Next Generation Goes Go-Pro during COVID-19 to Advance Shop Technology
The coronavirus doesn’t stop two next-generation professionals from implementing new five-axis machining cell technology at Electroform.
The use of a Go-Pro as a webcam at Electroform helped to maintain ongoing communication with the Exeron GmbH engineer who was 7 hours ahead.
Photo Credit: Electroform Company
“It was pretty amazing to see two young guys stepping up and doing a project most would not tackle. That’s something that is needed in this industry,” says Electroform Company CEO Wade Clark. Clark is referring to his son Zach who got creative and worked with Germany-based Exeron engineer Dominik Merz to remotely set up and make tooling modifications to the shop’s five-axis Exeron machining cell with integrated automation.
Electroform Company, located in Machesney Park, Illinois, has been offering product development, injection molds, automation, and injection molding for the plastics industry since 1988 to the medical, packaging and consumer products industries. The team uses its R&D facility to design and build multi-shot, in-mold labeling, and in-mold decorating and assembly, to name a few.
This line of work demands current technology, including the latest in machining and automation, and a shop can’t afford to be static with technology even during a pandemic if it wants to remain competitive. Clark explains that the new linear five-axis machining cell is not only extremely high precision but also very complex, which presented the challenge.
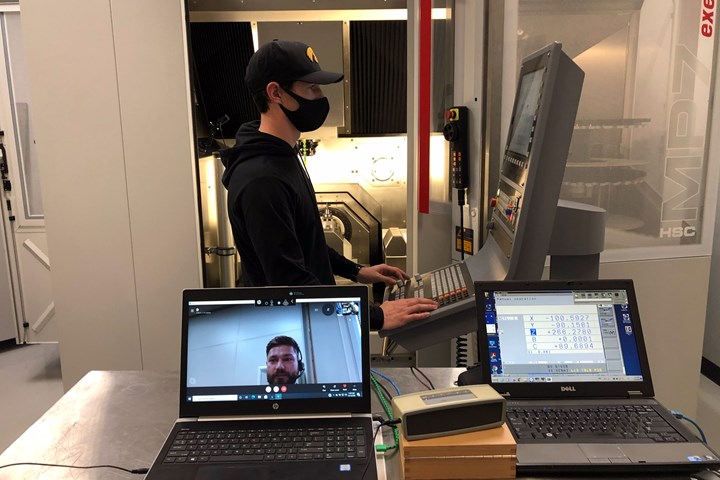
Zach Clark worked with Germany-based Exeron engineer Dominik Merz to remotely set up and make tooling modifications to the shop’s five-axis Exeron machining cell with integrated automation.
“We were not able to use a local technician. Plus, we didn’t know exactly what went into setting up a five-axis milling machine remotely because this machine is one of two Exeron five-axis machines in the whole United States, and we own both of them,” Zach Clark says.
Zach and Dominik installed the five-axis cell in two 6-hour days with a programming follow-up for air chuck that took another 90 minutes.
Zach Clark decided to use a Go-Pro as a webcam to maintain ongoing communication with Exeron GmbH, which was 7 hours ahead. Exeron GmbH is based in Oberndorf, Germany, near the edge of the Black Forest. This situation required Clark to work diligently in the mornings “virtually” alongside Merz (while it was late afternoon in Germany), which cut set-up time short.
Zach and Dominik installed the five-axis cell in two 6-hour days with a programming follow-up for air chuck that took another 90 minutes. All of this was completed over the internet. “Neither Zach, Dominik, nor Exeron, had ever installed a machine over the Internet before. Exeron provided the expertise that helped the set-up go extremely well, given the difficult circumstances under which both companies worked,” Wade Clark says.
The remote set-up was a big challenge, but Merz would do it again. “From my last visit to Electroform to set up their first machine, before the pandemic shutdown, I knew that the remote set-up would work because their employees are very good. We worked well together. Kudos to you and your team,” Merz says.
Related Content
-
Three Good Reasons to Switch from Three- to Five-Axis Machining in Moldmaking
Five-axis machining technology is a great tool in the moldmaker toolbox.
-
Mold Innovations Power Unique Auto Lighting Elements on Hummer EVs
Diamond machining, electroforming of micro-optical inserts and modified latch-lock system help injection molds produce unique forward lighting elements.
-
Machining Center Spindles: What You Need to Know
Why and how to research spindle technology before purchasing a machining center.