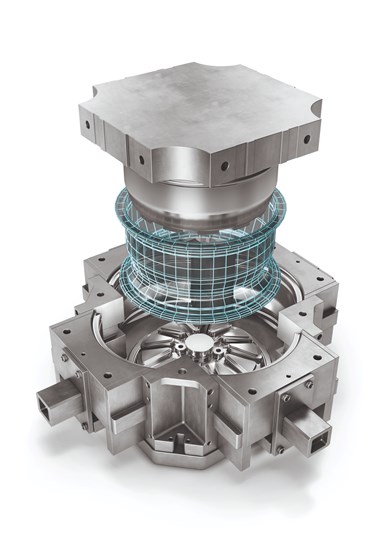
Wheel rim mold demonstrates the importance of cutting tool design to improve process reliability during machining. Photo Credit, all images: Walter AG
Most molds are made from hardened or heat-treated tool steel or hardened metals, and are challenging to produce, especially as their complexity increases. Strong forces also impact the cutting tools that machine the cores and cavities and make the channels and supply systems for coolant or hydraulic fluid. These aspects of moldmaking make process reliability a challenge. A good example is tool breakage during deep-hole drilling or increased tool wear due to material hardness and toughness — both negatively impact the final part’s dimensional accuracy and surface quality.
Making the right cutting tool choice to meet the complex requirements and conditions involved in mold machining is a challenge, especially for many small- and medium-sized shops that often lack the time and workforce to develop optimal machining strategies.
Design Considerations
Here are three cutting tool design considerations for improving your process reliability and cost efficiency when deep-hole drilling, producing internal threads or machining highly brittle mold materials.
1. When deep-hole drilling, use a pilot drill with land design that places the carbide mass directly behind the cutting corner or in the area where the most significant cutting force and highest temperature occur. Also, use a deep-hole drill up to 30x DC. The radially located lands dissipate the increased temperature created by the cutting operation into the chip.
This unique positioning of the guiding chamfers results in excellent straightness of the holes produced with a reduced tendency to vibrate. The result is drilled holes with very high dimensional accuracy and surface quality. This strategy and design increases the drill’s stability in the precise area, ensuring productivity and reliability, even in the case of inclined exits or cross holes when particularly high mechanical loads are placed on the drill.
This unique positioning of the guiding chamfers results in excellent straightness of the holes produced with a reduced tendency to vibrate. The result is drilled holes with very high dimensional accuracy and surface quality.
2. Consider the drill’s substrate and coating as they are essential to high heat resistance. For example, carbide accommodates higher temperatures than conventional drills, while a TiAIN/AICrN coating (grade WJ30EJ) increases the hot hardness of the drill even more.
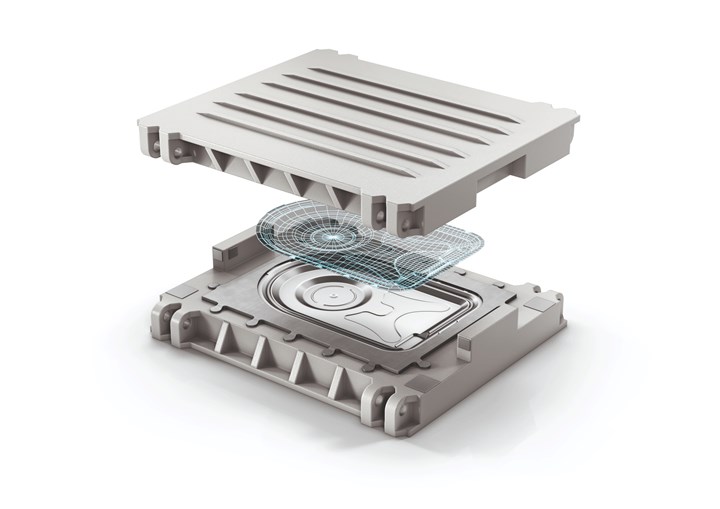
A washing machine back panel mold highlights how the right cutting tool can improve cost efficiency when machining highly brittle mold materials.
3. When drilling the fittings that connect coolant channels to a mold made of hardened material, use an orbital drill thread milling cutter to machine the core hole and thread and chamfer, if necessary, in a single operation. The milling geometry on the face produces stabilizing forces in the axial direction, improving stability when milling and decreasing deflection.
This solution reduces the need for radius corrections and slows down tool wear significantly. Also, a 15º helix angle and internal coolant offer reliable chip evacuation, enabling a mold builder to machine even tougher steels and deeper threads reliably.
Related Content
-
Machining Center Spindles: What You Need to Know
Why and how to research spindle technology before purchasing a machining center.
-
Moldmakers Deserve a Total Production Solution
Stability, spindle speed and software are essential consideration for your moldmaking machine tool.
-
Maintaining a Wire EDM Machine
To achieve the ultimate capability and level of productivity from your wire EDM on a consistent, repeatable and reliable basis, regular maintenance is a required task.