MoldMaking Technology is the go-to spot for everything moldmaking. From vertical machining to training and business development, as well as tips for achieving the best mold finish – we have you covered. Take a look at what articles you may have missed or want to revisit.
Below are the top ten most-viewed articles of 2022 so far. Based on analytics, these have been considered the most popular posts. However, this is just a small portion of the content MMT covers online and in monthly print issues.
Click the links below in case you missed any of these features or want a second look. For more archived content visit MMT’s articles tab.
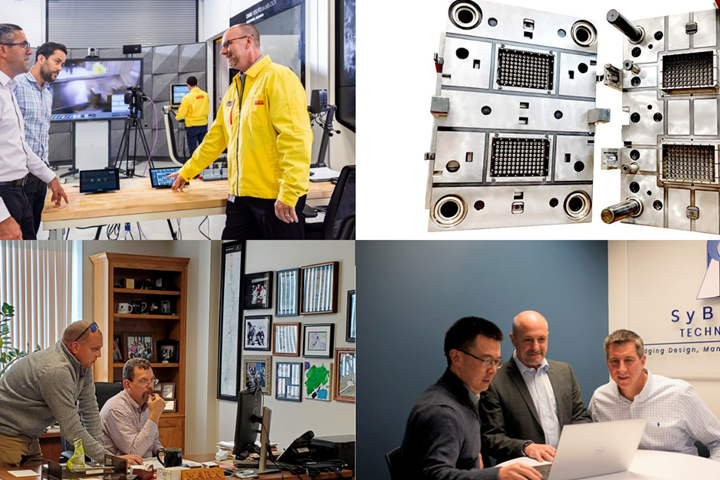
10. Vertical Machining Center Designed for Moldmaking Alongside Metal 3D Printers Brings Virus Face Masks to Market Quickly
Speed and accuracy of a new vertical machining center are vital to a two-process approach for quickly producing much-needed face mask molds.

The pandemic put many manufacturers to the test as teams jumped in to help produce various personal protective equipment, including Bastech, Inc. and its team. A new vertical machining center enabled the speed and accuracy they were looking for, and even acted as a significant contributor to the company’s newly launched product line.
9. How to Use Continuing Education to Remain Competitive in Moldmaking
Continued training helps moldmakers make tooling decisions and properly use the latest cutting tool to efficiently machine high-quality molds.
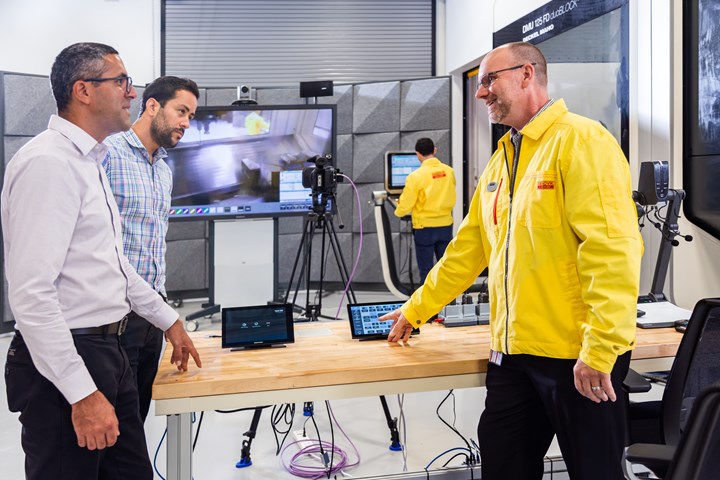
Photo Credit: Sandvik Coromant
This article details how the moldmaking industry is ever changing and with that, comes a need for all moldmakers to continue their education. The key to achieving this is standard or customized training, whether it’s in-person, virtual or a little bit of both, says Sandvik Coromant ’s Mike Andersen. This can lead to proper tooling decisions and use of the latest equipment, such as cutting tools.
