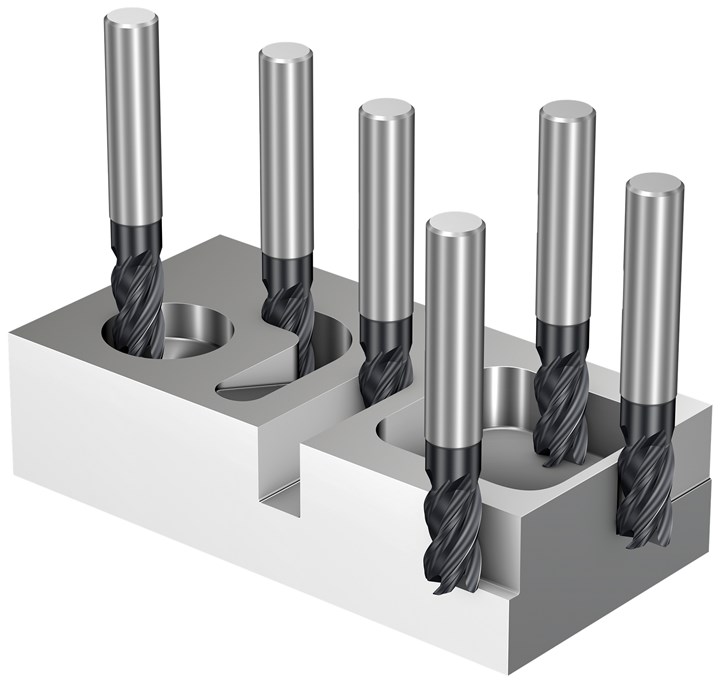
Solid end mills offer machining with different engagements and conditions for roughing with finishing capabilities, among other benefits. Photo Credit, all images: Sandvik Coromant
Aluminum has become an increasingly popular choice for moldmaking applications due to its lightweight, thermal conductivity and superior machinability. It possesses favorable properties and characteristics that make it easier to machine than other materials, such as being more readily cut, shaped and processed with minimal cutting tool wear and reduced machining time. However, to maximize the benefits of an aluminum mold, you must optimize the machining process.
Mold Characteristics
Aluminum molds often feature a variety of unique machining requirements depending on the specific needs of the intended application. For example, aluminum molds may require precision-machined grooves and slots to accommodate features like sealing mechanisms, slides or inserts. These features require careful machining to ensure proper fit, alignment and functionality. Molds may also require precise holes drilled at specific locations for injection points, cooling channels or venting. In other cases, aluminum molds have complex cavities and core inserts that require precise machining to achieve the desired part shape and dimensions. These features often demand multi-axis machining and intricate tool paths for the proper details and part accuracy.
Typically, aluminum molds also require smooth surfaces and high-quality finishes to ensure proper mold release and product parts with excellent surface quality. Ejector pin holes, runners and sprue channels are vital components of aluminum molds. These features must be accurately machined to ensure proper part ejection, efficient material flow and consistent mold filling during injection molding. Lastly, some applications may require specific textures or engraving on the mold surfaces to impart desired patterns or aesthetics onto the molded parts. Since each feature presents unique challenges in aluminum mold machining, machinists must employ appropriate cutting strategies, tooling selection and precision techniques to ensure dimensional accuracy, surface finish and overall mold functionality.
When it comes to challenges in machining aluminum, one significant challenge faced is the tendency of aluminum to generate chips that can be difficult to control due to its low shear strength. The built-up edge (BUE) formation is another common issue, leading to poor surface finish and dimensional inaccuracies. Additionally, the excellent thermal conductivity in aluminum can cause heat to accumulate rapidly during machining, affecting cutting tool life and potentially leading to thermal-induced distortion. To overcome these challenges and optimize the machining process, it is imperative to implement specific tips and techniques that address chip control, BUE prevention, effective heat management, etc.
