Husky Introduces UltraShot Hot Runner Injection Molding System
Amerimold exhibitor features the advanced technology which permits more precise melt control and the ability to produce identical, repeatable performance in every cavity.
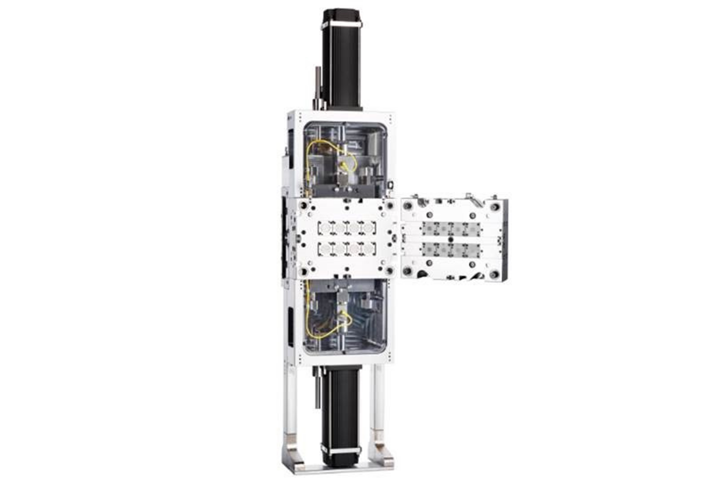
Photo Credit: Husky Injection Molding Systems
UltraShot by Husky is said to offer dramatic advances over traditional injection technology. The UltraShot hot runner injection molding system features a servo-controlled injection system that permits more precise melt control right in the gate, by positioning the shooting pots in closer proximity to the gates and pressurizing the resin near the cavities. This reduces shear and thermal variations in part quality and performance.
Additionally, says the company, UltraShot’s flow-front arrival time is shortened, enabling optimized command of cavity filling and short-shot balance control, and giving the ability to produce identical, repeatable performance in every cavity. UltraShot is also instantly scalable to 128 cavities under identical processing conditions, regardless of mold size by injection molding process constraints.
More importantly, says Husky, while the melt in a conventional hot runner can go through many high-pressure injection cycles, the melt in UltraShot hot runners experiences far fewer. This means less molded-in stress caused by birefringence, plus less scrap and waste, resulting in improved optical qualities in the finished part, while also helping to preserve the properties of a user’s resin material.
Moreover, a finished molded part can be produced in just one manufacturing step and in one production cell, instead of several. This is especially valuable to medical molders, Husky claims, because it reduces the number of step-by-step processes and product validations required, helping to get products to market faster, with a significantly reduced manufacturing footprint.
The UltraShot hot runner system also gets its precision from companion Altanium mold controllers, which accurately monitor set temperatures and cell manufacturing operations, ensuring dimensional consistency and a more ideal balance.

Exhibitor: Husky Injection Molding Systems
Booth 342
Related Content
-
Where Mold Manufacturing and Plastics Processing Connect
The Moldmaking Pavilion is one of seven pavilions returning to the show that houses exhibitors offering technology and service solutions for your specific moldmaking needs.
-
MoldMaking Technology's Leadtime Leader Awards Competition Returns!
After a brief hiatus, MoldMaking Technology’s Leadtime Leader Awards Competition is back!
-
More Than Moldmaking at PTXPO 2023
The Moldmaking Pavilion returns to the Plastics Technology Expo (PTXPO) March 28-30, 2023, at the Donald E. Stephens Convention Center in Rosemont, Illinois, but there’s more to discover than moldmaking.