The Designer's Edge: Plastic Part Sticking, Part 3
Today I continue my three-part series on plastic part sticking with a look at various options for holding the part to the core when the part is sticking in the cavity. I will also share a couple past examples.
Today I will discuss options for holding the part to the core when the part is sticking in the cavity. As I mentioned in Part 2, the most common approach is adding undercuts to the core with a rounded burr and pencil grinder. Just monitor the depth to prevent flaking. Another option is adding more rows of undercuts instead of going deeper with the first undercut. This entails part design approval to ensure the part's fit or function is not affected.
I advise using a dove-tailed burr and then grind down the ends, so it can act as a positive stop, allowing it to cut only as deep as modified (see image). This reduces the risk of flaking with the angled lead-in compared to the undercut from the rounded burr. This also works with cold slug wells.
Another option, although less aggressive than hand grinding undercuts, is using a $40.00 Dremel engraver with a sharp pointed tip. You can quickly add a fine stipple to the cavity surface, which helps hold the part in place.
For example, on an ABS part years ago we had an issue with the part sticking in the cavity half. We added rows of undercuts on areas on the core half. This did help the process window, but sticking was still an occasional issue with technicians trying to process around it. We used an engraver and put a fine stipple on the undercuts and cavity walls. The part then stuck so bad to the core that the ejection pins pushed right through the part. Remember this was a rigid ABS part.
Media blasting the core half with aluminum oxide is another less aggressive approach and can have a big impact on parts sticking to the cavity half. For severe sticking issues, adding a texture (acid etched) to the core half may work well.
Next month, we'll take a look at surface finishes and ways to stop parts from sticking to components such as slides and lifters.
Randy will be speaking at Amerimold Expo on June 17, 2015 on "Overcoming Repair and Part Quality Challenges with Design. " Click here to register to attend.
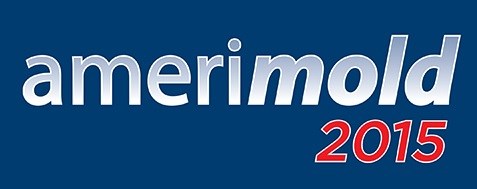