
The cavity plate of a 60 × 89-inch aluminum production tool for low-pressure/structural foam molding is being milled on the Fooke Endura 704Linear. CDM estimates it could rough and semi-finish/finish the large tool two to three times faster on the Fooke than on any other equipment in its shop. Photo Credit: CDM Tool & Mfg. Co.
Established in 1962, injection molding toolmaker CDM Tool & Mfg. Co. LLC serves customers in the packaging, logistics, appliance/household goods, off-highway/agricultural equipment, motorcycle, industrial and automotive industries. The company operates from a 40,000-square-foot (3,716-square-meter) facility in Hartford, Wisconsin, northwest of Milwaukee. It produces molds for straight injection, low-pressure/structural foam, gas-assist, 2K/overmolding and stack molds sized to fit presses with clamping pressures between 50 and 6,600 tons/tonnes, although 1,000 to 3,000 tons/tonnes is considered CDM’s sweet spot. These large tools are produced in aluminum or steel, for prototype and production programs (Class 101 to 105), with up to eight cavities and typically with lots of complex side action.
With a team of 40, the company produces 40 to 60 new molds annually and repairs or makes engineering changes to 60 to 100 additional molds built by CDM and other moldmakers. The company also provides custom CNC machining of large metal parts for prototyping, automotive, aerospace and composite layup molds.
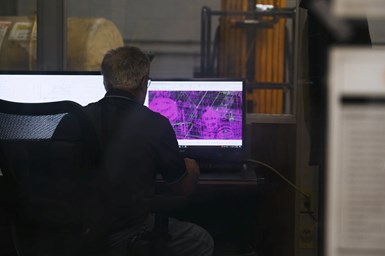
CDM Tool & Mfg. Co. is known not only for the large size of some of its molds, but also for its high accuracy, which CEO/Owner Stephen Hansen credits to CDM’s team of experienced and highly skilled tool designers and machinists, as well as investment in high-quality CNC machines. Photo Credit: CDM Tool & Mfg. Co. LLC
Not only is CDM known for the large size of some of its molds, but it also is renowned for its accuracy. Owner/CEO Stephen Hansen explains that the company has produced molds with tolerances as tight as 0.0006 inch/0.0152 millimeter over a 140-inch/3,556-millimeter span and 0.0014 inch/0.0356-millimeter over a 23-foot/7-meter span. As a consequence, CDM invests in high-speed/high-accuracy equipment capable of handling the large blocks the company so often cuts and it works to attract and retain a team of highly skilled and experienced tool designers and machinists.
Hansen says the company’s business strategy is not to bid on programs that would immediately have to be outsourced to other moldmakers — either local or offshore — but rather to play the long game and build solid relationships as a dependable supplier to its customers.
Capacity Constraint
In 2017, CDM was busy and starting to feel capacity-constrained, so Hansen searched for the company’s next CNC machining center to increase efficiency and production capacity. Although CDM already had a 3+2-axis mill and several four-axis mills, the team wanted to reduce setups further, so it targeted a true five-axis machine. In addition, given CDM’s reputation for on-time delivery and ability to hold tight tolerances, high-speed accuracy and repeatability were non-negotiable, as was the ability to run unattended nights and weekends. Also, given the block sizes the team regularly machines, a big work envelope was very important — especially since multiple smaller components can also be ganged up on a large machining center for high efficiency. Furthermore, since CDM produces tools in both aluminum and steel, the team wanted a versatile mill to semi-finish/finish steel and rough and semi-finish/finish aluminum.
Hansen looked at products from several machinery OEMs, eventually whittling the list down to three suppliers. Then, local distributor Manske Machinery Inc., which had sold and serviced other CDM equipment, suggested that Hansen look at mills from German machinery OEM Fooke GmbH, which Manske represented.
“There were several things that impressed us about Fooke,” recalls Hansen. “First was the size and capabilities of their machines. Second was how reliable we heard they were based on our research. Third, we liked their service and support. And fourth, they had a machine already being built that fit our sweet spot and would allow us to put a machine on our floor in much less time.”
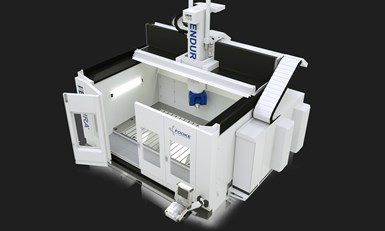
The five-axis Fooke Endura 700Linear series is equipped with a large cutting envelope, large toolchangers, lasers for tool checkoffs, CMM probes, Heidenhain or Siemens controllers, Fischer or Kessler spindles and the company’s thermal decoupling technology. Photo Credit: Fooke GmbH
Hansen was steered toward Fooke’s Endura 700Linear line of milling centers. Not only were they supplied standard with a range of valuable features, but the machines had a usable cutting area of 2,200 × 3,500 × 1,500 millimeters/86.61 × 137.8 × 59.06 inches, could handle workpieces weighing up to 60,000 pounds/27,216 kilograms and were equipped with spindles capable of running at 24,000 rpm. “Based on those specs, there wasn’t much we made that wouldn’t fit on a machine with those capabilities,” Hansen adds.
