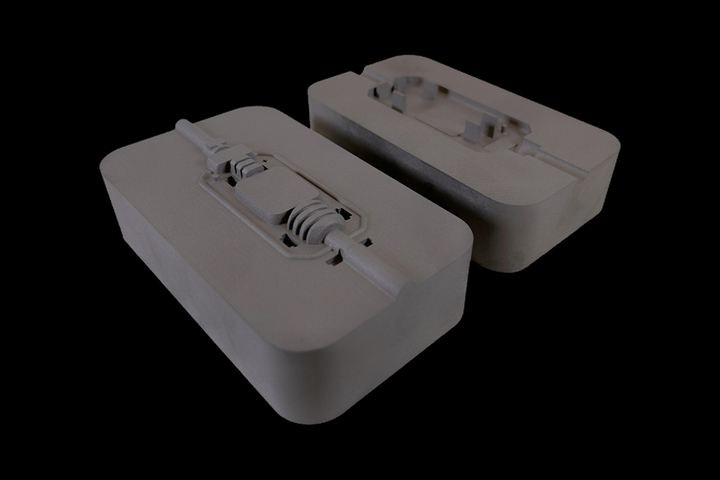
To quickly deliver production representative parts for a medical OEM to complete biocompatibility and functional testing, Westminster Tool used Mantle's Trueshape metal 3D printing technology to produce a prototype tool that provided the team with insights they could apply to the production tool build, saving time. Source (All Images) | Westminster Tool
Since July 2022, Class 101 injection mold manufacturer Westminster Tool has pushed the limits of its Mantle Beta metal additive manufacturing (AM) machine, worked with Mantle to improve the machine's quality and efficiency and completed numerous trials to identify ways to add value using this technology.
The company’s latest success story used metal 3D printing to quickly deliver production representative parts for a medical OEM to complete biocompatibility and functional testing. This included molding more than 7,000 pieces for development trials. They were then able to implement the lessons learned from the prototype mold build into a production mold, resulting in over 30% in design cost savings.
“Most of all, this tool design had over 40 swipe-by shut-off conditions, something we were concerned a printed technology wouldn’t be able to handle,” says Hillary Thomas, vice president of Westminster Tool. “Traditionally, this type of project would have required at least 8 weeks for manufacturing, requiring over 30 electrode shapes alone for EDM.”
The project was broken down into two phases of implementation.

Phase 1: Production-Quality Prototype Parts Within 4 weeks
The first step was manufacturing a prototype mold using MUD frame inserts and H13-equivalent printed cavities to replicate a production environment as quickly as possible. To do this, Westminster Tool used Mantle’s Trueshape Technology to print a top and bottom cavity. While the cavities were printed and sintered over 8 days, the Westminster Tool team finalized a post-print machining strategy, ordered MUD inserts and began the insert modifications.
The cavities required 55 hours of post-machining, which included the following:
- Grinding the bottom of the blocks to have a flat base to start from
- Squaring the block to bring molding geometry to center using hard mill
- EDM wiring ejector pin holes
- Tapping water lines and bolt holes
- Hard milling and using EDM on difficult swipe by areas (six areas total)
These operations took an additional 1.5 weeks before Westminster Tool was ready for final assembly and molding: resulting in molded parts within 4 weeks. The parts had minimal flash, and all critical dimensions were within ±0.003".
The parts were then molded in batches for development and biocompatibility testing in two different materials. The first was an ABS resin and the second was a PC/ABS blend. Ultimately, more than 7,000 pieces were produced for the customer’s development needs.
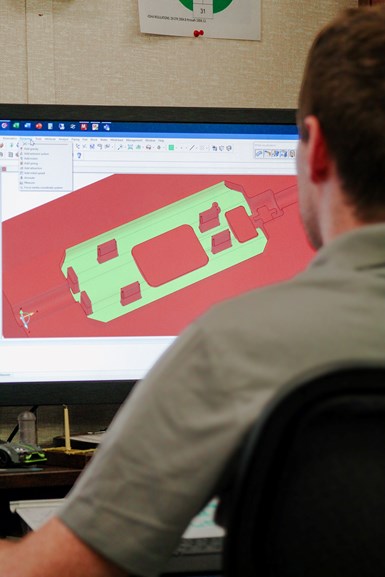
The Westminster Tool team implements lessons learned from the prototype mold build into a production mold, resulting in over 25% in design cost savings.
Phase 2: Reviewing Lessons Learned
The first of several lessons learned involved warp and sink challenges. The Westminster Tool team was able to improve some of these by adjusting process parameters, but not all. Despite achieving success in development testing, these remaining defects needed to be addressed in a production mold. While the company waited for feedback from the customer, they began identifying root causes and mitigation strategies such as surface finish, ejection and gating strategies for the production mold.
