Solid Carbide Drill Ideal for Cutting Medium Hardness Die Steel
Sandvik Coromant launches next-generation CoroDrill 860 for ISO P material, targets high-volume production applications for moldmakers.
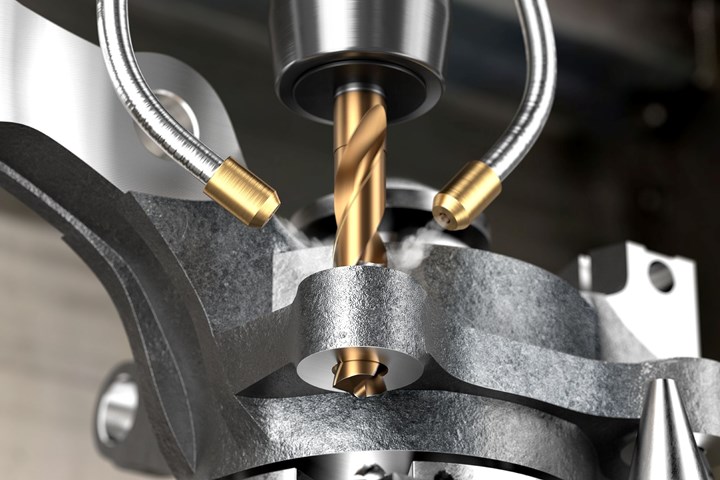
Photo Credit: Sandvik Coromant
Global metal cutting company, Sandvik Coromant, has launched an upgraded CoroDrill 860 cutting tool assortment to offer moldmaking customers improved productivity in drilling ISO P steels while significantly improving tool life.
The advanced -PM geometry is particularly ideal for medium hardness die steel in the mid-45 RC range (250-450 BHN). Sandvik notes that moldmakers would benefit using the 860-PM for higher volume production applications without the need to change out the tool as often, thereby reducing cost per component being drilled.
The solid carbide drill features a new grade, with an improved multi-layer physical vapor deposition (PVD) coating. The results are enhanced wear resistance, better tool life and an overall increase in productivity. In addition to the mold and die industry, CoroDrill 860-PM is also applicable for automotive, general engineering and power generation.
CoroDrill 860 with -PM geometry is available in standard stocked diameters from 3 mm (0.12 inch) to 16 mm (0.63 inch). Tailor-made tools are also available to customize the drill to match specific users’ machining requirements. The CoroDrill 860-PM is suitable for the Sandvik Coromant Reconditioning program. And, following end of life, the tool can enter the Sandvik Coromant Recycling program.
with an improved PVD coating will enable customers to improve process security, productivity, quality and cost.”
Related Content
-
Solving Mold Alignment Problems with the Right Alignment Lock
Correct alignment lock selection can reduce maintenance costs and molding downtime, as well as increase part quality over the mold’s entire life.
-
Maintaining a Wire EDM Machine
To achieve the ultimate capability and level of productivity from your wire EDM on a consistent, repeatable and reliable basis, regular maintenance is a required task.
-
Moldmakers Deserve a Total Production Solution
Stability, spindle speed and software are essential consideration for your moldmaking machine tool.