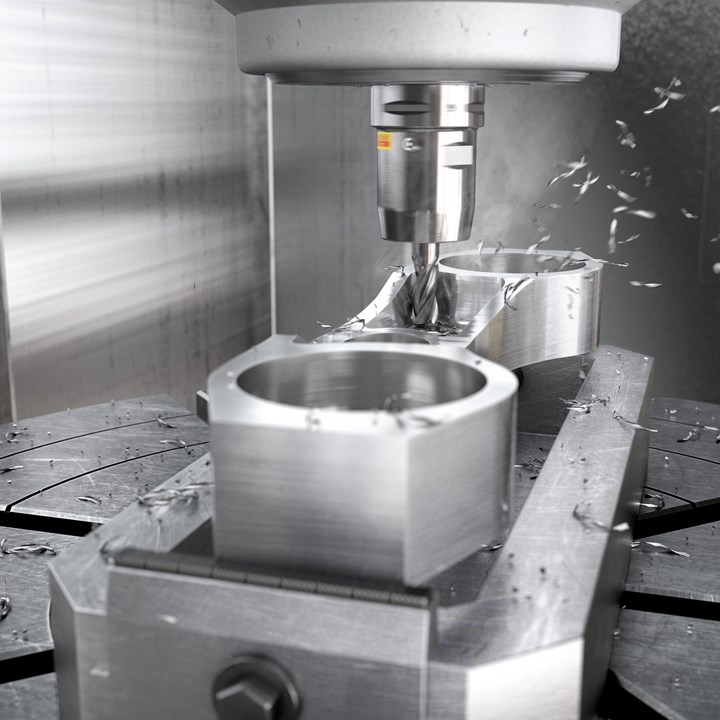
Dedicated solid end mills for aluminum are a stable and flexible concept designed to work in ISO N applications (non-ferrous metals, such as aluminum, copper and brass). They are specifically developed for roughing with finishing capabilities for different engagements in aluminum.
Tool Selection and Machine Setup
There are several factors to consider when it comes to machining aluminum. First, you want to choose the appropriate cutting tool by opting for high-performance tooling solutions specifically designed for aluminum. These tools offer superior tool life and performance, enabling efficient aluminum material removal while maintaining dimensional accuracy and surface finish. You also want to ensure the machining setup is rigid and stable to minimize vibrations. Since aluminum is prone to chatter, it can lead to poor surface finish and dimensional inaccuracies. Therefore, sturdy fixtures, clamps, workholding solutions and adequate machine rigidity can help to dampen vibrations and result in smoother machining operations.
Moldmakers should know two key cutting tool considerations: product durability and wear resistance.
Tool Geometry and Coatings
Using cutting tools with the appropriate geometry and coatings designed for aluminum machining is also important. Tools with sharp cutting edges and polished flute surfaces are ideal for reducing cutting forces and optimizing chip evacuation. Advanced coatings like TiAIN or TiCN can provide additional protection against BUE while improving tool life.
When it comes to coatings, a diamond-like coating (DLC) is a highly advantageous surface treatment for machining higher silicon content aluminum, and it can be applied using either physical vapor deposition or chemical vapor deposition processes. DLC coatings consist of a carbon-based structure with characteristics resembling that of natural diamond, offering exceptional hardness, low friction and exemplary wear resistance.
When applied to cutting tools, DLC coatings provide significant benefits for machining higher silicon content aluminum, which is notoriously abrasive and challenging to machine. The ultra-hard surface of DLC coatings acts as a protective barrier, thereby reducing tool wear and extending tool life. This is particularly advantageous when dealing with the abrasive tendencies of silicon particles within the aluminum matrix.
In addition to wear resistance, DLC coatings exhibit low friction properties, reducing the chances of BUE formation and material adhesion during machining. This results in improved chip flow and enhanced chip evacuation, leading to better surface finish and dimensional accuracy of the machined components. Using polycrystalline diamond (PCD) cutting tools with DLC coatings can yield remarkable results to further optimize the machining of higher silicon content aluminum.
