How to Address the Mold Engineering Skills Gap
Four ways to equip mold engineers with the necessary knowledge to tackle the skilled workforce crisis.
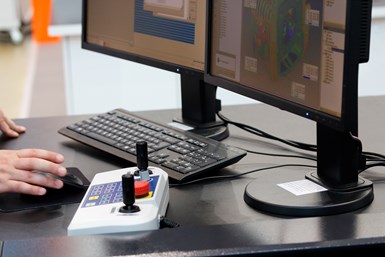
The best way to approach the mold engineering skills gap is to create powerhouses of knowledge and innovation within your company. Photo Credit: Getty Images
One way the engineering skills gap has played out across the industry is the lack of formal training and education in this specialized field. However, some companies have solved this challenge by quickly learning ways to train employees internally. This gives them competitive advantages over other manufacturing companies that don’t think about training their teams in-house.
Another way to address the engineer shortage is to have a strong leadership team in facilities backed up by experienced engineers. These seasoned professionals can quickly pass on their knowledge to new hires and help bridge the gap in competencies. Also, cross-training between different facilities worldwide — for companies with facilities in different countries — can provide a wealth of expertise and insights you can’t get anywhere else.
Lastly, fostering employee communication and collaboration can help mitigate the skills gap. By encouraging them to work together, learn from each other and share their ideas and experiences, you’ll give employees the tools they need to perform at their best. And with everyone working together, you’ll be able to better bridge the growing employee skills gap and take your company to the next level of success.
Here are four other ways to help close the skills gap in moldmaking:
1. Make closing business knowledge gaps a priority.
Stay ahead of the game by continuously filling knowledge gaps as your business grows. Regular employee training, product updates and policy changes are all crucial factors in maintaining the shape of your expanding enterprise. Invest in relevant training to avoid tension and stress caused by an untrained — or improperly trained — workforce.
2. Maximize your team’s skills inventory.
Just as you budget for investments and expenses, you must empower employees to take control of their careers with skill budgeting. Inspire your staff to conduct yearly skills inventories to identify their strengths and weaknesses. Then, track their progress throughout the year and watch as they soar to new heights.
3. Accelerate and streamline employee training.
Do you yearn for a more efficient and effective way to educate employees? If so, consider microlearning, a method for delivering knowledge that’s simple to create and easy to update and share in real time. With microlearning, you can drastically reduce the time and effort required to create training materials by encouraging your team to focus on small learning objectives at a time.
4. Keep pace with the ever-evolving world of training.
The future is now, and the need for reskilling has become a reality. With AI, robotics and other innovative advancements continuing to shape the business world, staying ahead of the curve is more crucial than ever. Don’t fall behind; stay current with the latest training technologies and techniques.
Leaders within the industry have the power to turn this crisis into a catalyst for change. By providing engineers with the right tools, resources and support, leaders can equip them with the skills and knowledge necessary to tackle the obstacles of today and tomorrow. In doing so, leaders can ensure that the moldmaking industry remains at the forefront of technological advancement and continues to thrive for generations.
Related Content
Confronting the Mold Design Talent Drought
Recently, I reposted on LinkedIn the results of an informal survey we conducted, which revealed a shortage of skilled mold designers. It quickly gained a lot of traction. Given the response, I thought I'd summarize the feedback and keep the conversation going.
Read MoreCross Training, In-House Capabilities and Collaborative Design Move Helm Tool Forward
Cross-training, bringing it all in-house, molding and collaborative design are essential to Helm Tool's success.
Read MoreMold Maintenance Continues to Matter: Enhanced Training Program in a New Facility
I attended a MoldTrax mold maintenance workshop in 2019 and shared my experiences, and despite changes in ownership, the workshop's remarkable value endures, as discussed in a recent Q&A with the current leadership.
Read MoreMaking Mentoring Work | MMT Chat Part 2
Three of the TK Mold and Engineering team in Romeo, Michigan join me for Part 2 of this MMT Chat on mentorship by sharing how the AMBA’s Meet a Mentor Program works, lessons learned (and applied) and the way your shop can join this effort.
Read MoreRead Next
How to Foster Innovation Through a Culture of Education, Mentoring
Dynamic Tool Corp. shares its strategy for building a team with the right attitude and aptitude to deliver innovation that meets customer expectations.
Read MoreUnique Mold Design Apprenticeship Using Untapped Resources
To help fill his mold design skills gap, Jeff Mertz of Anova Innovations, is focused on high schools and underprivileged school districts, a school that has lower graduation and college entrance rates. The goal is a student-run enterprise.
Read MoreMMT Chats: How Onboarding and Acquiring Lead to Growth
MMT Editorial Director, Christina Fuges sits down with Cavalier Tool & Manufacturing President Brian Bendig to discuss how he has grown the business with a three-step onboarding process and successful acquisitions. This episode is brought to you by ISCAR with New Ideas for Machining Intelligently.
Read More