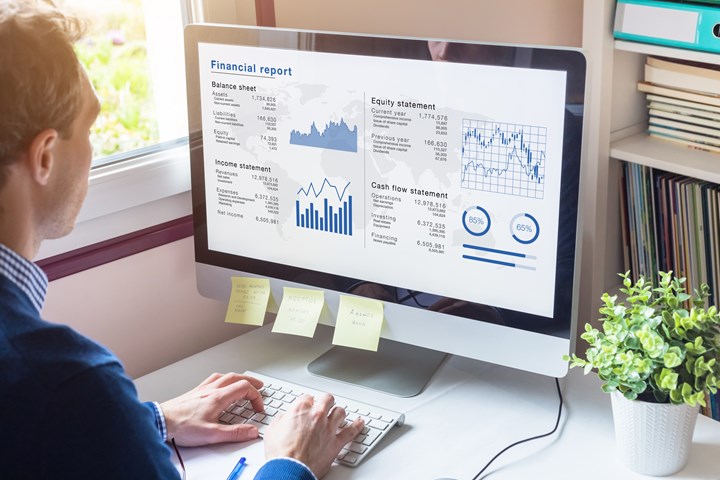
Photo Credit: Getty Images
As the final quarter of 2021 begins, mold builders should focus on year-end tax and cash flow planning. With so much uncertainty in today’s environment—labor concerns, geopolitical changes and the potential for tax law changes—mold shops will benefit by understanding their current financial and operational wellbeing.
Cash Flow and Tax Planning
Cash flow planning is imperative to give your shop the wherewithal to accomplish some of your goals. There are many moving parts in a mold builder’s operation, so using a cash-flow projection tool to consider the variables or “levers you can pull” to impact cash flow as the year comes to an end can be extremely helpful.
Tax planning cannot be done in a vacuum. We often run two years of tax projections to ensure the shop and planner understand the impact of specific actions. For example, should you accelerate or defer income from 2021 to 2022, or vice versa.
Also, shops must think beyond only U.S. income tax. For example, many tool builders are structured as flow-through tax entities (such as S corporations or partnerships), which means they are taxed at the shareholder or partner level. In addition, the U.S has four sets of rules passing through an individual income tax return: income tax, alternative minimum tax (AMT), self-employment tax and net investment income tax. So again, having someone involved who understands how each work can be highly beneficial.
Impact of Tax Policy
What are the prospects of tax rates going up? Many in Washington believe the Democrats will successfully reverse some of the Trump-era tax cuts brought about by the Tax Cuts and Jobs Act of 2017. However, some provisions could significantly impact mold shops and their owners. Proposals include increasing corporate and individual income tax rates, removing the flow-through deduction for manufacturers and increasing the estate tax. This change could have a significant impact on the transfer of family-owned mold shops.
As such, if shops believe that tax rates will increase the following year, they may want to consider accelerating income into 2021 to take advantage of the lower tax rates and deductions that may not be available in 2022 and beyond. While this seems at odds with traditional tax planning, many advisors are considering the possibility and taking these proposals into account while planning for their clients.
While tax deductions are a great way to increase cash flow, tax credits provide the best bang for your buck because they are a dollar-for-dollar offset to a mold builder's income tax liabilities.
Three Planning Strategies
Here are a few planning ideas for mold builders regardless of whether tax policy changes.
1. Method of Accounting Changes: Switching from Overall Accrual Method to the Cash Method, or Vice Versa
Under the accrual method of accounting, most mold builders must recognize revenue when it is earned and expenditures when they are fixed and determinable. The industry widely used this method up until the Tax Cuts and Jobs Act (TCJA) made changes that enabled “small” businesses (businesses less than $26 million average annual gross receipts) to switch their overall method of accounting to the cash method without requesting permission from the Internal Revenue Service.
The cash method recognizes revenue when the cash is physically received and expenditures when the cash is paid, allowing for better control of the timing of revenue and expense recognition. This accrual to a cash method of accounting change can be very advantageous for mold builders with large receivable balances, prepaid expenses and smaller payable balances, accrued expenses and job deposits. However, understand that this change results in a timing difference and not permanent tax savings.
If an overall switch to the cash method is not logical, there is a lighter option under §1.263(a)-4(f). This rule is commonly referred to as the "12-month rule" and allows businesses to expense any prepayment that the underlying benefit does not exceed the earlier of 12 months or the end of the taxable year following the taxable year in which the payment was made.
For example, accrual-basis moldmakers can receive a full deduction for the prepayment of expenses, even if the event has occurred in full, as long as the benefit of the contract or policy does not extend past 12 months or the end of the following taxable year. Eligible expenses include, but are not limited to, workers compensation insurance, general liability insurance, real estate taxes and professional dues and subscriptions.
Alternatively, under President Biden’s proposed fiscal year 2022 budget, the potential for increased ordinary income tax rates and corporate rates may warrant a potential switch to the accrual method of accounting for some mold builders, accelerating income into 2021 that would otherwise not be recognized (collected) until 2022. In addition, shops currently on the cash method of accounting may want to accelerate income into the 2021 tax year to avoid future higher individual income tax brackets or the proposed increase of the corporate tax rate from 21% to 28%.
Section 179D studies provide generous tax savings for mold builders installing qualifying energy-efficient systems or building improvements.
