Are You Blazing New Trails to Build Your Future Workforce?
I’ve been working in the manufacturing industry for many years now, and I know that manufacturers have struggled far too long to bridge the skills gap. Thank goodness for moldmaker ingenuity and the desire to rise above the roadblocks!
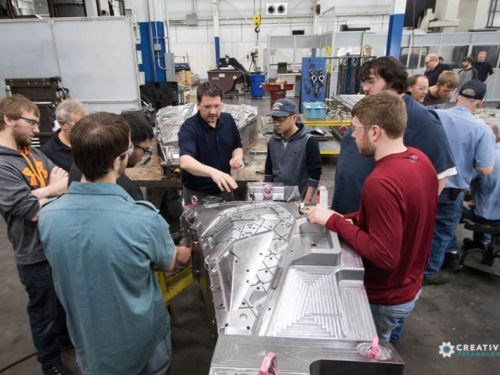
Our 2016 Leadtime Leader Honorable Mention, MSI Mold Builders, regularly hosts student tours in its Cedar Rapids, Iowa, moldmaking facility in order to promote careers in our trade.
I’ve been working in the manufacturing industry for many years now, and I know that manufacturers have struggled far too long to bridge the skills gap. There always seemed to be roadblocks strewn here and there along that career path manufacturers have laid out before legislators, teachers, career counselors and prospective apprentices. What roadblocks? There are so many I can’t count them all, but those roadblocks caused enough derailment for us to see too many shop classes and related curriculums get eliminated from school offerings. Thank goodness for moldmaker ingenuity and the desire to rise above the roadblocks!
Since I became actively involved with the American Mold Builders Association (AMBA) Chicago Chapter about 16 years ago – and especially since I’ve had the honor to join the editorial staff here at MMT – I have met many moldmaking business owners and managers who are blazing new trails to bring this viable industry back into view. I thought I’d mention a few of them in my blog today and share the wealth of ideas.
CS Tool Engineering Inc. in Cedar Springs, Michigan, is one mold shop that is working hard to make connections both inside and outside of the industry in order to promote our trade. “We consider ourselves an educator to anyone who wants to learn more about the trade,” Don Snow, president, told MMT. “We have welcomed college classes, community members, and other tool & die shops to tour our facility. We do not feel threatened by a competitor if they have a question or would like to see how one of our machines works. We’re all in this together and we support the community and trade strongly. We recently helped sponsor Career Tech Days at the Muskegon Area Community Tech Center along with our tool & die collaborative. By staying involved in these trade schools, we are supporting young people who may not know about the exciting opportunities in tool & die.”
Metro Mold and Design in Rogers, Minnesota, has seen a lot of change happening in both its workforce and the global workforce. “The companies that are successful will be those that can quickly educate or re-educate their workforces both domestically and abroad,” Greg Heinemann, CEO, says. “We have explored the idea of forming partnerships with those in education to help develop curriculums made up of both classroom and critical hands-on training that can quickly transition unskilled labor into highly-skilled labor.”
JMMS Inc., of Easley, South Carolina always has an opening for the right person, according to Rich Martin, business development manager, but at the same time, the talent has to fit the company’s culture. “Our CEO serves on a local technical college board and is an advisor on the national AMBA board,” Martin says. “He is also involved in one of the upstate manufacturing alliance groups. Our training program is state certified.”
In an article I wrote about El Dorado Molds in Rancho Cordova, California, Glen Shrigley, vice president of operations, told me, “It’s very difficult to find someone who has the right skill sets and hire them. That’s why we established our own apprentice program.” A section of the article is dedicated to how this growing company is qualifying and training its future workforce. Access the article here.
There are several more shops I could mention, but I think those above present a great variety of ideas for making the skills gap a little less arduous. So consider partnering with local high schools and community colleges that have STEM curriculums, or, like Metro Mold and Design, explore working with a school to create the training courses you need to build tomorrow’s workforce. Ally your company with at least one manufacturing-related organization like the AMBA and research state and federal grant programs that can be of benefit financially and otherwise. If you are doing something unique or just very successfully to bring new talent into your company, let us know!
Laslty, check out MMT's August issue for Part 1 of a series that breaks down the skills gap. Click here.
Related Content
Making Quick and Easy Kaizen Work for Your Shop
Within each person is unlimited creative potential to improve shop operations.
Read MoreCross Training, In-House Capabilities and Collaborative Design Move Helm Tool Forward
Cross-training, bringing it all in-house, molding and collaborative design are essential to Helm Tool's success.
Read MoreThe Role of Social Media in Manufacturing
Charles Daniels CFO of Wepco Plastics shares insights on the role of social media in manufacturing, how to improve the “business” side of a small mold shop and continually developing culture.
Read MoreMaking Mentoring Work | MMT Chat Part 2
Three of the TK Mold and Engineering team in Romeo, Michigan join me for Part 2 of this MMT Chat on mentorship by sharing how the AMBA’s Meet a Mentor Program works, lessons learned (and applied) and the way your shop can join this effort.
Read MoreRead Next
2016 Leadtime Leader Awards HM: MSI Mold Builders - Optimizing Lead Times
This mold manufacturer combines continuous improvement strategies with machining power to maximize growth and opportunity.
Read MoreHow to Use Strategic Planning Tools, Data to Manage the Human Side of Business
Q&A with Marion Wells, MMT EAB member and founder of Human Asset Management.
Read MoreHow to Use Continuing Education to Remain Competitive in Moldmaking
Continued training helps moldmakers make tooling decisions and properly use the latest cutting tool to efficiently machine high-quality molds.
Read More