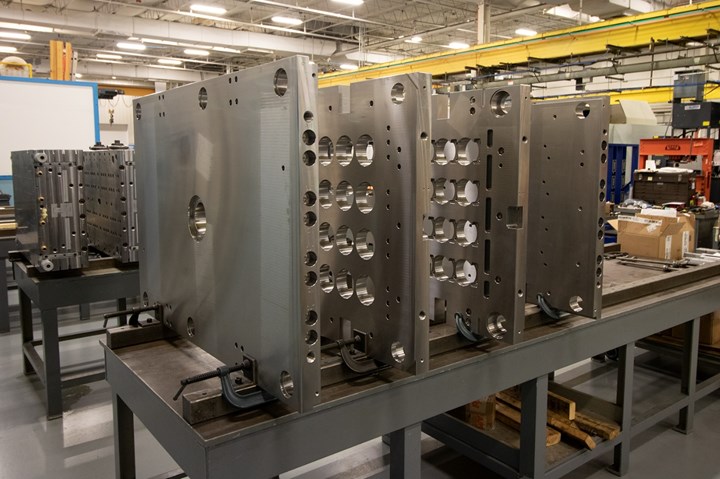
Both Triangle Tool and Penn Erie specialize in designing, building, and manufacturing large-frame custom mold for high cavitation. Photo Credit: The Plastek Group
Give us a quick snapshot of the size of the company’s tooling divisions: Triangle Tool and Penn Erie.
Tom Hartline, Penn Erie General Manager: These shops have been around more than 60 years. The Erie, Pennsylvania Tooling Divisions of The Plastek Group comprise a total of 76,278 square feet of combined workspace.
The Triangle Tool Division is 44,488 square feet, and the Penn Erie Division is 31,790 square feet, with a total of 97 employees, including three current apprentices between the two tool shops. The goal is to keep two to four apprentices on staff at all times.
What types of molds do Triangle Tool and Penn Erie design and manufacture?
Hartline: Both Triangle Tool and Penn Erie specialize in designing, building and manufacturing large-frame custom mold for high cavitation. The largest frame built by Penn Erie was 52 inches wide by 61 inches long. Mold designs include stack tooling, single-face molds, unscrewing molds and two-shot molds.
We pioneered—what are now industry standards—designing and building molds for in-press maintenance and the concept of component interchangeability.
What markets do Triangle and Penn Erie serve?
Hartline: Both operations are the middlemen to serving the injection plastics molding industry, offering mold design, building of injection and injection blow molds, as well as services and tools to satisfy the overall production needs of consumer product packaging customers.
What are some of the critical equipment across these two tooling divisions?
Bob Prischak, Triangle Tool General Manager : At Triangle, our five-axis hard mills, electrode milling machines, rough mills, lathes, grinders, EDMs and CMMs are essential. We have invested in a multitude of machine tool technology to fit our needs, including Yasada, Makino, DMG Mori, Okuma, Hurco, Brown & Sharp, Charmilles, Mitsubishi and Okamoto.
At Penn Erie, our arsenal includes Bridgeports, Cincinnati, Sunnen Hone, Okuma, Webb, (Grinding) Brown & Sharpe, Hermes Blohm, Okamoto, Okuma, Makino, Mazak, Bostomatic, Hurco, Mori Seiki, Mikron, Agie Charmilles, Comparitor CMM and an Alflak laser welder.
Our newest piece of equipment is an Okuma five-axis lathe for EDM carbon featuring automation and a surplus of capacity to hold and change out a large number of electrodes. We also employ 12 robots across both facilities—nine at Triangle and three at Penn Erie.