This led to a better understanding of how the material performed in the tool during molding. For example, the length of the part was shrinking more than anticipated, thus moving a dimension out of tolerance. Based on the successful fitment of the prototype part into the assembly, Westminster Tool and the customer were able to move forward with the length at its current state confidently.
“Traditionally, we would have suggested staying steel safe in this area to hit the tolerance, which would have added cost and time,” Thomas says. “But in this case, we were able to shift our expectations and still meet the requirements.”
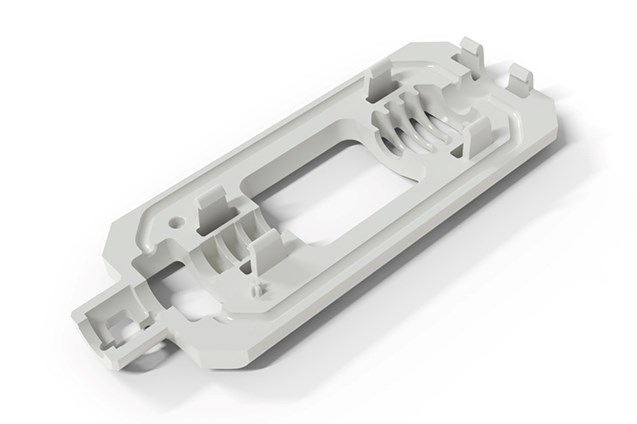
The team tackled warp and sink challenges in both the prototype and production mold stages by identifying root causes and mitigation strategies. This yielded a better understanding of how the material performed in the mold during molding, saving time and money.
Real Savings for Production Molds
“At Westminster Tool, we complete a thorough design for manufacturing process for every production mold we build,” Thomas says. This is heavily focused on risk identification and mitigation, and it accounts for about 20-30% of design costs. “By learning and understanding the prototype tool and the risk related to the part, we have a chance to remove most of these costs from our production tool build.” With this project, Westminster Tool already had the majority of the cavity stacks designed, saving an additional 10% of design time.
Most of the time, projects get hung up on the qualification phase of tools. “During the process of building tools, our pride comes from working towards real savings on the back end of the project,” Thomas shares. Whether it’s learning the hard way, for example, that a material is shrinking differently than expected or dealing with a mechanical challenge, troubleshooting can unnecessarily add weeks to a timeline.
Westminster Tool’s ultimate goal is to get involved sooner in part development so the team can seamlessly transition a complex mold from qualification to production.
Related Content
Precision Meets Innovation at IMTS 2024
After attending IMTS, it's clear that the integration of advanced technologies is ready to enhance precision, efficiency and automation in mold manufacturing processes. It’s a massive event, so here’s a glimpse of what the MMT team experienced firsthand.
Read MoreHow to Make Data Work for Mold Productivity and Performance
The use of digital workflows improves the impact of mold design libraries, conformal cooling and machine learning.
Read MoreMMT Chats: 4 Keys to a Successful Mold-Building Operation: Innovation, Transparency, Accessibility and Relationship
MoldMaking Technology Editorial Director Christina Fuges chats with Steve Michon, co-owner of Zero Tolerance in Clinton Township, Michigan, about the excitement of solving problems, the benefits of showing gratitude, the real struggle with delegation and the importance of staying on top of technology. This episode is brought to you by ISCAR with New Ideas for Machining Intelligently.
Read MoreIn "Hybrid" FIM Process, 3D Printing Complements Injection Molding
Alpine Advanced Materials used a desktop 3D printer and the freeform injection molding process to reduce prototype tooling production time and cost for its customers.
Read MoreRead Next
MMT Chats: Pushing Further 3D Printing Development for Tooling
Partnership yields improvements to how tooling components are made with a new level of precision, accuracy and surface finish right out of the printer. Hillary Thomas, Westminster Tool and Paul DiLaura, Mantle tackle these topics with MMT Editorial Director Christina Fuges. This episode is brought to you by ISCAR with New Ideas for Machining Intelligently.
Read MoreWestminster Tool, Mantle Develop Case Study for Medical Devices
The joint project set out to create medical-grade forceps while testing the design, material, manufacturing and injection molding process with metal 3D-printed cavities.
Read MoreWestminster Tool Run Rigorous DOE on New 3D-Printed Tool Steels
Hybrid 3D printing platform offers mold builders high-tolerance metal parts faster, at lower cost and with less secondary finishing.
Read More