National Tool & Manufacturing Surface Grinder Improves Parallelism, Finish
Amerimold exhibitor National Tool & Manufacturing enhances its surface grinding tolerance capabilities to provide a 0.0002 parallelism.
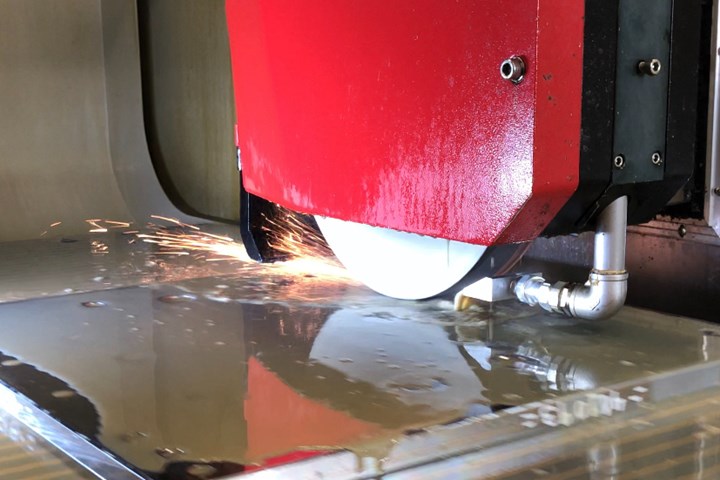
Photo Credit: National Tool & Manufacturing Co.
To improve its custom steel mold base and plate quality for its customer’s tooling projects, Amerimold 2021 exhibitor National Tool & Manufacturing Co. (NTM) says it has improved its surface grinding tolerance capabilities. According to NTM, its surface grinder was enhanced to provide a 0.0002 parallelism thanks to uniform machine quality, which is due to consistent preventive maintenance done according to factory specifications and recommendations. The surface grinder wheel will cross the plate and take off a specific amount, customized for each project. It is programed to automatically dress after a certain amount of stock removal. This ensures that the wheel is not being overdressed or loaded up.
The machine also automatically compensates for diameter loss from wheel dressing—the wheel’s speed will increase to ensure consistent surface finishes. The machine keeps track of the lost diameter and how fast it should be going to ensure it provides the most accurate grind with each pass. The surface grinder also contains a mist-away system to keep swarf from spreading to the rest of the shop, while an automatic paper filter also works to ensure coolant cleanliness. These added protections help keep particulates off the plate to help perfect the RMS finish, the company says.
NTM also focuses on perfect flatness. The variable chuck is used to assist the operator in achieving the required parallelism and flatness, resulting in consistent, correct tolerance and flatness. The ability to program plates to grind unattended also enables technicians to complete other projects while the surface grinder is in operation.
Exhibitor: National Tool & Manufacturing Co.
Booth 136 (P)
Related Content
-
Tolerancing in Mold Design, Overcoming Cutting Tool Vibration, SPE MTD Updates & More Most-Viewed May Content
Every month, MMT draws inspiration from its diverse readership's wide-ranging interests, from mold design tolerancing to cutting tools and beyond. Here are May’s top 10 most-viewed articles, based on Google Analytics.
-
How to Optimize Mold Finishing
Circle segment technology requires fewer tool paths, improving surface quality and increasing cutting tool life.
-
Cutting Tools: Technology to Make Your Process Easier
Having the right cutting tool technology for moldmaking is a crucial component for efficiency and cost-effectiveness.