8. Hot Runner, Mold Component Partnerships Lead to Innovative Mold Designs
Formula Plastics takes on tooling via sister company Formula Tooling using dedicated partners, 3D modeling services and highly trained engineers to develop advanced mold designs.
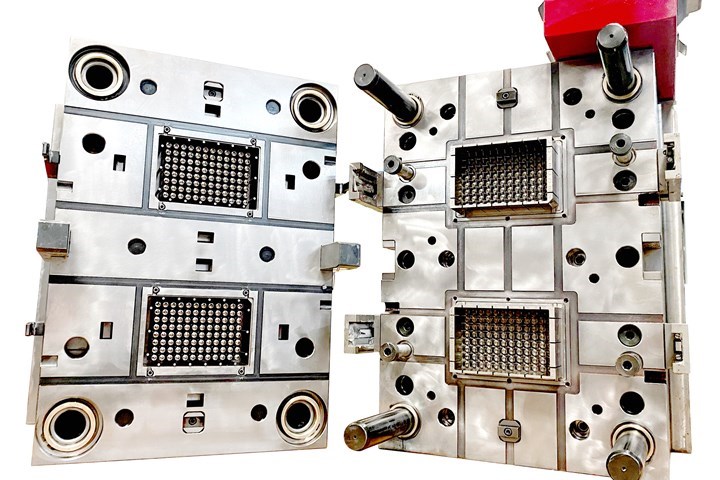
Formula Tooling (sister company to Formula Plastics) has built over 90 molds since 2020. It’s revenue grew over $10 million in 2021. This case study examines their strategy with dedicated partners, 3D modeling services and highly trained engineers.
7. Transforming Moldmaking into Digital Industrial Manufacturing
Moldmaking and digitalization is at the core of this global industrial manufacturing company’s consolidation and diversification plan.
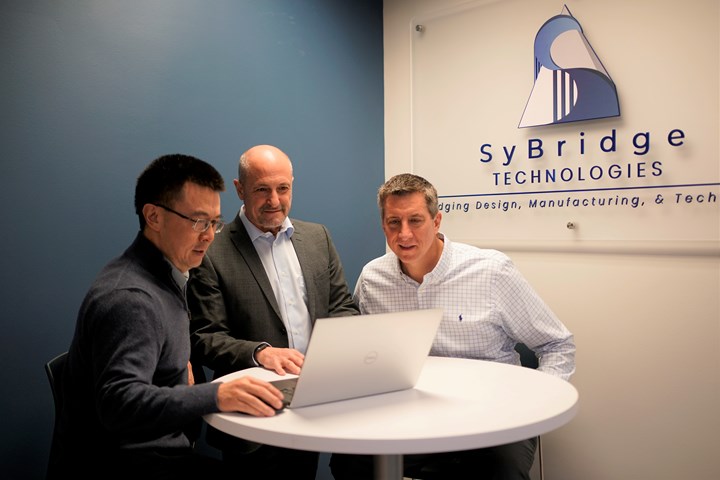
Moldmaking is at the core of global industrial manufacturing company SyBridge Technologies’ consolidation and diversification plan. SyBridge Technologies CEO, Tony Nardone explains, “We view ourselves as a true solutions provider, an industrial technology company that takes on a total package. We can take all the data and manage the platform.”
6. Lessons from a Nine-Year Succession Plan
Small business shop owners share the four keys to transitioning a family manufacturing business.
