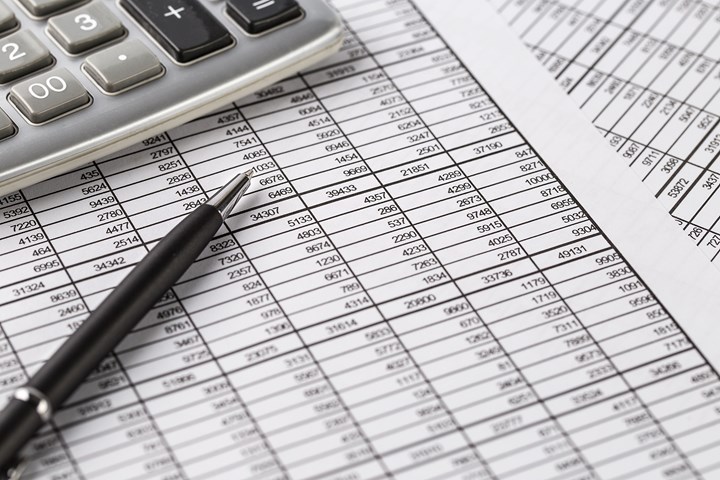
In recent months, the U.S. Treasury Department has issued two sets of rules interpreting new provisions found in the Tax Cuts and Jobs Act of 2017 (TCJA) that could have a significant impact on a moldbuilder’s tax liability.
The Treasury proposed regulations relating to accounting methods for individual small businesses having less than $25 million (indexed for inflation) of average annual gross receipts (AAGR). The Treasury typically will issue regulations in the proposed form first, allowing businesses to comment on the regulations before they issue them in a final format. While the Treasury sometimes allows businesses to rely upon proposed regulations for tax return positions, the general rule is that the regulations are not effective until they are in the final format.
The Treasury also issued final regulations on bonus depreciation, reflecting changes made by both the TCJA and the Coronavirus Aid, Relief and Economic Security Act (CARES Act). These regulations clarified several rules related to mold shops’ buildings and plants.
Simplified Accounting for Small Business
The TCJA increased the AAGR threshold that moldmakers must meet to be eligible for various simplified accounting methods. The TCJA allowed mold shops with AAGR of $25 million or less for the prior three tax years ($26 million for 2019, as the amount was indexed for inflation) to switch to the cash method of accounting. That is, the mold shop will recognize revenue when it receives the cash and claim deductions after they pay the expenses. Mold shops meeting the AAGR threshold and whose receivables exceed their payables should evaluate whether this change in accounting method would benefit them.
Shops meeting the AAGR threshold may treat their inventory as non-incidental supplies and materials, deducting the inventory when used or consumed, or following its applicable financial statements (AFS). Also, shops under the AAGR are exempt from the Uniform Capitalization (UNICAP) rules and are not required to capitalize their indirect expenditures and overhead into the cost of their inventory.
The proposed regulations addressed the definition of a tax shelter concerning these methods of accounting rules. Mold shops that incur losses and are taxed as flow-through entities (S Corporations, Partnerships and LLCs) in which ownership does not participate in the management of the business could result in the entity being deemed a tax shelter, thereby not allowing the change, even if the reason for the loss is the change in the accounting method itself. As such, any mold shops with ownership not active in the management of the business should evaluate these rules carefully.
The Treasury department received comments asking them to consider the argument that mold shops could deduct the inventory when they go into work-in-progress, rather than when they sell the finished mold to the customer.
The proposed regulations reiterate that mold shops meeting the AAGR threshold may treat their inventory as non-incidental supplies and materials, deducting the inventory when used or consumed, or following its applicable financial statements (AFS). However, Treasury defined “used or consumed” as sold to the customer in these proposed regulations.
