Cost Segregation Study: A Lucrative Tax Strategy
A cost segregation study will maximize a mold shop’s depreciation benefits, decreasing current tax liability, improving cash flow and increasing after-tax profits.
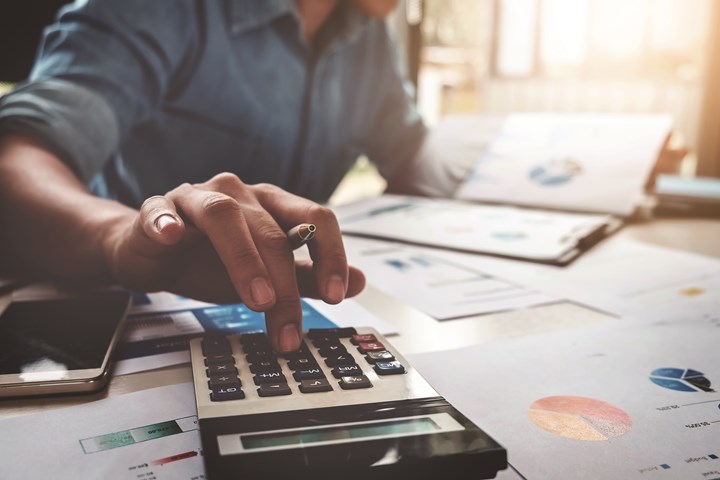
If your shop hasn’t done a cost segregation study, there is a good probability that you haven’t claimed the appropriate amount of depreciation. This means that your business could be missing out on greater depreciation deductions earlier on in the life of the shop.
A cost segregation study is the process of identifying and separating out personal property (IRC §1245 property) that is or has been grouped with real property (IRC §1250 property). A cost segregation study breaks down the components of a building and allocates the tax basis between these two types of property that make up the entire building.
This is important because without the study, the asset class-life for a commercial building is 39 years. Certain components of the building and the building systems qualify for shorter class lives. The assets identified to be shorter class lives for mold shops will be depreciated over five, seven, 10 or 15 years. For most mold shops, these assets might be special electrical, air, water, plumbing, mechanical and finish components. It is not uncommon for 25 to 50% of a shop’s total costs to be eligible for reclassification into shorter life assets.
According to the U.S. Treasury department, “Cost segregation studies are a lucrative tax strategy that should be considered in almost every real estate purchase.” An average study for a $1 million purchase or new construction could generate over $250,000 of accelerated depreciation over the normal 39 years.
Generally, a detailed, engineering-focused cost segregation study will maximize a mold shop’s depreciation benefits. As the depreciation deductions increase, current tax liability decreases, improving cash flow and increasing after-tax profits.
Mold shops may offset current ordinary income with depreciation, at ordinary income tax rates. However, if a shop sells the underlying asset, it will generate a capital gain or depreciation recapture at the 25% rate. Both the capital gains tax rate and the 25% depreciation recapture rate are likely lower than the ordinary rate for which the shop received the depreciation deduction. Mold shops also benefit from the time-value of money, getting a tax deduction now as opposed to future tax years.
An average study for a $1 million purchase or new construction could generate over $250,000 of accelerated depreciation over the normal 39 years.
Defining Property
The use of cost segregation studies began increasing in the late 1990s following several prominent tax court cases and related IRS rulings. Interest intensified further in 2013 and 2014 when the IRS issued new tangible property regulations governing the capitalization and depreciation of certain capital expenditures. These regulations also introduced the definition of a unit of property. A building structure consists of the building and its structural components, other than the structural components designated as building systems.
Building systems include HVAC systems, plumbing systems, electrical systems, escalators, elevators, fire protection, alarm and security systems, gas distribution systems, etc. It is important to understand the unit of property in order to determine whether an expenditure is required to be capitalized or if it may be deducted currently.
