembly.
-
What Is Scientific Maintenance? Part 1
Part one of this three-part series explains how to create a scientific maintenance plan based on a toolroom’s current data collection and usage.
-
Cube Mold Technology Advancing Injection Molding
Injection mold design features a central rotating cube that can split and counter-rotate, with additional gear elements on the exterior.