Former i-mold Changes Names to Servomold GmbH
With the change to Servomold GmbH & Co. KG, Managing Directors Bianca and Thomas Meister underline their company’s focus on the development and manufacture of servo-electric systems.
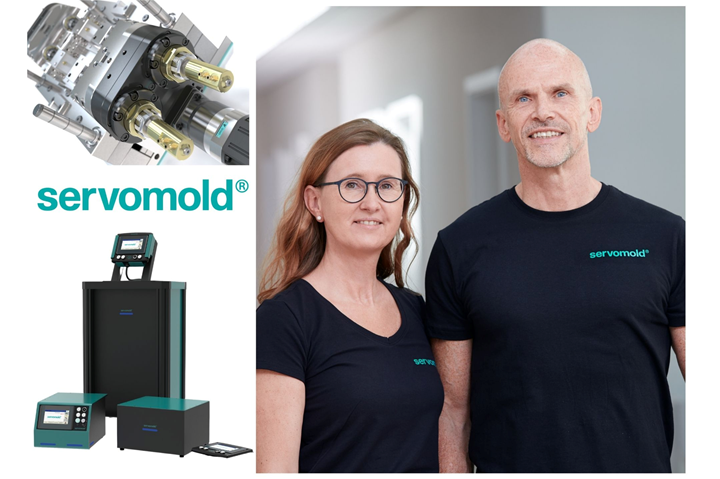
Photo Credit: Servomold
Former i-mold GmbH & Co. KG has changed its name to Servomold GmbH & Co. KG, a decision, says Managing Directors Bianca and Thomas Meister that helps emphasize the company’s focus on application-specific components and integrated system solutions for the automation of injection mold tools. As part of its production line, Servomold has sold more than 600 plug-and-play controllers worldwide.
The company began in 1998 as a design service provider—and one year later—for the development and patenting of tunnel gate inserts. In 2011, Thomas Meister founded the Servomold division, whose name the company has now taken over.
“As a consultant, designer and supplier, we combine over 20 years of corporate experience in all aspects of injection mold tools automation,” Thomas Meister says. “Our technologies offer countless possibilities to realize rotational and linear movements with the highest process and mold safety, while at the same time enabling significant energy savings compared to hydraulic and pneumatic systems.” The business with tunnel gate inserts has been continued by previous Co-Managing Director Andy Walter in a separate company.
Servomold manufactures its individually designed systems up to the complete unscrewing half in-house, and supplements special designs with modular components such as thread core systems, indexing plate drives, unscrewing units, drive units and linear actuators. In the application-specific realization of corresponding complete solutions, the company includes—beyond the tool—the entire process chain. Commissioning worldwide on site as well as remote services complete the offer.
“Servo components create ideal conditions for the realization of minimum cycle times and maximum availability, as well as comprehensive process control and verifiability,” Thomas Meister continues. “Especially when using all-electric injection molding machines, they are the ideal complement for achieving clean operating conditions. We look forward to perfecting and further developing our proven performance under the Servomold company name. For example, we will soon be able to present a completely newly developed control system, further strengthening the basis for successful cooperation with our customers.”