PCD tools, which consist of a diamond layer bonded to a carbide substrate, possess optimized hardness and thermal conductivity. The combination of PCD tools and DLC coatings leads to wear resistance, reduced friction and enhanced thermal management, making them preferable in tackling the challenges of higher silicon content aluminum. By using DLC coatings and PCD tools in tandem, mold manufacturers can achieve longer tool life, improved surface finish and increased machining efficiency. These technologies offer a reliable and effective solution for optimizing the machining process and ensuring consistent quality in producing components from these challenging materials.
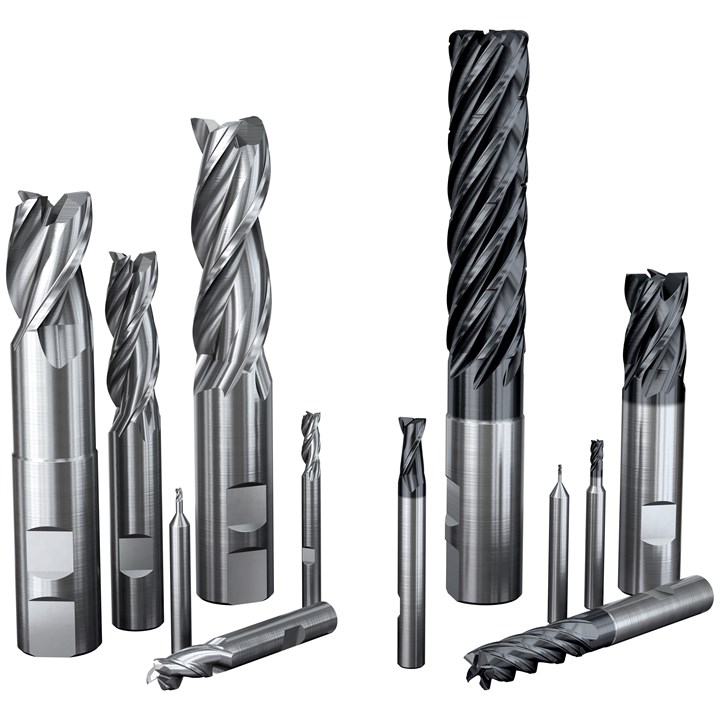
Each flute of these solid end mills is unequally spaced from the others on every level of the cutting edge, reducing the constant harmonics typically produced with conventional end mills.
Speed and Feed Cutting Parameters
Besides selecting the most optimized coatings, selecting the correct cutting parameters for achieving efficient aluminum machining is crucial. For instance, it is generally recommended to adopt higher values compared to other materials regarding feed rates and cutting speeds. High-speed machining techniques can boost productivity while maintaining tool life. However, balancing high cutting speeds with the appropriate feed rates is essential to prevent excessive heat generation.
Coolant also plays a vital role in aluminum machining. Coolant helps dissipate heat, lubricate the cutting zone and flush away chips. When it comes to aluminum machining, flood coolant or high-pressure coolant systems are commonly employed to ensure effective cooling and chip evacuation. Making use of minimum quantity lubrication techniques or soluble oils for better lubrication and cooling is critical in reducing the risk of built-up edge formation. Likewise, regular tool inspection and maintenance are essential to ensure optimal performance. Users should inspect tools for signs of wear, such as edge chipping or excessive flank wear, and promptly replace worn or damaged tools to avoid compromised machining quality and potential tool breakage.
Implementing suitable machining strategies can also significantly improve aluminum machining efficiency. Users should consider employing high-efficiency milling techniques, such as trochoidal or adaptive milling, which can reduce cutting forces, improve chip evacuation and increase metal removal rates. Also, proper workpiece fixturing ensures consistent part accuracy and repeatability during aluminum machining. Precision locating and positioning of the workpiece within the fixture improves machining accuracy.
Last to be considered are post-machining finishing operations such as deburring, polishing or surface treatments. The appropriate techniques can help achieve the desired surface finish and dimensional accuracy. During this process, it’s important to consider using nonabrasive methods like chemical polishing or vibratory finishing to avoid damaging delicate features or compromising tolerances.
