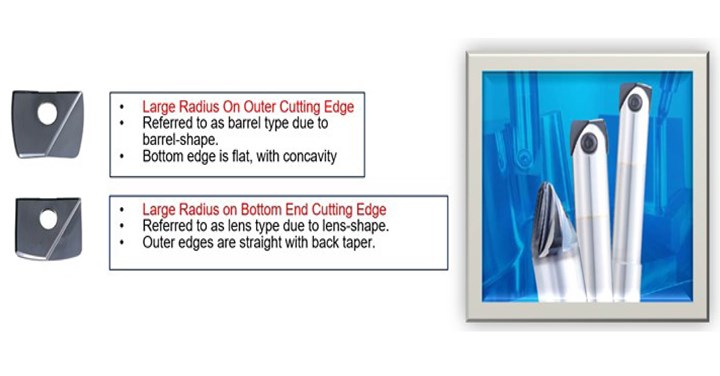
All photo credit: OSG USA Inc.
When mold shops made the jump from traditional machining to high-speed machining, they greatly reduced finishing cycle times. The high-speed machining centers offered more rigidity, higher rpm spindles (10K to 15K), better accuracy and faster controls. These same improvements have been made to cutting tools, which can also reduce cycle times and lengthen cutter life.
Mold builders aiming to reduce machining cycle times and improve surface finishes for mold work should consider barrel cutters and lens tools. Here we’ll explain their features and functions, niche applications and benefits—backed up with test cut data to illustrate the value of these cutting tools to mold builders.
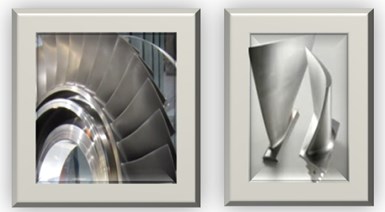
Figures 1 and 2.
If workpieces have larger free-flowing surfaces for which a shop typically uses a ball end mill or an end mill with a corner radius for finishing, it may be time to check out barrel cutters and lens tools. These cutting tools were developed for machining aerospace parts with large free-flowing surfaces (see Figures 1 and 2) and not very small, intricate parts. Medium to large cavities and cores, plastic injection and compression molds, forge dies, die-cast dies and some stamping dies are ideal applications for these cutting tools.
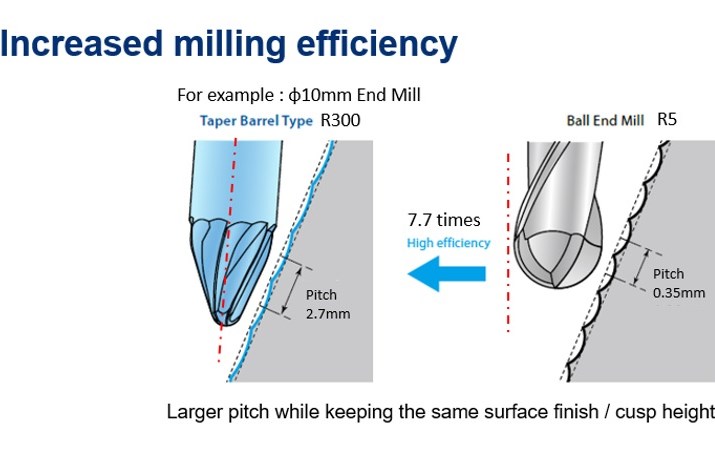
Figure 3.
When using barrel cutters and lens tools for finishing operations, step-overs and step-downs are very large compared to ball end mills or bull nose cutters. Most machining time is spent using ball end mills or bull nose tools to finish surfaces that require small depths of cut and step-overs (0.003 to 0.01 inch). However, barrel and lens tools can offer 0.08 inch for depth of cut and step-over. Also, surface finishes are much better due to fewer cusps compared to ball end mills and bull nose tools (see Figure 3).
Doing the math will reveal a dramatic reduction in finishing cycle times by half and more.
Related Content
-
Treatment and Disposal of Used Metalworking Fluids
With greater emphasis on fluid longevity and fluid recycling, it is important to remember that water-based metalworking fluids are “consumable” and have a finite life.
-
Solving Mold Alignment Problems with the Right Alignment Lock
Correct alignment lock selection can reduce maintenance costs and molding downtime, as well as increase part quality over the mold’s entire life.
-
Moldmakers Deserve a Total Production Solution
Stability, spindle speed and software are essential consideration for your moldmaking machine tool.