Tackling Supply Chain Troubles
The operations manager for a contract manufacturer specializing in plastic injection molding shares how to tackle supply chain challenges.
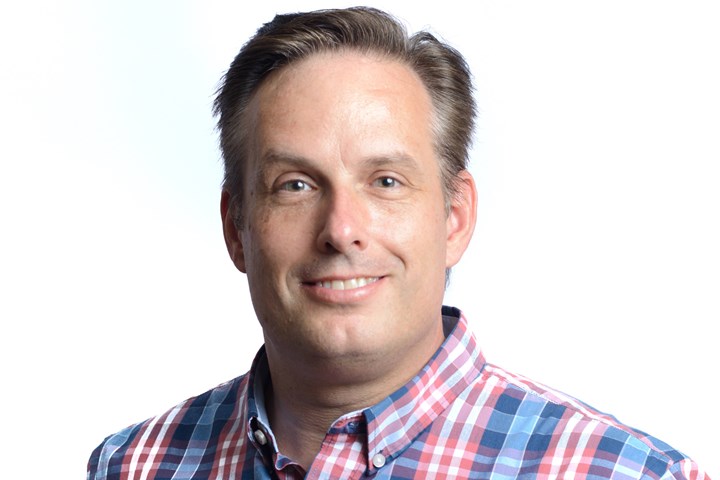
Current EAB member James Jergens shares the realities of supply chain challenges.
On-time delivery is one of the key metrics we measure weekly, and we fell off the cliff this past April. Delays from key suppliers for steel, components, hot runner systems and mold bases were the root cause.
For Ernie Green Industries (EGI), where I was the former operations manager, it started with steel delivery extensions of 5-10 business days followed by extended lead times for mold bases, missed due dates on existing mold base orders and then delays in hot runner deliveries from suppliers with global production and supply chain systems. Our overseas suppliers met due dates, but with extended shipping times due to fewer flights, and global shipping complications as a result of COVID-19 and shipping container shortages.
To navigate the current climate, we took action. To do this, EGI started ordering steel earlier in the design process. For us, right now, steel is less expensive, and we ordered larger steel blocks. We are also monitoring our design process and ordering components and mold bases earlier in the design process.
The supply chain crisis is not going away soon. Encourage your team to be resilient and to work with customers and suppliers to reduce risk points to meet lead times.
The following are recommendations for facing supply chain issues head on:
- Work with suppliers to understand their constraints and risks to meet deliveries.
- Request weekly or daily updates to track progress.
- Conduct risk assessments to find bottlenecks and alternative ways to continue delivering quality molds on time.
- Ensure your customers know and understand the current climate of tool building.
- Be upfront and honest when communicating issues and challenges that may impact a mold build.
- Provide detailed updates with photos.
- Involve your customer in supply issues as they might have pull with suppliers.
The supply chain crisis is not going away anytime soon. Encourage your team to be resilient and to work with customers and suppliers to reduce risk points to meet lead times. When issues occur, communicate and work closely with your customer and suppliers to minimize delays. One day this will pass, but until then, we need to press on and over-communicate.
Related Content
-
MMT Chats: Solving Schedule and Capacity Challenges With ERP
For this MMT Chat, my guests hail from Omega Tool of Menomonee Falls, Wisconsin, who share their journey with using enterprise resource planning (ERP)—and their people—to solve their schedule and capacity load monitoring challenges.
-
MMT Chats: 4 Keys to a Successful Mold-Building Operation: Innovation, Transparency, Accessibility and Relationship
MoldMaking Technology Editorial Director Christina Fuges chats with Steve Michon, co-owner of Zero Tolerance in Clinton Township, Michigan, about the excitement of solving problems, the benefits of showing gratitude, the real struggle with delegation and the importance of staying on top of technology. This episode is brought to you by ISCAR with New Ideas for Machining Intelligently.
-
The Critical Role of Management Representatives in ISO 9001
In ISO 9001 quality management systems, the Management Representative (MR) plays a crucial role. While the 2015 version of ISO 9001 no longer mandates this position, having a trusted management member serve as an MR remains vital for streamlining operations and maintaining quality standards.