A Supporting Role
This shop solved a critical application problem with help from a distributor in the know about potential solutions and a responsive supplier to help implement them.
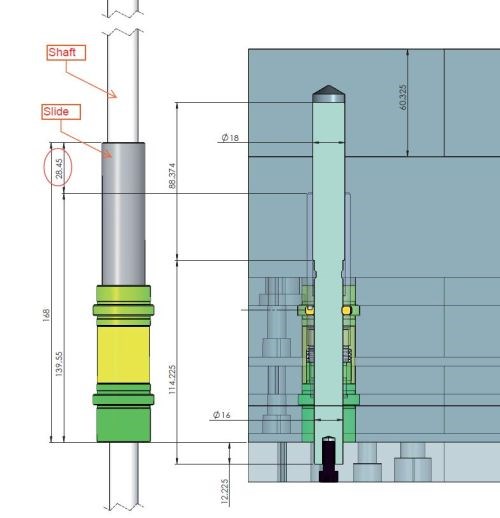
Fitting the double ejector rod within the tool required cutting both the shaft and the sleeve to size.
Even the most ideal equipment for an application isn't worth much if a shop doesn't know it exists or can't get the support needed to implement it properly. One recent example is an application at Mid Missouri Tool and Die, a toolmaking and molding operation in Carrollton, Mo. As detailed in this article, vertical lifters from Cumsa enabled the shop to design a mold that releases a series of undercuts without requiring angled machining operations. The tool also incorporates double ejector rods from the same supplier to provide the two-stage action needed to release the rest of the part from the mold.
Implementing both components required more than simply selecting and ordering them from a catalog, although that's how shop co-owner Tony Machado says he got wind of Cumsa in the first place. The catalog in question was left to him by Lee Horneyer, president of St. Louis-based distributor Lee Horneyer Company, who'd told him about the supplier's offerings during an unrelated visit to the shop about 6 months prior. Little did Machado know at the time that Horneyer had just introduced him to the ideal solution to a problem that otherwise might have prevented the shop from taking advantage of a big opportunity from an important customer.
Upon revisiting the catalog, Machado knew the essential design of the vertical lifters would work well for his application. However, he says he needed input from the Spanish supplier's U.S. arm in Troy, Mich., to determine the exact model he'd need. Even more important was support from Cumsa USA engineer Jorge de Fortuny, who helped him through the modifications needed to properly incorporate the double-ejector rods.
When he received the components, Machado wasn’t quite sure how to proceed. He knew he'd need to cut the double-ejector rod’s inner shaft to arrive at the proper length at both the larger diameter at the top and the smaller diameter at the bottom. However, he didn’t expect to find that the slide that moves along the shaft was also too long. It turned out that he'd also have to disassemble the component and cut that slide at 28.45 mm, as detailed in the diagram above. This was only a minor point of confusion that was easy to clear up, but the job very well could have been delayed if Fortuny weren't available to answer questions in a timely manner.
Of course, making the mold work properly also required Machado's own ingenuity and that of his team (read the article for more about that). Moreover, were it not for their knack for taking on tough challenges, the customer likely never would have approached them with the job in the first place. Still, it's worth keeping in mind that suppliers and distributors can—and should—play a critical supporting role in ensuring things get done right.
Related Content
-
The Secrets to Hard Milling Success
The Secrets to Hard Milling Success
-
Fundamentals of Designing the Optimal Cooling System
The right mold components can help improve mold cooling and thereby produce higher-quality parts.
-
Solving Mold Alignment Problems with the Right Alignment Lock
Correct alignment lock selection can reduce maintenance costs and molding downtime, as well as increase part quality over the mold’s entire life.