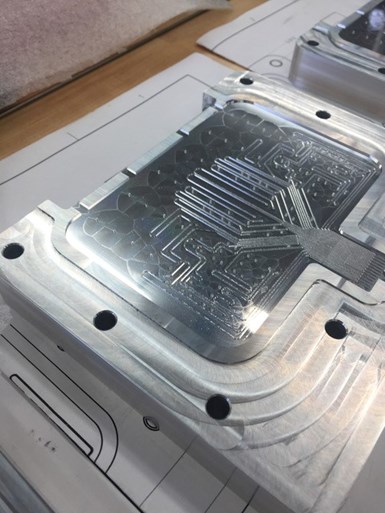
Part sizes at M5 were getting smaller and smaller, so the shop invested in a Kern Micro Vario machine tool equipped with a Heidenhain TNC 640 control for five-axis micro machining. Photo Credit, all images: M5
M5 (Minnesota Micro Molding, Machining & Manufacturing), based outside of Minneapolis, is a four-person machine shop with about 20 machines doing specialized micro machining. Production is generally under 500 as this shop prototypes tiny parts, assemblies and fixtures for customers with incredibly high accuracies. M5 has grown from a tool and die shop to a strong and reliable source for small parts (almost always less than the size of a hand) and micro machining and molding.
“The part sizes requested kept getting smaller over time, so we further pushed our resources in that direction and obtained a Kern Micro Vario machine tool equipped with a Heidenhain TNC 640 control for five-axis micro machining,” M5 owner, Jon Baklund, explains. “Not only did this add an innumerable amount of new capabilities and capacity, but it also brought in new customers. In fact, with it, we have been able to push the limits further on accuracies that we would have never even contemplated attaining before, achieving the highest and tightest tolerances and surface finishes that we’ve ever had. And when I talk about capabilities, I am referencing that these machines are full dynamic five-axis machining centers, with high-speed spindles up to 42,000 rpm!”
Putting Five-Axis Control to Work
One recent example is a medical device manufacturer who needed an extremely detailed microfluidics mold to help make essential vaccines and other drug therapies. This silicone mold part needed about 30 0.010-inch-wide channels. M5 staff had to machine the entire bottom of the mold with a single 0.008-inch-diameter end mill to be held to a near-perfect flat surface that would not have any steps or individual facets in it.
The process took 22 hours to get that first exacting surface using five-axis machining. Once completed, it could be used to make plates that allow varying liquid medication/materials to go into the channels and then blend to make varying drug therapies/vaccines.
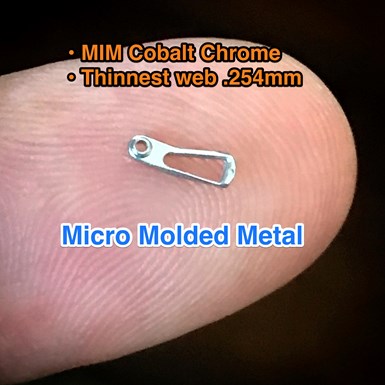
Working in the micron range, accuracy is of the utmost importance to M5. This part micro molded at M5 was possible with the help of its Kern with the Heidenhain control.
For this project, M5 made eight of these microfluidic molds at the high accuracies required by the customer. “Having a machine like the Kern Micro Vario with the Heidenhain control gave us great control over spindle growth, especially when 50 millionths matters,” Baklund adds.
The acquisition of the five-axis machine tool has enabled M5 to handle many much-needed medical equipment parts jobs quickly, and word has spread. Many jobs are done around the clock using the Heidenhain TNC 640 controls’ remote desktop manager in order to work at night from home, so four months after starting up the machine tool, a second Kern/Heidenhain was added to the shop. Its small footprint allowed easy implementation.
“These machines are full dynamic five-axis machining centers, with high-speed spindles up to 42,000 rpm!”
Another recent example of medical equipment parts completed quickly by M5 is a job involving critical components for a one-trigger, Inneurco device used in brain surgery on stroke victims. This small device is developed to quickly penetrate a brain blockage, cut and suture in one pass. Again, M5 expediently handled the micro machining/molding/welding of multiple vital parts. “By doing this, we were happy to enable our customer to get their product to market faster,” Baklund says.