2. Plant Cost Segregation and Energy-Efficient Building Improvements
For mold builders that want to own their building, add additional shop space or construct an entirely new plant, a cost segregation study can be an extremely effective tool in accelerating deductions to provide a bump in cash flow from the resulting income tax savings. Cost segregation studies offer an in-depth, engineering-based analysis of the costs associated with the acquisition, construction or renovation of a building by taking the entire cost of the development and breaking it down into smaller subcategories of building components (e.g., electrical, communications, concrete, masonry, etc.). These building components have a specified class life of 5-39 years as determined by the IRS, which dictates the depreciation method necessary.
The Tax Cuts and Jobs Act greatly incentivized the benefit of a cost segregation study when it made 100% bonus depreciation eligible to building components with a class life of 20 years or less, resulting in an immediate deduction for a large portion of the underlying project.
It is important to note that even if you purchased, constructed or expanded the building in a prior year, a cost segregation study and a simple change in accounting method can allow you to claim the depreciation deductions of prior years without having to amend prior-year tax returns.
Mold builders must think beyond only U.S. income tax.
Section 179D studies provide generous tax savings for mold builders installing qualifying energy-efficient systems or building improvements. Qualifying energy-efficient systems and improvements include interior lighting, building envelope (exterior walls and roof), or heating, cooling, ventilation or hot water systems that reduce the energy and power cost. The tax benefit for these improvements can be up to $1.80 per building square foot.
3. Income, Payroll and Other Tax Credits
While tax deductions are a great way to increase cash flow, tax credits provide the best bang for your buck because they are a dollar-for-dollar offset to a mold builder’s income tax liabilities. While numerous tax credits are available to businesses, the most important credits to the moldmaking industry are the Employee Retention Credit (ERC), Work Opportunity Tax Credit (WOTC), R&D Tax Credit and the Alternative Fuel Excise Tax Credit.
As the dust settles on the second round of the Paycheck Protection Program (PPP), exploring the ERC is important to ensure no dollars are left on the table after the PPP forgiveness process. Our August article highlighted the ERC’s general terms and significant changes, but it is essential to know how the ERC can be impacted by any potential PPP forgiveness.
Under the original guidance, ERC and PPP could not be utilized in tandem. Later developments amended those limitations and allowed shops to take advantage of both programs. However, it was clearly stated that the same wages could not be used for both programs (no double-dipping). Due to this caveat, when applying for PPP forgiveness, mold builders should exhaust all qualifying “non-payroll costs” on their forgiveness form before factoring in any wages. For example, suppose the PPP wages used on the forgiveness application reach at least 60% of the total loan process. In that case, this strategy frees up more wages for ERC purposes without jeopardizing your shop’s forgiveness eligibility.
The Work Opportunity Tax Credit is a federal credit of up to $9,600 per employee that promotes employers hiring individuals who qualify as members of a specified target group. These target groups include qualified veterans, ex-felons, residents of a federal empowerment zone or enterprise community, summer youth employees and individuals who are recipients or family members of a recipient of government assistance, including food stamps.
The R&D tax credit rewards mold builders for the design and development of new tools and related processes. For mold builders developing unique, novel, one-of-a-kind molds, the design, development and sampling activities may be eligible for the credit. In addition to the federal credit, approximately 35 states have a research tax credit.
Another less well-known tax credit relevant to mold builders is the Alternative Fuel Excise Tax Credit, which is available for alternative fuel used to operate a motor vehicle, including forklifts. A $0.50 tax credit per gallon is available for the following alternative fuels: natural gas, liquefied hydrogen, propane and others.
Now is the time to begin year-end planning. Waiting until the last two weeks of the year gives mold shops little flexibility to impact cash flow and income tax liabilities.
Related Content
MMT Chats: 4 Keys to a Successful Mold-Building Operation: Innovation, Transparency, Accessibility and Relationship
MoldMaking Technology Editorial Director Christina Fuges chats with Steve Michon, co-owner of Zero Tolerance in Clinton Township, Michigan, about the excitement of solving problems, the benefits of showing gratitude, the real struggle with delegation and the importance of staying on top of technology. This episode is brought to you by ISCAR with New Ideas for Machining Intelligently.
Read MoreThe Critical Role of Management Representatives in ISO 9001
In ISO 9001 quality management systems, the Management Representative (MR) plays a crucial role. While the 2015 version of ISO 9001 no longer mandates this position, having a trusted management member serve as an MR remains vital for streamlining operations and maintaining quality standards.
Read MoreMMT Chats: Solving Schedule and Capacity Challenges With ERP
For this MMT Chat, my guests hail from Omega Tool of Menomonee Falls, Wisconsin, who share their journey with using enterprise resource planning (ERP)—and their people—to solve their schedule and capacity load monitoring challenges.
Read MoreThe Role of Social Media in Manufacturing
Charles Daniels CFO of Wepco Plastics shares insights on the role of social media in manufacturing, how to improve the “business” side of a small mold shop and continually developing culture.
Read MoreRead Next
Understanding the Implications of Tax Filing Extensions and COVID-19
These tax tips will help mold builders take advantage of filing extensions and increased benefits from tax law updates.
Read MoreHow to Use Strategic Planning Tools, Data to Manage the Human Side of Business
Q&A with Marion Wells, MMT EAB member and founder of Human Asset Management.
Read MoreHow to Use Continuing Education to Remain Competitive in Moldmaking
Continued training helps moldmakers make tooling decisions and properly use the latest cutting tool to efficiently machine high-quality molds.
Read More