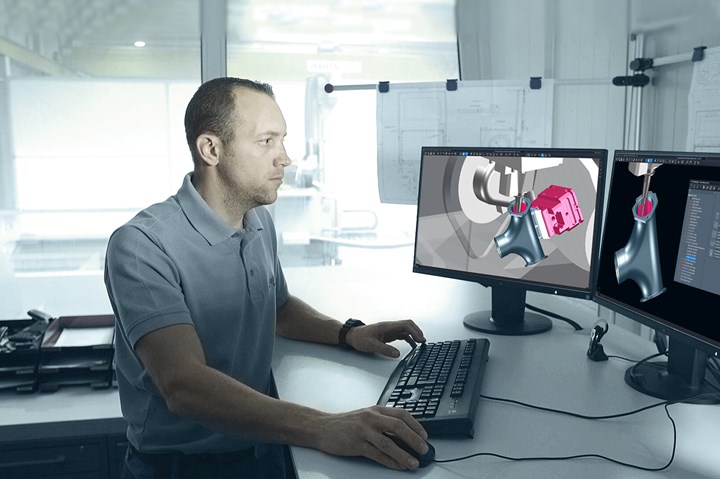
Mold builders can standardize operations by creating templates for automated design and manufacturing processes. Photos Credit, all images: Tebis America
It is no secret that being a mold builder today isn’t like it used to be. Challenges, including the growing cost of doing business, increased low-cost country competition and the seemingly never-ending talent gap, require businesses to focus on driving efficiency throughout their organization to remain competitive.
As a result, many mold shops are turning to automation to streamline manufacturing operations. But, as with many things, “automation” is a broad topic, and there are multiple forms of automation to consider. All too often, when automation is used in the manufacturing environment, people automatically think of robots, cobots or vision systems. And while these are viable solutions for some manufacturers, for moldmakers they can make significant operational improvements and reduce wasted time with process and design automation.
The automation journey is a marathon, not a sprint, requiring planning (i.e., training) and strategy. Let’s start with the foundation, your mindset. If your mindset is to see every mold as unique, you probably view automating mold design as undesirable or impossible. This isn’t true — it’s like thinking any shoe will be adequate for your marathon.
Many of your molds include identical parts, which makes it possible to automate the general design by developing a template with your CAD/CAM software. Any variations in size, color, tolerance or surface area can be modified utilizing parametric features and, with the right software, can be programmed into the design.
This level of automation is achievable regardless of your shop’s size or type of tool produced. However, it requires time and focus. Automation is not a quick fix (i.e., sprint), but it can deliver a significant return on investment when correctly implemented. This can be done by following several key steps in your automation planning.
-
Prepare Your Business
Before committing to a marathon, you must assess your overall health — whether your body can take on the task. The same is true for automating your operations. You need to assess all aspects to determine if your machinery, equipment and people are capable of automation. Things to ask yourself: Is your equipment old? Do you have current machine technology? Is your software capable of the programming level needed for automation?
Once your capabilities assessment is complete, you must make an investment plan for the required equipment and technology and work to standardize your tooling operations. These key activities serve as the foundation for automating your processes. However, having the right people on board is equally important for all of this. Marathons aren’t necessarily a team sport, but automating your business is, so it may require you to hire different talent or identify and train interested team members.
-
Research the Right Solution
Once you have identified the gaps, it’s time to identify the right solutions and partners to ensure you have the tools to simulate and automate. In doing so, conducting due diligence in your research is important to identify the technology and technology partners that will address your needs and simplify your current systems. For example, creating and simplifying processes will be difficult if your business has multiple software programs that don’t interact or work collaboratively.
Use the experience of others by leveraging your peer network and associations, such as the American Mold Builders Association (AMBA), to learn about process automation best practices and identify potential partners through referrals.
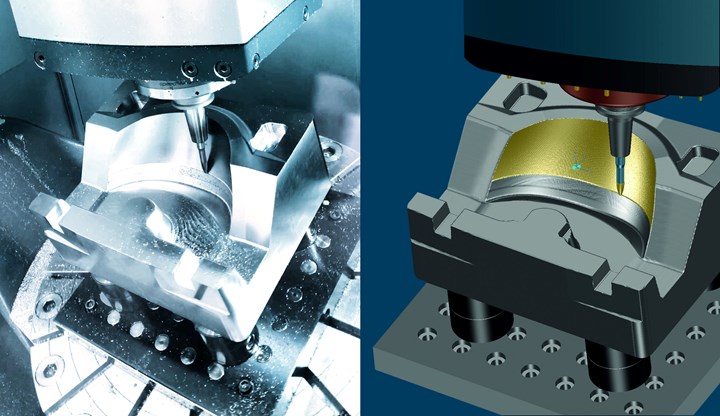
Mold builders can automate the general mold design by using CAD/CAM to develop a template.