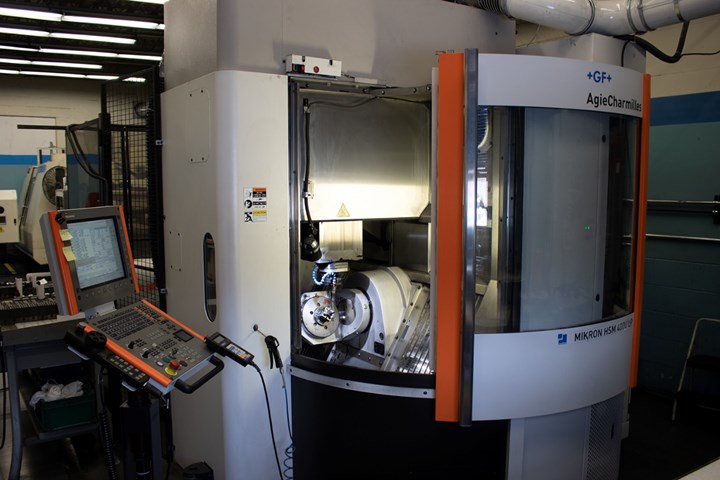
Five-axis hard mills, electrode milling machines, rough mills, lathes, grinders, EDMs and CMMs are essential to Triangle Tool and Penn Erie.
How do Triangle Tool and Penn Erie work with and benefit from The Plastek Group?
Prischak: Triangle Tool and Penn Erie are part of The Plastek Group, which has seven molding and assembly production facilities. This working relationship creates a close network and an integrated community around the completion of the manufacturing process from start to finish. Due to the business structure within The Plastek Group, Triangle Tool and Penn Erie are set up with a surplus of accessible communication and convenient on-site maneuverability to follow the design, build and production phases of each project, as required. Triangle and Penn Erie also have the advantage of The Plastek Group’s in-house first article team who performs eight different testing procedures.
Both tooling facilities work to achieve the quickest cycle times and good quality parts, which begin with engineering. Working with our in-house corporate tooling/design and engineering departments, Triangle Tool and Penn Erie attend weekly design and tooling review meetings as well as a variety of testing, prototyping and documentation meeting. Participation in these meetings is essential as we move through the part design and mold manufacturing process to ensure the utmost ease of in-press maintenance. We also hold in-depth interviews and follow-up meetings with customers.
Both tooling facilities work to achieve the quickest cycle times and good quality parts, which begin with engineering.
How do you achieve in-press maintenance designs and component interchangeability?
Prischak: We pioneered—what are now industry standards—designing and building molds for in-press maintenance and the concept of component interchangeability. We incorporate more plates into the mold design. We design in more moveable pieces instead of requiring a technician to pull an entire mold out of the press. This design provides the technician with access to all components while the mold remains in the press. It also allows for layers to be removed, giving access to more parts and components—as little or as much as needed.
What does automation look like across The Plastek Group’s tooling divisions?
Prischak: A recent focus has been adapting more automation. For example, at Triangle and Penn Erie, automation is present on several of our five-axis machining centers. The robots are strategically installed by interfacing them directly to the machines. While we do staff three shifts a day within each of the tool shops, the technology we have allows us to automate the process as much as possible to reduce the labor and manufacture around the clock. In some instances, we also run our shops lights out.
How are you addressing the skills gap for both tooling divisions?
Hartline: It is not easy to find qualified and interested candidates for employment. So over the past 50 years, The Plastek Group has provided a four-year, 8,000-hour State of Pennsylvania certified program to educate and train local talent within the plastics tool building skill set, and award individuals with a Pennsylvania Journeyman Card. Plastek’s first program graduating students was in 1982.
Plastek also participates in Manufacturing Day, high school student tours, high school and college career fairs to help educate young, developing minds about the career opportunities available in their communities.
To offset the challenge of finding external candidates for apprenticeships, we often consider individuals who are family or friends of friends of our current moldmakers. We have also had success with recommendations from individuals who are working in other departments of our manufacturing production facilities and who have shown good workmanship and potential for the apprenticeship programs.
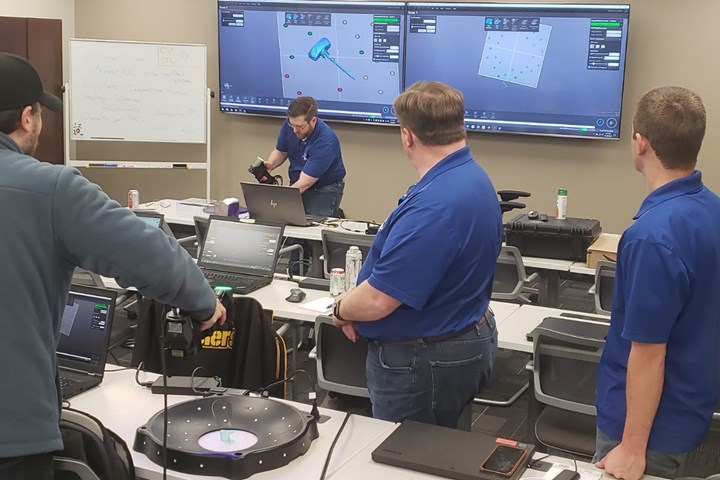
Triangle Tool and Penn Erie have both increased investment and support to the personal development of their employees over the past two years with continuous training—both on-site and company-sponsored certified training classes offsite.