This interpretation seems to conclude that Congress intended no real change since accrual-basis businesses could deduct the inventory when sold to the customer before the changes made by the TCJA. The Treasury department received comments asking them to consider the argument that mold shops could deduct the inventory when they go into work-in-progress, rather than when they sell the finished mold to the customer. If the Treasury were to accept this suggestion, mold shops should consider how this change in accounting method could help defer their tax liabilities.
The proposed regulations also clarify that if the mold shop does not have an AFS, then they must prepare their books and records following the accounting procedures that meet that requirement.
Final Regulations on Bonus Depreciation
The TCJA allows mold shops to write off the cost of qualifying property as a 100% bonus depreciation in the year they placed the property into service. Bonus depreciation typically applies to shops’ depreciable assets with a recovery period of 20 years or less. The deduction applies to qualifying property bought and placed into service after September 27, 2017.
While bonus depreciation has been around in some forms since 2001, the TCJA increased the bonus depreciation percentage from 50% to 100% for assets placed in service between September 27, 2017, and December 31, 2022. The percentage begins to phase-down in 2023. Also, the TCJA expanded the definition of eligible property to include used property.
While bonus depreciation has been around in some forms since 2001, the TCJA increased the bonus depreciation percentage from 50% to 100% for assets placed in service between September 27, 2017, and December 31, 2022.
The final regulations clarify the effect of the changes made to bonus depreciation by the CARES Act. The CARES Act made qualified improvement property (QIP) eligible for bonus depreciation after a drafting error in the TCJA. Generally, QIP is any improvements made to a shops’ interior of the plant and not the building’s structure.
The final regulations address preexisting QIP. That is, if a mold shop purchases a new building with existing QIP, those improvements/costs are not eligible for bonus depreciation. If a mold shop acquires a building tax-free in a like-kind-exchange, the QIP will not be eligible for bonus depreciation. If shops are building a new plant, special rules apply to which assets and components are eligible for bonus depreciation.
Both sets of regulations provide much-needed guidance to businesses. Mold shops should evaluate how these new regulations will impact their tax liabilities, and owners should keep a lookout for the final regulations concerning small shops’ methods of accounting.
Related Content
MMT Chats: Solving Schedule and Capacity Challenges With ERP
For this MMT Chat, my guests hail from Omega Tool of Menomonee Falls, Wisconsin, who share their journey with using enterprise resource planning (ERP)—and their people—to solve their schedule and capacity load monitoring challenges.
Read MoreThink Safety: Eliminate Hazards Throughout the Shop
The tooling community is taking advantage of new products for safer mold shops and molding facilities.
Read MoreEditorial Guidelines: Editorial Advisory Board
The Editorial Advisory Board of MoldMaking Technology is made up of authorities with expertise within their respective business, industry, technology and profession. Their role is to advise on timely issues, trends, advances in the field, offer editorial thought and direction, review and comment on specific articles and generally act as a sounding board and a conscience for the publication.
Read MoreMaking Mentoring Work | MMT Chat Part 2
Three of the TK Mold and Engineering team in Romeo, Michigan join me for Part 2 of this MMT Chat on mentorship by sharing how the AMBA’s Meet a Mentor Program works, lessons learned (and applied) and the way your shop can join this effort.
Read MoreRead Next
Tax Relief to Help Manage the Impact of COVID-19
U.S. Congress and Treasury have provided relief to mold shops since the beginning of the coronavirus via accelerated deductions, new tax credits, guidance around these benefits and extensions on the time to file and pay taxes.
Read MoreHow Tax Reform Impacts the Accounting Methods of Mold Shops
The Tax Cuts and Jobs Act of 2017 code may broaden the accounting methods available to mold builders with average annual gross receipts of less than $25 million for the prior three tax years.
Read MorePODCAST: Interview with Our Tax Guy, Mike Devereux
MMT Editorial Director Christina Fuges sat down with The Manufacturing Alliance Podcast for a lively conversation with Mike Devereux of Mueller Prost who brings tax knowledge and expertise to the brand’s monthly The Bottom Line column.
Read More