-
Create a Digital Layout
To automate programming and design, you must create digital versions of all your entities — tools, machines and clamping devices. Every piece of equipment must have a digital twin. This will allow you to predict and estimate what the machine can do within a certain time for specific mold designs. With this information, you can make, develop and test a build process before establishing it as a benchmark.
Automation allows you to do more more efficiently, helping you cross the finish line with on-time delivery and cost-competitive tools.
-
Create Templates
The next step is to create templates for automated design and manufacturing processes — 2D, 3D, five-axis, simple parts, partial template, etc. — to help standardize operations. Think of a template as a training route. Start with a basic route based on desired distance and make changes to customize or adapt the route to your growing level of fitness.
Creating and using templates as a map for the structure or design of a mold and the manufacturing process can eliminate some guesswork, save time, and help standardize and improve quality. Additionally, it enables you to operate more machines with fewer people.
-
Simulate Before Releasing the Jobs
You have your templates, automated design and development processes and are ready to build your first mold. However, before you take that step, run a full simulation on all of your machines.
You can integrate your programming and machine simulation with the correct software solution. This will identify any potential issues or crashes and insulate your business from them, helping to ensure your shop is ready to run the automation race.
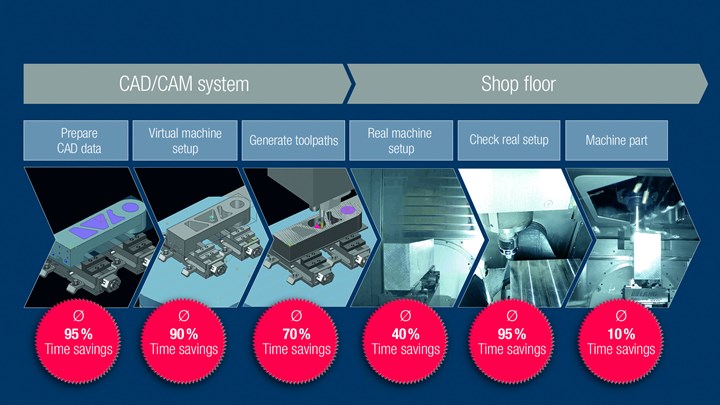
A mold shop must assess all aspects of the operation to determine if its machinery, equipment and workforce are capable of automation.
-
Analyze the Data
To optimize your business and ensure your automated processes are achieving your desired goals, you need to collect and analyze data from all aspects of the company. The key to doing this is having the right manufacturing execution system (MES) and enterprise resource planning (ERP) system feeding you the necessary information to make informed business decisions and determine how to best meet your customers’ quality and delivery needs.
The marathon of automating your manufacturing operation allows you to maximize your team, ensuring that employees deliver value and optimize machine use. It also makes your shop a desirable place to work for the next generation of manufacturers.
Remember, automation does not replace people. You will always need skilled talent to operate your moldmaking business successfully. By incorporating automation into your business, you move people from performing low-value tasks to high-value ones. Ultimately, automation allows you to achieve more with better efficiency, helping you cross the finish line with on-time delivery and cost-competitive tools.
Related Content
Quality Tool & Die Enhances Performance With Advanced EDM and Milling Technologies
The adoption of Mitsubishi wire and sinker EDMs, along with the OPS Ingersoll five-axis milling machine with automated cells, has enabled unmanned operations and improved precision. As a result, QTD has expanded its facility, grown its workforce and increased its business by 10-15% annually.
Read MoreDevelopments in High-Speed Machining Technology
There have been many exciting developments in high-speed machining relative to machining centers and controls, tooling and CAD/CAM systems.
Read MoreCAM Automation Increases Mold Production, Quality
Mold builder switches CAM software package after 20 years to take advantage of innovative programming strategies that reduce mold machining programming and processing times.
Read MoreAdvancing Moldmaking and Plastics: Trends in 3D Printing, Automation and Sustainability
NPE 2024 showcased the latest trends and technologies in innovation, efficiency and sustainability for moldmakers and molders, featuring advancements in 3D printing, automation, design and virtual reality/augmented reality/artificial intelligence.
Read MoreRead Next
Turning the Tables on Me ... Conversation All About Moldmaking
Being a guest on the All-Axis Podcast by Tebis was a pleasure to talk about all things moldmaking.
Read MoreStability, High Speed, Flexibility of Five-Axis Portal Milling Machine Reduces Rework for Mold Builder
The thermo-symmetrical construction of a five-axis portal milling machine with a center-guided Z-axis enables higher accuracy, reducing rework. Also, the symmetrical design and the guide arrangement increase stability and save weight, making the machine more dynamic, productive and energy-efficient.
Read More