Can you provide specifics on your training program?
Hartline: We have increased investment and support to the personal development of our employees over the past two years with continuous training. When it comes specifically to tooling and engineering, we have provided on-site and off-site company-sponsored certified training classes in Creo Manufacturing Training, Pro E (engineering), Pro man (manufacturing), Creaform 3D laser measuring, Abaqus finite element analysis, computer-aided engineering, statistical methods for quality and manufacturing, project management training and train the trainer.
Each program is tailored to a specific technical area and includes both on-the-job training and classroom education. We partner with Penn State Behrend, Erie Technical Institute and Richmond Community College to provide this program.
We offer a robust three-year technical training program for entry-level candidates possessing mechanical aptitude despite limited or no industry experience. Each program is tailored to a specific technical area and includes both on-the-job training and classroom education. We partner with Penn State Behrend, Erie Technical Institute and Richmond Community College to provide this program.
To participate, candidates must qualify with a high school degree, a passing grade on an aptitude test, full attendance of required classes and a satisfactory work record over a three-year commitment. These opportunities include positions as a maintenance technician, molding technician, mold maintenance and laboratory technician.
We also offer plastic process technician apprenticeships through Keystone Community Education Council scholarships, which aid students in the Erie, Pennsylvania and Hamlet, North Carolina areas, including Plastek employees and their children.
Original Plastek Group founders, Joe and Isabel Prischak, have set up more than $2,000,000 in endowment funds to support the development of the Plastics Engineering Technology Degree Penn State Behrend since 1989 and the Joseph Prischak Center for Engineering Technology on campus at Richmond Community College since 2010.
Related Content
Making Mentoring Work | MMT Chat Part 2
Three of the TK Mold and Engineering team in Romeo, Michigan join me for Part 2 of this MMT Chat on mentorship by sharing how the AMBA’s Meet a Mentor Program works, lessons learned (and applied) and the way your shop can join this effort.
Read MoreMold Maintenance Continues to Matter: Enhanced Training Program in a New Facility
I attended a MoldTrax mold maintenance workshop in 2019 and shared my experiences, and despite changes in ownership, the workshop's remarkable value endures, as discussed in a recent Q&A with the current leadership.
Read MoreCross Training, In-House Capabilities and Collaborative Design Move Helm Tool Forward
Cross-training, bringing it all in-house, molding and collaborative design are essential to Helm Tool's success.
Read MoreEden Tool and Eden Manufacturing: A Story of Resilience, Growth and Innovation
This critical parts manufacturer, founded on solid tooling fundamentals, didn’t get derailed with the unexpected passing of the owner because leadership was already building a solid business, not just a good tool shop. Here’s how they managed change incrementally… and they’re not finished yet.
Read MoreRead Next
PODCAST: 20 Years of MoldMaking Technology Magazine
It's one thing to be the interviewer; it's another to be the interviewee. The tables have been turned. The Manufacturing Alliance invited me to sit down during the American Mold Builders Association Conference to talk all things moldmaking.
Read MoreHow MoldMaking Technology Magazine Came to Be
Twenty years ago a moldmaker launched this magazine, legitimizing an industry and then passed it on to a passionate media company, which took it to the next level.
Read MoreMoldMaking Technology Celebrates 20-Year Anniversary
MoldMaking Technology (MMT) is celebrating its 20th anniversary in 2018. Founded in 1998, MMT remains committed to everything moldmaking, from design to first shot. This industry, which is utterly dependent on accurate, repeatable and efficient technologies throughout the design and build stages, was so worthy of a publication of its own. We are honored to celebrate this milestone with the industry and look forward to many more years to come.
Read More