Share
Read Next
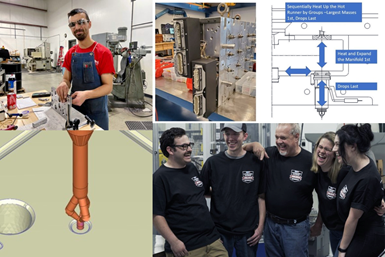
Photo Credit: (top left) Tri-Par Die and Mold Corp. (top right) Fast Heat by Spark Industries, (bottom left), RJG Inc. (bottom right), Westminster Tool.
With so much content to read on top of your daily responsibilities, it’s always nice to have some recommendations to narrow your focus, help you prioritize and ensure you don’t miss out on a piece of content that could impact how you do business moving forward.
Below is a recap of MoldMaking Technology articles (along with excerpts) dating back to 2000 that our editorial advisory board (EAB) members noted as some of their favorites. Here are the top five:
5. September 2021 issue: Leadtime Leader Award Winner: Westminster Tool — Perseverance with a Plan
Westminster Tool’s latest commitment to the plan — investment in new technologies, processes and capabilities, workforce development/training, and sales and marketing — helped them edge out this year’s competition.
“Westminster Academy maps outline a specific career pathway in the company with all the courses and lessons needed to succeed in that position. With more than 50 maps covering positions from molding technician to president, everyone within the company participates in defining the roles and responsibilities required of their position clearly and improving their maps for the next training opportunity ultimately. This captures and standardizes all tribal and technical knowledge for current and future trainees, ensuring everyone receives the same quality training.”
4. November 2021 issue: The Ins and Outs of Hot Runner Temperature Control
A training checklist that explains the why and how of proper hot runner temperature control and system management.
“Five critical areas to consider during this preparation include the (1) condition of hot runner heaters, thermocouples and grounding (ensure there are no direct shorts), (2) mold box connections and grounding, (3) heater and thermocouple cable connections and grounding (ensure there are no direct shorts), (4) hot runner controller connectors, maintenance and grounding and (5) incoming power and grounding. Notice the importance of proper grounding. If any one of these links in the chain is not production-ready, the system will not perform correctly.”
3. September 2019 issue: Injection Molding Simulation Prediction Vs. Actual
Simulations have come a long way in the last three decades. Still, if we seek to prevent dimensional variation, we must understand what provides the highest level of accuracy so we can make good injection mold engineering decisions.
“There are four analyses to run with hundreds of results for each. Don’t worry; we won’t talk about them all, just some higher level ones. The first type is a filling analysis showing shear heating, shear rates, shear stress, air traps, knit/meld lines, clamp tonnages and injection pressure. Then we have the packing analysis to provide clamp tonnage, gate seal, potential sinks and voids. Finally, cooling helps to determine the overall cycle time based on wall thickness and material section (metal and plastic), as well as cooling line placement. Warp is inherent to most, if not all, plastic molded parts. It’s just a matter of scale.”
2. December 2012 issue: Part 1 — Finding, Training and Retaining Employees
Before beginning your search, sit with your management team and list the non-machining skills, accomplishments and attributes you know someone must have to be successful at your company.
“Develop relationships with the schools in your area — both high schools and colleges. Meet with counselors and advisors to tell them you are looking to hire. Make sure they understand that you know you are not going to get someone with machining skills. Counselors and advisors interact with hundreds of people and are often the first to hear about it when someone is looking for a job.”
1. August 2000 issue: Teach Yourself Polishing
Schools for mold polishing do not exist, and most veteran polishers don’t want to teach the subject, so here are a few simple polishing guidelines.
“It’s an unfortunate reality that far too many polishers destroy the dimensions of the part all because of ignoring the following rule, “You can’t use as much steel as you wish to put on a polish. You only have the depth of the tool mark.” That simple rule is from where 99% of all ruined dimensions come. The polisher does not understand where a dimension is; the dimension that the moldmaker intended is exactly at the bottom of the tool mark and not 0.0001 further.”
Related Content
Editorial Advisory Board 2023-2026: Meet New Board Member Adam Nartker, Diversified Technologies International
The 2023-2026 version of MoldMaking Technology’s EAB features a new crew of industry professionals. Meet Adam Nartker.
Read MoreHow to Use Strategic Planning Tools, Data to Manage the Human Side of Business
Q&A with Marion Wells, MMT EAB member and founder of Human Asset Management.
Read MoreGenerational Quality: Balancing Tradition, Innovation and Continuous Improvement
Q&A with Corey Fox, an MMT EAB member and Operations Manager at Accede Mold and Tool.
Read MoreEditorial Advisory Board 2023-2026: Meet Board Member James Jergens, Ascend Innovative Mold
The 2023-2026 version of MoldMaking Technology's EAB features a new crew of industry professionals. Meet James Jergens.
Read MoreRead Next
UMass Lowell Assistant Professor Shares Three Favorite Articles Used to Educate Incoming Moldmakers
MMT’s Editorial Advisory Board shares its top MoldMaking Technology articles and how this content has been valuable to their businesses.
Read MoreHuman Asset Management Talent Development Consultant and Partner Shares Three Favorite Articles: Profiles, People, Purpose
MMT's Editorial Advisory Board shares its top MoldMaking Technology articles of all time and how this content has been valuable to their businesses.
Read MoreScholle IPN NA Tooling Manager Shares Three Favorite Articles: Community, Game-Changers and Training
MMT's Editorial Advisory Board shares its top MoldMaking Technology articles of all time and how this content has been valuable to their businesses.
Read More