Altair Partners With Simcon to Deliver Molding Simulation Platform
Simcon provides software tools that help customers design better parts, molds and find better injection molding machine settings.
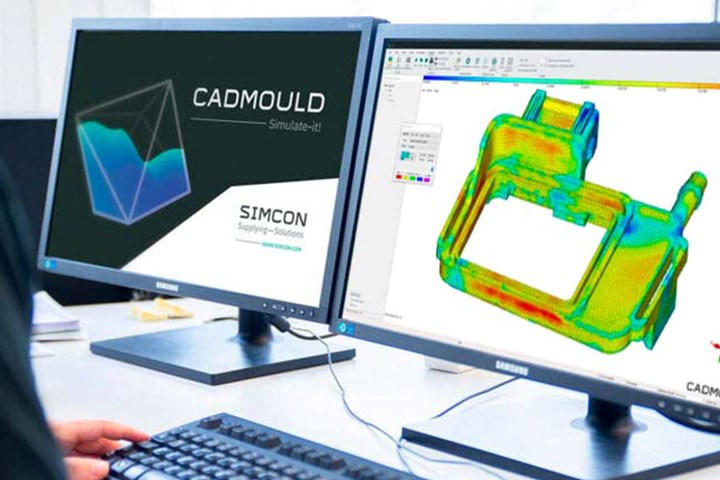
Photo Credit: Altair Engineering
Altair welcomes Simcon to its Altair Partner Alliance (APA). Headquartered near Aachen, Germany, Simcon specializes in plastics injection molding and provides software tools that help customers design better parts, molds and find better injection molding machine settings. This makes the injection molding process easier and more efficient, cost-effective and sustainable.
The addition of Simcon’s advanced simulation technology will give Altair customers a broader, more powerful set of virtual injection molding tools that integrate with other simulation-guided product design tools such as structural solvers, thermal solvers, crash testing software and metrology software.
Simcon’s software suite bolsters Altair’s existing polymer engineering offerings – which already includes materials data, CAE workflow and manufacturing solutions – and will help Altair customers drive the digital transformation of the plastics engineering value chain. By adding Simcon, Altair says it now boasts the most complete set of plastics engineering solutions and expertise. Simcon’s solutions enable customers to digitally revolutionize their entire plastics engineering value chain. With industry-leading precision and speed, customers can anticipate and fix issues like air entrapments, weld lines, hot spots, sink marks, shrinkage and warpage virtually — before molds are built.
Through the APA, Simcon will offer three packages for injection molding simulation and design optimization, and a separate package for optimized mold tryouts.
The simulation and design packages are:
- Warp It!: Enables customers to simulate the filling, packing and cooling phases of injection molding, including the shrinkage and warpage that occurs during cooling. It can also simulate sequential and cascading injection molding, and multi-component filling and inserts.
- Optimize It!: Gives users access to Varimos, a powerful automation, variant analysis and optimization tool. With it, users can work faster and more efficiently compared to traditional trial-and-error simulation. Varimos reportedly shortens engineering time from weeks to days by evaluating many design alternatives simultaneously.
- Varimize It!: Simcon’s complete package that offers users all of CADMould’s modules and Varimos. With it, users can simulate and optimize the entire injection molding process, including special methods like injection compression, foaming and rubber materials. This package also includes the Unwarp module, which can compute mold compensations and export warped part results in an ultra-high-resolution mesh, like for virtual metrology; it also includes an FEM module for structural analysis.
The optimized mold tryout management package is Varimos Real. This tool helps machine-setters achieve final, real-world refinements and optimize machine settings by setting up an efficient design of experiments (DoE) and learning from the results. With this package, users can improve development time and quality, assess the robustness of their manufacturing process and determine whether mold corrections are required. Lastly, it can optimize quality features that aren’t yet represented in simulation, such as parts’ surface qualities.
Simcon’s solutions are applied in the automotive, engineering, aerospace, consumer and medical sectors. According to Simco, through the APA, this technology will enable holistic, simulation-driven product design and manufacturing that will maximize performance and create more sustainable plastic products.
To learn more about Simcon and its injection molding technology, register for the introductory webinar.
Related Content
How to Improve Your Current Efficiency Rate
An alternative approach to taking on more EDM-intensive work when technology and personnel investment is not an option.
Read MoreHow to Select a Mold Temperature Controller
White paper shares how cooling channel analysis, which collects maximum pressure drop, total flow rate and heat dissipation, eases the performance evaluation of mold temperature controllers.
Read MoreIt Starts With the Part: A Plastic Part Checklist Ensures Good Mold Design
All successful mold build projects start with examining the part to be molded to ensure it is moldable and will meet the customers' production objectives.
Read MoreTolerancing in Mold Design, Part 2: Using GD&T to Address Conventional Tolerancing Issues
Mold designers can achieve a single interpretation of workpiece functionality when following the American Society of Mechanical Engineers Geometric Dimensioning and Tolerancing standard.
Read MoreRead Next
Are You a Moldmaker Considering 3D Printing? Consider the 3D Printing Workshop at NPE2024
Presentations will cover 3D printing for mold tooling, material innovation, product development, bridge production and full-scale, high-volume additive manufacturing.
Read MoreHow to Use Continuing Education to Remain Competitive in Moldmaking
Continued training helps moldmakers make tooling decisions and properly use the latest cutting tool to efficiently machine high-quality molds.
Read MoreReasons to Use Fiber Lasers for Mold Cleaning
Fiber lasers offer a simplicity, speed, control and portability, minimizing mold cleaning risks.
Read More