How to Make an Informed Hot Runner Decision
A proper hot runner assessment requires evaluating and calculating key runner system variables.
Evaluating the cost justification for a hot runner mold requires careful consideration of cycle time, material type, annual volume, available press size and power consumption, as well as the cost of utilities, resin pricing, allowable regrind percentage and labor rates. Here are three key areas to consider:
1. Cold Vs. Hot Process Considerations
Cycle time is the primary cost measure of the molding process, and cooling represents about 80% of the molding cycle (see Figure 1). The thicker the part, the longer the cycle time. However, the runner could determine the cooling time, and increase cycle time more than expected if the runner is thicker than the part.
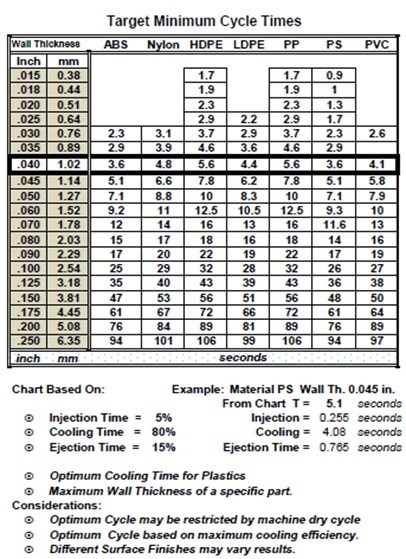
Figure 1
Images courtesy of Richard Hagfors.
The minute the resin leaves the machine barrel, the material starts to cool and solidify. This, in turn, causes injection pressures to climb and can yield unfilled parts, stress and warp. Limit the l/t ratio (length of flow versus part thickness) to avoid this outcome. Generally, a ratio under 100 is considered general-purpose molding and does not require increased injection pressures.
In a cold runner mold, the l/t ratio is measured from the start of the cold sprue, where the material leaves the heat source and begins to cool, which continues through the entire runner to the furthest point in the part (last point of fill). For example, 1 mm (0.039 inch) thick resin can flow easily 100 mm (3.94 inch). However, if a hot runner is used, the l/t ratio starts at the gate, reducing flow length and the injection pressure required to fill the part.
The higher the ratio, the more injection pressure is required to fill the part. A cold runner is included in the l/t calculation when the molder measures at the point of no added heat. This is one reason hot runners are appealing and can make the difference between molding a good or bad part.
Cold runners can also affect fill time, recovery, and residence time in the machine barrel and hot runner manifold. Every cycle involves the processing of the cold runner, as well as the parts.
Most molders adapt the mold and process to their current machines to optimize performance instead of using mold requirements to size the barrel. Injection molding machines equipped with reciprocating screws have a best-case range, so the process engineer must find the balance among residence time, temperature and pressure to deliver continuous melt to the mold.
Hot runner systems have some limitations. For example, manifold melt channels are typically manufactured in fixed melt channel diameters to limit pressure drop and maintain a consistent flow. The material in the manifold is considered part of the residence time, so always consult the material supplier on recommended temperatures and residence times. Also, melt channel size and complexity can impact color change.
Evaluating the cost justification for a hot runner mold requires careful consideration of cycle time, material type, annual volume, available press size and power consumption, as well as the cost of utilities, resin pricing, allowable regrind percentage and labor rates.
2. Material Considerations
Most polyolefin resins can be reused without issue. Engineered materials can be limited in regrind content because each time the resin is processed, it experiences another heat history that can degrade melt quality and impact performance, color, rigidity, tensile strength, etc.
Keep in mind, not every runner makes it to the granulator, and not every pellet makes it back to the hopper. While eliminating the cold runner can reduce scrap, a complete hot runner system might not be cost-justified based on low annual volume. The cost of an entire hot runner system may take longer than a year for payback. It might be wise to consider a hot/cold combination or at least a heated sprue bushing. The sprue is typically the thicker portion of the runner, and eliminating that and/or a portion of the runner could have an impact on the cycle time, resin consumption, scrap, etc.
In some applications, a hot runner system might eliminate scrap from unusable runners, but based on the required shot size volume (total volume of parts and runners) relative to the barrel volume, and it might reduce the consumption causing the barrel of the molding machine to be too large. Residence time on engineered materials would increase, which may cause other issues. For example, too small a shot can be challenging to process even with olefins.
3. Energy Considerations
Hot runner systems run on electricity like granulators. An injection molding machine takes roughly 1 kiloWatt (kW) to process 1 kg (454 lbs) of resin. Reducing the shot size to parts only can have a significant impact on power consumption. It stands to reason that only heating, melting and processing parts takes less energy than parts and runners.
When deciding between a cold or hot runner system, consider all of these variables, which combined can increase productivity and energy savings, improve material utilization and reduce floor space and noise requirements on the shop floor.
RHH Advisor and Consulting—Injection Molding
646-352-3021
rick.hagfors@gmail.com
Rick Hagfors is a consultant and advisor to the injection molding industry with over 40 years of experience in molding machines, injection molds, hot runner systems and process control.
Related Content
Machining Center Spindles: What You Need to Know
Why and how to research spindle technology before purchasing a machining center.
Read MoreIt Starts With the Part: A Plastic Part Checklist Ensures Good Mold Design
All successful mold build projects start with examining the part to be molded to ensure it is moldable and will meet the customers' production objectives.
Read MoreRevisiting Some Hot Runner Fundamentals
What exactly does a hot runner do? If you’ve been in the injection molding industry for any length of time, you might think the answer is obvious, but it is not.
Read MoreThe Benefits of Hand Scraping
Accuracy and flatness are two benefits of hand scraping that help improve machine loop stiffness, workpiece surface finish and component geometry.
Read MoreRead Next
Are You a Moldmaker Considering 3D Printing? Consider the 3D Printing Workshop at NPE2024
Presentations will cover 3D printing for mold tooling, material innovation, product development, bridge production and full-scale, high-volume additive manufacturing.
Read MoreHow to Use Strategic Planning Tools, Data to Manage the Human Side of Business
Q&A with Marion Wells, MMT EAB member and founder of Human Asset Management.
Read MoreHow to Use Continuing Education to Remain Competitive in Moldmaking
Continued training helps moldmakers make tooling decisions and properly use the latest cutting tool to efficiently machine high-quality molds.
Read More