Cooled Ante-Chamber Bush Gate Regulates Gate Point Temperature Control
Meusburger’s cooled ante-chamber bush EC with customizable gate diameters features cooling close to the gate point along the entire circumference of the hot runner nozzle.
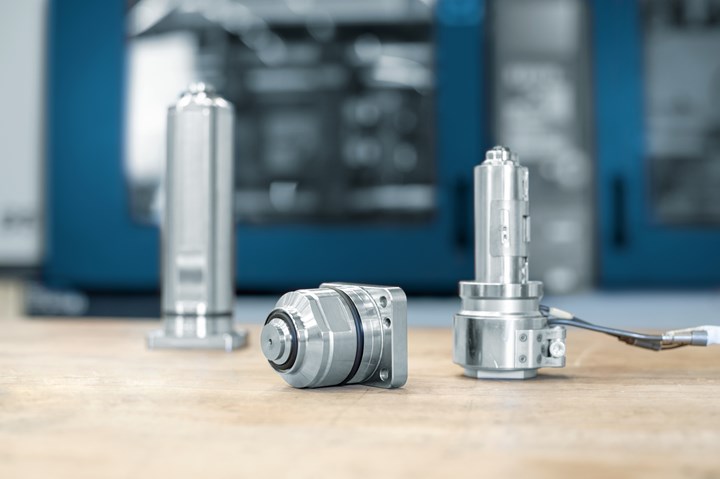
Photo Credit: Meusburger US
Meusburger US presents its cooled ante-chamber bush, which ensures optimal cooling in the gate point. Ante-chamber bushes are used in hot runner nozzles for providing the required nozzle shape in the cavity plate. They help to quickly restore the gate point quality in applications with abrasive plastics.
Meusburger customers are able to customize the cooled ante-chamber bush EC according to their requirements with quick delivery time. If the appropriate installation space is available in the mold, Meusburger says the ante-chamber bush can provide both temperature regulation close to the gate point and along the entire circumference, as well as exact installation dimensions for the company’s smartFILL hot runner nozzle series. This is said to enable maximum flexibility regarding the gate diameter, the length of the ante-chamber bushes and the connection to the mold’s temperature control channels. Ultimately, uniform gate temperatures and easy cleaning ensure lasting quality for both the gate and the component for the injection-molded part.
The cooled ante-chamber bush features cooling close to the gate point along the entire circumference and optimal control of the gate temperature. Further advantages are the wear-protected and corrosion-resistant design and fast integration into the mold concept, along with the customizable gate diameters. In addition, the lengths can be matched exactly to the mold design.
Related Content
-
Technology Roundup: New/Improved Technologies You Don't Want to Miss
With all the technology joining the market, moldmaking is a versatile, ever-evolving industry. As such, this technology roundup has no specific theme — it features a variety of products for applications and solutions across the industry.
-
Products and Services for Multiple Moldmaking Needs
New year, new technology roundup! Featured here is a collection of product offerings, from profile milling cutters to industry-specific CAD/CAM software to innovative hot work tool steels.
-
To the Next Level: Hot Runners, Mold Components Solutions and Services
Moldmaking can be a complex business, but things can be simplified with the right hot runner and mold component technologies and services.