Magnetic Ring Encoder Delivers Functional Safety for Machine Tool
Heidenhain’s contamination-resistant, absolute modular magnetic angle ECM 2400 is suitable for high rotational speeds, angular accelerations and limited space.
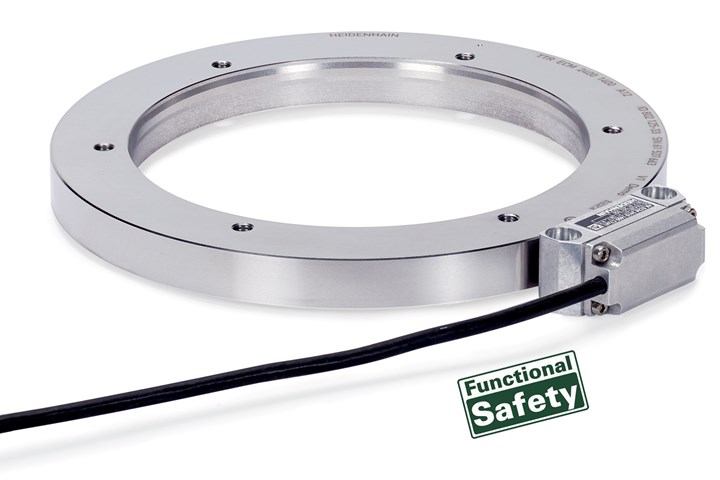
Photo Credit: Heidenhain Corp.
Heidenhain’s contamination-resistant, absolute modular magnetic angle encoder, the ECM 2400, provides machine tool users functional safety (FS) for machine feedback. ECM 2400 supplements the Heidenhain’s portfolio of absolute angle encoders and is designed for machine tool applications that require a sturdy encoder with medium accuracy. The ECM 2400 is suitable for applications with high rotational speeds, angular accelerations and limited space due to the system’s low overall height.
Heidenhain says the ECM 2400 encoder works particularly well on B-axis lathes with motorized milling spindles, or on the A and C axes of milling machines where a large hollow shaft encoder is necessary. In general, it is suitable on all rotary axes that require the following attributes:
- Safety-oriented application (mechanical fault exclusion
- Sturdy angle encoder
- Large inside diameter
- Lower position accuracy than an optical measurement system
- Dynamic positioning accuracy (simultaneous multi-axis machining)
The encoders are available with EnDat 2.2 interface. In conjunction with a safe control, they can be used as single-encoder systems in applications with control category SIL 2 (as per EN 61508) and with Performance Level “d” (as per EN ISO 13849). The fault exclusion that is implemented in its design has been tested and is ensured under the specified operating conditions.
Existing non-FS interfaces for ECM 2400 encoders includes Fanuc05 and Mit03-4. All of these encoders have an IP67 rating.
Related Content
-
Moldmakers Deserve a Total Production Solution
Stability, spindle speed and software are essential consideration for your moldmaking machine tool.
-
How to Eliminate Chatter
Here are techniques commonly used to combat chatter and guidelines to establish a foundation for optimizing the moldmaking process.
-
The Secrets to Hard Milling Success
The Secrets to Hard Milling Success