What You Put Out There Comes Back to You
Surely there is truth in this headline. I’ve seen it happen with my own eyes and recently witnessed it again when I participated with the Society of Plastics Engineers (SPE) Mold Technologies Division as its Mold Maker of the Year Award was presented to Geoff Luther, owner and president of A-1 Tool Corporation in Melrose Park, Illinois. The award was well-deserved.
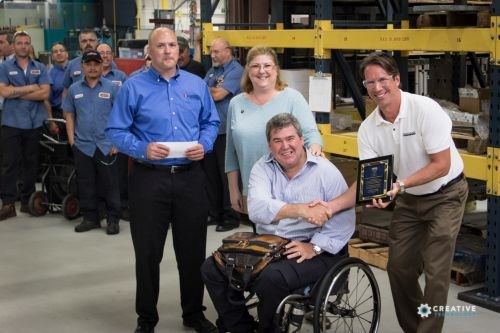
Geoff Luther (front, center) is presented with the SPE Mold Technologies Division's Mold Maker of the Year Award by, from left. Greg Osborn, Cynthia Kustush and Glenn Starkey. (Photos courtesy of Creative Technology)
Surely there is truth in this headline. I’ve seen it happen with my own eyes, most recently when I participated with the Society of Plastics Engineers (SPE) Mold Technologies Division as Chair Glenn Starkey of Progressive Components presented the division’s Mold Maker of the Year Award to Geoff Luther, owner and president of A-1 Tool Corporation in Melrose Park, Illinois. The award was well-deserved.
For several years now, Luther has worked tirelessly with both East and West Leyden Township high schools as part of an advisory committee to help them develop a first-class metalworking curriculum that exposes hundreds of students to advanced manufacturing career opportunities each year. His company provides tours for the students and instructors, plus he has recruited several students from the school to bring them into mold making and machining apprenticeships at A-1.
Greg Osborn from Synventive Molding Solutions, who serves as Education Committee Chair for the SPE Mold Technologies Division, nominated Luther and also attended the presentation. “Geoff is very well respected in the mold making community as the leader of one of the largest and most technologically advanced mold shops in the Midwest,” he says. In fact, not only does Luther lead an impressive moldmaking operation, he has demonstrated his commitment to his employees’ well-being, professionally and personally, by updating his company with new, state-of-the-art machinery; providing clean, organized and well-lit work areas, spacious break rooms and kitchens, a fully-equipped gym and even a sauna.
I happen to serve with Geoff on the Education Committee of the American Mold Builders Association (AMBA) Chicago Chapter, as does Greg Osborn, and I can say that there is no lack of enthusiasm or energy in the way Geoff gives of his time and experience to help us reach out to other school districts, their instructors, advisors and students.
“Geoff has inspired us all by sharing his experience with building solid relationships at the Leyden high schools,” says Francine Petrucci, AMBA Chicago president and chair of its education committee. “His strategies for recruiting apprentices is so valuable and has provided our committee with a strong foundation for launching similar efforts on a wider scale across northern Illinois.”
As part of his recognition, Geoff was presented with a plaque for himself and a scholarship check for $500 that must be given to a trade-related school or program of the honoree’s choice. Luther has chosen Leyden Township’s metalworking program as the beneficiary.
As I said earlier, you get back what you put out there, and I believe Geoff Luther is a fine example of someone who gives back to his industry without reservation and our industry is most willing to recognize and thank him for his efforts. Congratulations, Geoff.
Related Content
-
Making Quick and Easy Kaizen Work for Your Shop
Within each person is unlimited creative potential to improve shop operations.
-
Unique Mold Design Apprenticeship Using Untapped Resources
To help fill his mold design skills gap, Jeff Mertz of Anova Innovations, is focused on high schools and underprivileged school districts, a school that has lower graduation and college entrance rates. The goal is a student-run enterprise.
-
Confronting the Mold Design Talent Drought
Recently, I reposted on LinkedIn the results of an informal survey we conducted, which revealed a shortage of skilled mold designers. It quickly gained a lot of traction. Given the response, I thought I'd summarize the feedback and keep the conversation going.