High-Speed, High-Accuracy Linear-Drive Mills
Fooke was established in 1904 in Borken, Germany, and is still a privately held, family-owned operation backward integrated to steel fabrication and welding. The company designs and produces large-capacity, high-speed/high-precision five-axis gantry and traveling-column mills, as well as friction stir welding machines. Fooke has produced five-axis machines for over 30 years and has been a leader in developing five-axis gantry mills with linear drive motors. Customers primarily fall into the automotive, rail and aerospace industries and roughly 30% of all mills are sold to moldmakers. In addition to sales, services and manufacturing facilities in Germany, Fooke also maintains facilities in Yokohama City, Japan and Shelby Township, Michigan.
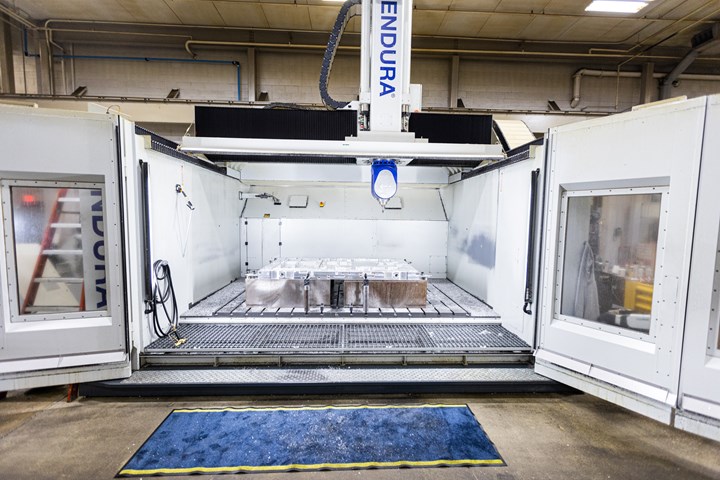
CDM invested in the Fooke Endura 704Linear milling center owing to its large usable cutting area of 86.61 × 137.8 × 59.06 inches, the ability to hold blocks weighing up to 60,000 pounds and spindles capable of running at 24,000 rpm. Photo Credit: CDM Tool & Mfg. Co. LLC
The 700Linear series of gantry mills has been in production since 2004 and is the closest Fooke comes to offering a standard production machine with a short lead time; all other models are highly customized/built to order. Still, many components can be modified even on 700Linear mills. In addition to tool changers holding up to 68 tools, machines can be configured with CNC controllers from Heidenhain GmbH or Siemens AG and spindles from Fischer Spindle Group AG or Kessler Group. Fooke will install standard or build custom units if customers require palletization systems. Additionally, 700Linear models are modularly expandable in the X-axis (the XL and XXL versions), which extends reach from 1,500 to 2,200 or 5,500 millimeters/59.06, 86.61 or 216.5 inches. The machines also can be configured to mill aluminum, cast iron, steel, carbon and glass fiber-reinforced composites and modeling block.
With a sturdy, self-supporting monoblock design, this family offers a large machining area in a relatively small footprint and doesn’t require a particular foundation beyond standard industrial floors. In addition to a direct measuring system for X,Y, Z, C and A axes, a laser for tool checkoffs, and a coordinate measuring machine (CMM) probe, four different milling heads are available for this model (CDM ordered the 704 model).
Like all Fooke mills, the 700Linear series is equipped with the company’s thermal decoupling technology, which insulates and protects workpieces from short-term temperature fluctuations from the outside environment and the machine itself to help ensure high-precision cutting. Additionally, all mills use linear drive rather than ball/screw drive motors, which are much faster, more dynamic and less prone to wear and tear.