To determine if an expenditure is to be capitalized, mold shops must first understand the unit of property and the building systems. The expenditure is evaluated to determine if it meets the definition of a restoration, adaptation to new or different use, betterment or improvement of the building system and unit of property. A cost segregation will help to identify the specific costs related to these various building components so that building owners can apply the proper tax treatment.
Cost segregation studies became even more valuable with the recent Tax Cuts and Jobs Act (TCJA) changes to the depreciation rules. The TCJA increased bonus depreciation for qualifying assets to 100%. This means a shop can automatically expense all assets properly classified as an asset class of 20 years or less as bonus depreciation under the MACRS (Modified Accelerated Cost Recovery System) depreciation.
In addition, the IRS expanded Section 179 to include certain components of the building. Improvements to a mold shop, such as new roofs, HVAC, fire protection, alarm systems and security systems will qualify for Section 179. A cost segregation study identifies all of the components of the building to ensure the tangible property regulations were properly implemented, as well.
Mold shops also benefit from the time-value of money, getting a tax deduction now as opposed to future tax years.
Study Benefits
While cost segregation studies can be particularly beneficial in improving the cash flow on new construction, they can also provide tax and cash flow benefits for improvements to existing structures. It is worth evaluating a cost segregation study on any size property. Mold shops may even consider the benefits of a study on a building improvement or addition with a cost basis as low as $250,000.
It is never too late to perform a cost segregation study. If your shop missed taking advantage of these benefits in the year the property was initially purchased or constructed, and placed in service, you can still do a look-back study as long as the building was acquired or renovated after December 31, 1986.
A look-back study claims all of the prior years’ missed depreciation deduction in one year. Amending your tax returns is unnecessary. Mold shops can claim these benefits on a Form 3115: Change in Accounting Method through an IRC §481(a) adjustment (the difference between the depreciation expense claimed and the depreciation expense a shop should have claimed). Engineering-based cost segregation studies have been upheld and appropriate since 1997, and the change in accounting method is automatically approved.
Cost segregation studies provide fantastic tax benefit to those mold shops owning their own plants. It’s typically best to perform a cost segregation study in conjunction with the tangible property rules.
For More Information
Related Content
Making Mentoring Work | MMT Chat Part 2
Three of the TK Mold and Engineering team in Romeo, Michigan join me for Part 2 of this MMT Chat on mentorship by sharing how the AMBA’s Meet a Mentor Program works, lessons learned (and applied) and the way your shop can join this effort.
Read MoreEditorial Guidelines: Editorial Advisory Board
The Editorial Advisory Board of MoldMaking Technology is made up of authorities with expertise within their respective business, industry, technology and profession. Their role is to advise on timely issues, trends, advances in the field, offer editorial thought and direction, review and comment on specific articles and generally act as a sounding board and a conscience for the publication.
Read MoreTackling a Mold Designer Shortage
Survey findings reveal a shortage of skilled mold designers and engineers in the moldmaking community, calling for intervention through educational programs and exploration of training alternatives while seeking input from those who have addressed the issue successfully.
Read MoreThe Role of Social Media in Manufacturing
Charles Daniels CFO of Wepco Plastics shares insights on the role of social media in manufacturing, how to improve the “business” side of a small mold shop and continually developing culture.
Read MoreRead Next
Do a Technology Risk Assessment to Protect Your Shop
The road to protecting your shop’s information starts with a technology risk assessment that identifies areas to protect and areas to consider public knowledge.
Read MoreUnderstanding the New Flow Through Deduction
The qualified business income deduction of the Tax Cuts and Jobs Act gives mold shops a 20-percent deduction of qualified business income to all non-corporate taxpayers, but it comes with some qualifications, restrictions, and limitations.
Read MoreTax Reform Impact on Inventory Deductions
The changes made to Internal Revenue Code (IRC) §471 Rules for Inventory of the Tax Cuts and Jobs Act (“Act”) present some tax-savings opportunities for “small” mold shops with regards to work in process (WIP) and finished goods.
Read More