AIM-ing High to Serve Medical Market
During my recent travels, of which there’s been quite a bit, I had the opportunity to visit AIM Plastics in Clinton Township, Michigan, where a whole lot of medical molding is going on.
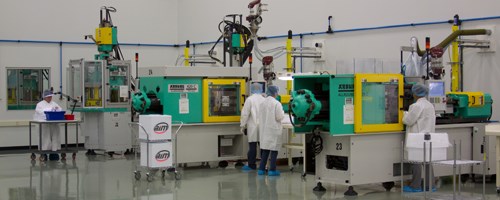
During my recent travels, of which there’s been quite a bit, I had the opportunity to visit AIM Plastics in Clinton Township, Michigan, where a whole lot of medical molding is going on.
About 99 percent of AIM’s operations is medical, so when I say a whole lot of that is happening there, you can take it to the bank. The balance is a mix of consumer and electronics products. The company, which employs 70, also designs and manufactures molds (including about 360 prototype molds per year), fixtures and gauges, by the way, so they cover the full scope for customers.
Did you catch that mention of 360 prototype molds per year? AIM Plastics offers what it has trademarked as “Prototype-Plus” molds, which means they can build an economically-priced prototype solution fast, and customers get the quality of a production mold. In other words, customers receive what can easily be used as a bridge tool or, if the mold is needed only for low-volume production, these Prototype-Plus molds might be the only tools needed to get the job done.
Walking through the company’s molding facility, it’s obvious AIM looks to meet customers’ strict quality requirements, and in fact AIM Plastics was founded on the ideology that everything produced there ultimately affects the end-users (not just OEM customers, but medical providers and their patients), so the end-users are always at the forefront of services rendered.
Within the molding facility is a 6,000-square-foot, ISO Class 7 (10K) cleanroom where parts are molded, inspected, validated and assembled according to customer requirements. Within the cleanroom environment, AIM Plastics offers a range of molding and assembly services. Scientific molding principles and processes are applied throughout to ensure molded products are consistently meeting high-level standards. Press sizes range between 40 tons and 165 tons in the cleanroom (35 tons to 440 tons overall).
I don’t want to give everything away, as I hope to do a more in-depth story about AIM Plastics in the future, but if you’d like a more detailed glimpse into this company you can visit their new website. AIM Plastics has launched an informative new blog series for the company that provides even deeper insights into the company’s expertise, and keeps visitors up to date on news and trade show appearances. In addition, as you peruse the website look for videos that will further educate you about AIM Plastics.
Related Content
-
How to Analyze and Optimize Cutting Conditions to Reduce Cycle Time
Plastic injection mold design and manufacturing company puts NC program optimization software module to the test. The results were surprising.
-
What is Scientific Maintenance? Part 2
Part two of this three-part series explains specific data that toolrooms must collect, analyze and use to truly advance to a scientific maintenance culture where you can measure real data and drive decisions.
-
Tolerancing in Mold Design, Part 1: Understanding the Issues of Conventional Bilateral Tolerancing
Mold designers must understand the location, orientation and form limitations of conventional tolerancing before changing to another dimensioning system.