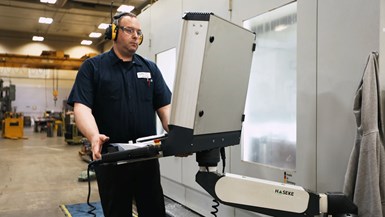
Given its five-axis capabilities and large cutting envelope, CDM can mill large workpieces or gang up several smaller components on the Fooke and run unattended for over 100 hours on a single setup, significantly increasing shop productivity. Photo Credit: CDM Tool & Mfg. Co. LLC
“Linear drive mills don’t take as thick a chip out but, as a consequence, they are more dynamic and have a much higher feed rate so that they can cut much faster,” explains Marco Kotonski, president and CEO of Fooke USA Inc. “Fooke mills offer the highest dynamics, reliability, surface finish, accuracy and after-sales service support. And 700Linear machines are very versatile, can cut large workpieces or multiple smaller ones and are available with the shortest lead time, which can be a major factor for some customers.”
Although in North America, the Fooke USA team tends to highly customize after-sale service, the company offers some standard maintenance programs, including its 36Plus preventative maintenance, measurement and alignment services, remote service support, customized training, overhaul and modernization service, and a valuation and certification program for Fooke machines for resale.
Big Molds: Fast and Accurate
CDM’s new Fooke Endura 704Linear mill arrived in the first quarter of 2018. A good example of the kinds of tools CDM regularly cuts on the machine is a large aluminum mold — with a finished size of 60 × 89 inches/1,524 × 2,261 millimeters — for a production program using the low-pressure injection/structural foam molding process. The team used the Fooke for all milling work on the cavity and core of this mold owing to the size workpiece the machine can hold, its high cutting speed, high rpm spindle — which allowed for extremely fast roughing, as well as semi-finish and finish machining of the block — the machine’s five-axis capabilities, which enabled CDM to machine all the fine details in a single setup, and its ability to cut to tolerances of better than 0.0152 millimeter/0.0006 inch over the span of the mold.
“This mold had a lot of intricate detail and radii that the Fooke handled easily,” remembers Hansen. “For example, the core block had a significant number of ribs, which the machine’s speed — both its inches-per-minute and its high rpm — easily tackled. The mold didn’t require a high polish, but the good surface finish we achieved ensured any polishing we did do was minimized. In fact, I’d estimate that we were able to produce this mold two to three times faster on the Fooke than we could have on any of our other machines.”
“Not only is the machine durable, reliable, low maintenance, repeatable, really fast and very accurate, but its size allows us to cut really big blocks or to gang up several smaller mold components and achieve run times of over 100 hours with a single setup, which really enhances our productivity.”
If he knew then what he knows now, would Hansen still purchase the Endura 704Linear? “We’d definitely buy the same machine again,” adds Hansen. “In fact, we will buy another Fooke. The only thing we’d change is that the company has added some newer technology since our machine was delivered. They’ve improved damping and made rough machining of steel more pervasive. Also, when we bought our Fooke, we didn’t know for sure if these machines were as reliable as we’d heard. However, we now definitely know they are. We’ve been running our machine two shifts a day, seven days a week for five years and we’re still on our first spindle, which is running well with more than 20,000 hours on it. If you treat the machine well, it will definitely perform for you.”
What features does the team like best? “Not only is the machine durable, reliable, low maintenance, repeatable, really fast and very accurate, but its size allows us to cut really big blocks or to gang up several smaller mold components and achieve run times of over 100 hours with a single setup, which really enhances our productivity,” says Hansen. “We can directly attribute a 10-15% increase in production capacity to the installation of the Fooke. Another benefit is that the machine didn’t require a special foundation, which otherwise adds to the cost and time it takes to get most CNC centers installed and up and running.”
Related Content
The Ins and Outs of Hot Runner Temperature Control
A training checklist that explains the why and how of proper hot runner temperature control and system management.
Read MoreMaintaining a Wire EDM Machine
To achieve the ultimate capability and level of productivity from your wire EDM on a consistent, repeatable and reliable basis, regular maintenance is a required task.
Read More6 Ways to Optimize High-Feed Milling
High-feed milling can significantly outweigh potential reliability challenges. Consider these six strategies in order to make high-feed milling successful for your business.
Read MoreHow to Eliminate Chatter
Here are techniques commonly used to combat chatter and guidelines to establish a foundation for optimizing the moldmaking process.
Read MoreRead Next
MMT Chats: COVID, Communication and Customers with CDM Tool & Mfg
CDM Tool & Manufacturing expedited and maximized resources with supplier support to be part of a solution in the fight against the coronavirus.
Read MoreNew Ownership Revitalizes Precision Mold Builder with Heavy Capital Investments, New Management Style
A rich history in mold building, recent technology investment and a shift in management philosophy re-energizes a Midwest precision mold builder and contract CNC machine shop.
Read MoreHow to Tackle Sophisticated Molds
Considering that semi-finishing and finishing processes account for 70 percent of the milling of a mold, it becomes obvious that using such a system can lead to huge productivity gains.
Read More