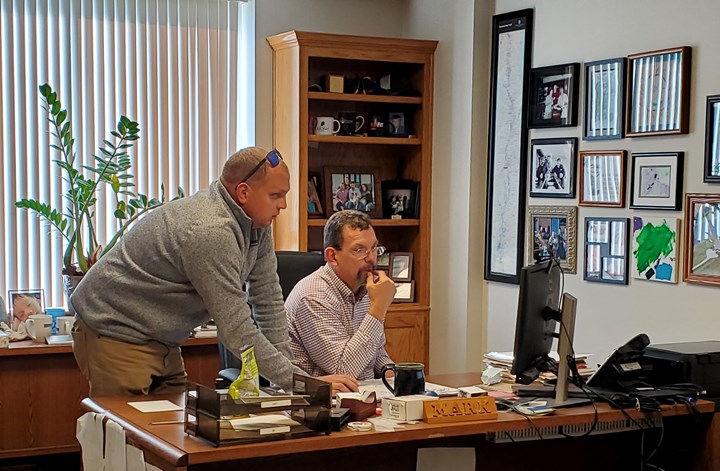
Mark and Corey Brown of Burger & Brown Engineering sit down to share their experience transitioning ownership of their family manufacturing business. Read about what they learned from their nine year succession plan. Small spoiler: it involves a sense of humor.
5. A Different Approach to Pricing
A cost-based approach to pricing used in moldmaking is the fundamental flaw causing net profits to be less than 10% of sales. There is another option.
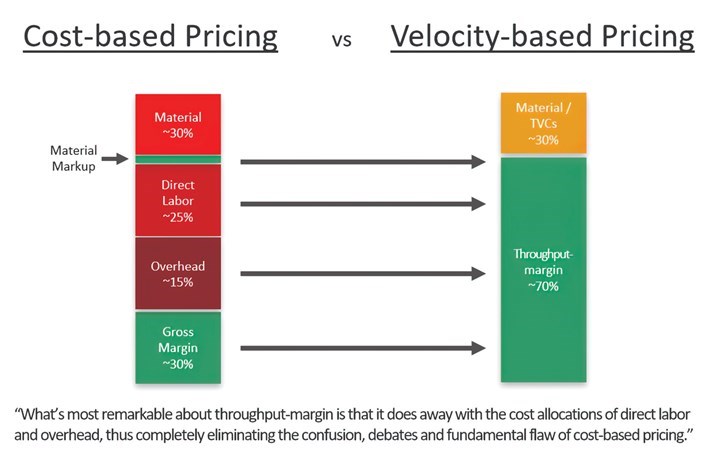
Do you lose opportunities because your price is too high? Do you ever feel you might be leaving money on the table? Are you ever less than 100% confident in your price? This article will help you navigate your options when it comes to pricing at your moldmaking business.
4. How to Use Diffusion Bonding to Optimize a Mold’s Thermal Performance
Joining dissimilar metals has tremendous potential for conformal cooling, but to successfully use diffusion bonding, a mold builder must understand the complexities of the interface and its effect on the chemical and thermo-mechanical properties of the bond.
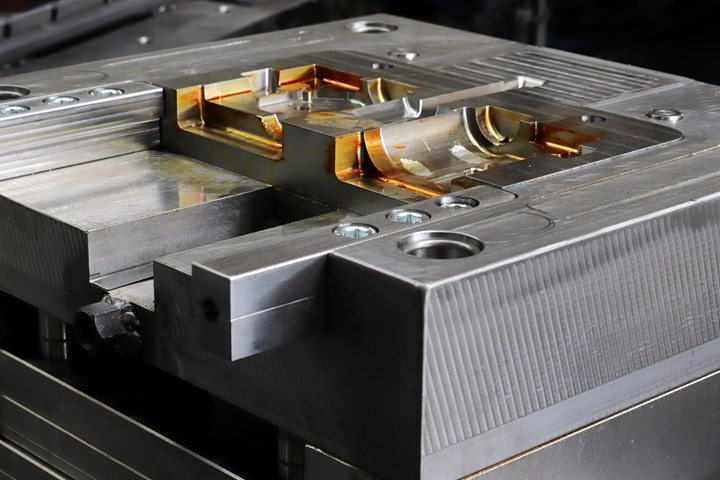
In this informative article, Thomas Palamides, Senior Product Manager at Industrial Furnaces, explains how mold builders can increase the quality of a finished product and reduce manufacturing costs through conformal cooling.
3. Save Time, Money: Use a Mold Design Checklist
Here are 15 examples of common molding issues that occur during an initial mold trial. Many of them could be avoided or corrected with a proactive checklist.