M5 also was responsible for micro molding tiny prototype components on its patented Desktop Micro Molding Platform for a Medtronics part for pacemakers where tiny wires will be run through before implantation in a human heart. “Here, 0.004-inch-size wires will run through eight 0.005-inch-diamenter holes and the parts cannot be touched by human hands to keep it sterile, so the importance of this mechanical automation and the need for these super high-accuracy machines,” Baklund says.
“When you combine the accuracy of a machine like the Kern Micro Vario with the control capabilities of the Heidenhain TNC 640, the number of new possibilities that open up to a company like ours is virtually endless.”
Refined Micro Mold Machining Technology
Baklund also points out that not just any machine tool can do this type of delicate work. That’s because thermal expansion can cause machining issues when dealing at microlevels. However, the Kern machines are easily controllable and liquid-cooled throughout to eliminate that.
“For years, we worked at getting our micro process refined. This is why we ended up adding the Heidenhain-controlled Kerns. They get the job done and don’t need to be in a temperature-controlled room.,” Baklund says. The Kern machine is configured to pump cold water throughout the structure, making it more temperature stable than its outside environment.
With no prior experience with five-axis machining or a Heidenhain control, Alex Madsen, M5 part owner, lead toolmaker and designer, was up and running in a week and a half from receiving the first Micro Vario, doing very complex operations and already completing jobs to go out the door.
“I’m regularly using end mills of 0.003-inch diameter on hardened steels with these machines, often resulting in surface finishes like mirrors. Also, the fifth axis helps with tool life. Being able to machine five sides of a part simultaneously eliminates having to fixture second clamping,” Madsen says.

M5 refined its micro process by adding Heidenhain-controlled Kern machines.
Toni Mangold, Kern precision president, adds that it is important to them to have a control that can handle the latest advanced technology built into the Micro Varios. “We standardize with Heidenhain controls because of their high level of built-in technology that enables our machines to reach their full capability and for the user to do great manufacturing quickly and easily. These unique technologies are built into this machine, and the user doesn't need a Ph.D. to run it. You use the cycles on the control, and it works!”
“I’ve also found that the Heidenhain TNC simulation test run screen is extremely accurate,” Madsen adds. “I do a full render of my part on the control, and there have been times where it shows a half a thousandth step off that was found in the G-code and the Heidenhain control shows it. So, I can prove it out on the control on these tiny parts where I need super-fine surface finishes, and I trust what I see. And it turns out as expected.”
One of Madsen's favorite TNC optional control features is dynamic collision monitoring. Baklund explains that they leave it turned on at M5. “It is worth it because if you crash a spindle, the cost could be $60,000.”
Madsen explains that this is important to him since he sometimes does five or six different parts a day between two machines running simultaneously, so he needs to trust that he can walk away from one setup to view another. “This allows me to be more efficient and productive. I rely on the collision monitoring every day.”
M5 has much to look forward to in the days, months and even years ahead. “When you combine the accuracy of a machine like the Kern Micro Vario with the control capabilities of the Heidenhain TNC 640, the number of new possibilities that open up to a company like ours is virtually endless,” Baklund concludes.
Related Content
How to Analyze and Optimize Cutting Conditions to Reduce Cycle Time
Plastic injection mold design and manufacturing company puts NC program optimization software module to the test. The results were surprising.
Read MoreDevelopments in High-Speed Machining Technology
There have been many exciting developments in high-speed machining relative to machining centers and controls, tooling and CAD/CAM systems.
Read MoreFive-Axis Graphite Mill With Automation Debottlenecks Electrode Machining
Five-axis electrode cutting enabled Preferred Tool to EDM complex internal screw geometry on an insert that otherwise would have had to be outsourced.
Read MoreMachining Center Spindles: What You Need to Know
Why and how to research spindle technology before purchasing a machining center.
Read MoreRead Next
VIDEO: 6 Factors a Mold Builder Should Consider in a CNC Control
Many mold builders choose high-speed cutting over EDM because CNCs are able to meet the required tolerances and finishes. The control is key to this. Here we break down what a mold builder should look for in a CNC control.
Read MoreSix CNC Control Features for Moldmakers
A CNC control should have features to automatically smooth the axis movements or allow the operator to set tolerance limits manually.
Read MoreProductivity Meets Precision
With machine dynamics, mechanical design and thermal stability in control, mold manufacturers can take five-axis machining to the next level.
Read More