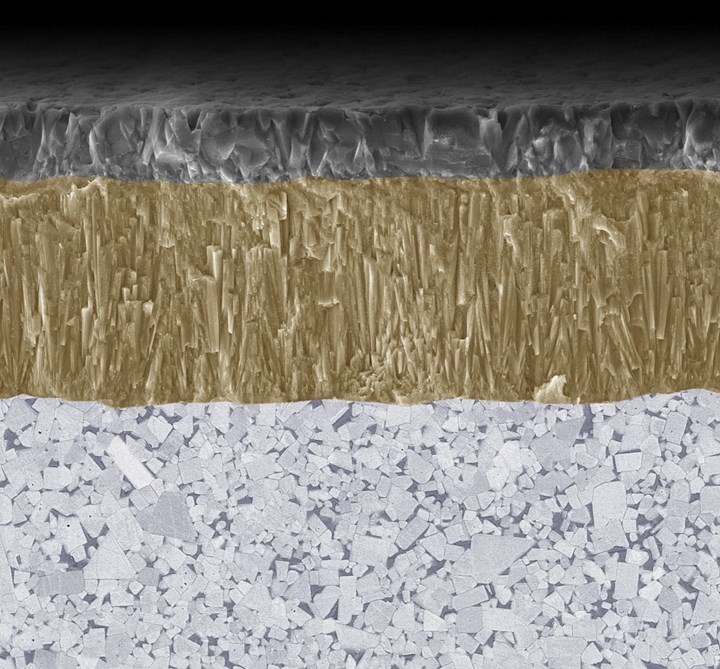
Cutting tool coating as seen under a microscope.
Innovative Solutions for the Future of Aluminum Machining
When choosing products and solutions already on the market, using a high-performance cutting tool designed to optimize the aluminum machining process is important. Machinists should seek out an innovative tool that offers a range of features and benefits that enhance productivity, tool life and surface finish.
Moldmakers should know two key considerations: product durability and wear resistance. A product engineered with a specialized substrate and advanced coating technology, ensuring long-lasting performance even in demanding aluminum machining applications, is preferred. This level of durability translates to extending tool life, reducing the frequency of tool changes and increasing machining uptime.
Regarding aluminum machining, using high-performance cutting tools specifically designed for the process can optimize efficiency and results. These tools offer exceptional durability and wear resistance, ensuring extended tool life in demanding aluminum machining applications. Optimized geometry and advanced coatings facilitate efficient material removal, minimize cutting forces and prevent built-up edge formation. Their versatility enables various machining operations, reducing the complexity and cost of tool management. By leveraging these tools, moldmakers can achieve higher productivity, faster metal removal rates and reduced cycle times, enhancing their market competitiveness. Implementing such advanced techniques and tools has been proven to improve efficiency, quality and productivity in aluminum tooling and mold manufacturing.
Related Content
The Ins and Outs of Hot Runner Temperature Control
A training checklist that explains the why and how of proper hot runner temperature control and system management.
Read MoreSolving Mold Alignment Problems with the Right Alignment Lock
Correct alignment lock selection can reduce maintenance costs and molding downtime, as well as increase part quality over the mold’s entire life.
Read MoreMoldmakers Deserve a Total Production Solution
Stability, spindle speed and software are essential consideration for your moldmaking machine tool.
Read More6 Ways to Optimize High-Feed Milling
High-feed milling can significantly outweigh potential reliability challenges. Consider these six strategies in order to make high-feed milling successful for your business.
Read MoreRead Next
How to Overcome Cutting Tool Vibration
Advanced indexable milling cutting tool design provides secure, predictable machining, increased metal removal rates, reduced cycle times and fast changeovers.
Read MoreIncrease Process Security and Minimize Risk
Staying competitive in the growing automotive market comes down to quality, productivity and cost per component, and all three can be accomplished with the right set of tooling solutions.
Read MoreHow to Use Continuing Education to Remain Competitive in Moldmaking
Continued training helps moldmakers make tooling decisions and properly use the latest cutting tool to efficiently machine high-quality molds.
Read More