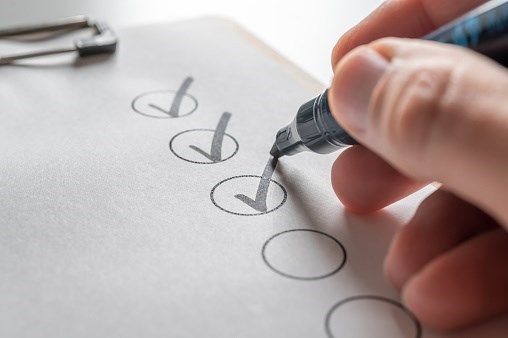
Not only does this article gives 15 examples of common molding issues, it also details the top three cost variables of a mold design. This is no average mold design checklist, it is a “Proactive Mold Design Checklist” that details the “what ifs” of mold design failure.
2. How to Achieve the Best Mold Finish
A look at factors that impact the polishability of tool steels and recommendations for obtaining a high-gloss finish.

Mold polishing is a critical step when it comes to the manufacture of high-quality plastic parts. This article from Camilla Finnkvist, Application Manager at Uddeholm and Patricia Miller, Director of Technical Services, details some key challenges and factors to consider to achieve a high-gloss surface finish.
1. Advances in P20 Steel Potentially Eliminates Need for Stress Relieving After Rough Cutting
Omega Tool Corp. compares conventional, new P20 grades side by side in production fascia tools, finds no downside.
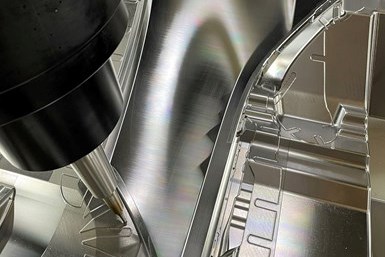
When Finkl Steel launched, MD Xtra, its new P20-type steel back in 2017, the company knew it would be a game changer. “Although modifications to P20’s basic chemistry have occurred over the years, the sizes of today’s largest molds have reached a range where you need to move beyond P20 to achieve the ideal properties needed by such big molds,” noted Ben Ritchey, Finkl technical director. But how much of a game changer was it really? In this article, Finkl, together with Omega Tool Corp. and an automotive OEM, conducted a study to test the steel’s properties again conventional P20 to find an answer.
Related Content
Five Strategies to Make Automation Affordable
Mold manufacturers can maintain their competitive edge by making smart capital investments in times of crisis.
Read MoreHow to Use Scientific Maintenance for More Accurate Mold and Part Troubleshooting
Discover how adopting scientific maintenance approaches helps improve mold lifespan, minimize failures, and optimize production outcomes.
Read MoreCAM Automation Increases Mold Production, Quality
Mold builder switches CAM software package after 20 years to take advantage of innovative programming strategies that reduce mold machining programming and processing times.
Read MoreAchieving Flexible Capacity with Automation
This high-mix, low-volume manufacturer embarked on a year and a half program to introduce robotics to its manufacturing process.
Read MoreRead Next
Four-Step Formula for Mold Builders to Use in Their Marketing That Increases Sales
The most common marketing mistakes, some key marketing questions to land new business and how the Theory of Constraints applies to marketing within the small to midsize manufacturer.
Read MoreTaking a Holistic Approach to Training Is Filling a Local Skills Gap
Success coaches through JEVS Human Services’ Tri-State Apprenticeship Program (JTAP) provide guidance and a different way of learning for the whole person for small- to mid-sized manufacturers.
Read MoreMMT Chats: Impressions and Inspirations from AMBA Event that “Shifts the View”
MoldMaking Technology Editorial Director and Managing Editor share their takeaways from a recent American Mold Builders Association Conference focused on leadership and mentorship in the moldmaking community. This episode is brought to you by ISCAR with New Ideas for Machining Intelligently.
Read More