The Designer's Edge: Cleaning and Maintaining the Mold in the Press
Randy discusses cleaning and maintaining the mold in the press to reduce downtime.
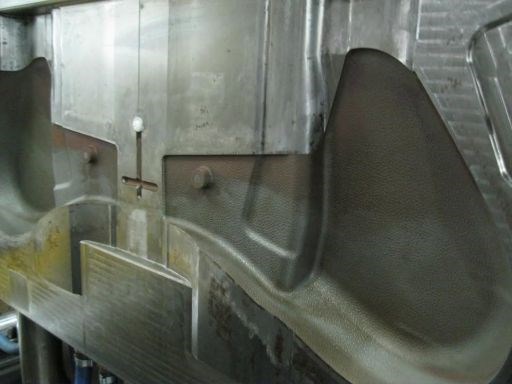
Rust in the cavity.
In the last series I discussed water and design considerations to reduce mold issues. Water via leaks or condensation can cause a lot of damage to a mold and its cavities. However, if the issue is caught soon enough a light surface rust will not be a major issue, but if the water or condensation is allowed to sit it can cause major damage.
For one project the tool was properly cleaned, sprayed with rust preventative and pulled from the press, but the water leak was not noticed and water accumulated inside the clearance holes. As the tool sat the water leaked into the diamond-polished cavity and caused major damage. Some may ask, "How could this occur with the tool properly pulled, cleaned and sprayed with a rust preventative?" Well, not all rust preventatives are the same. I have used numerous brands over the years. Cavities can also have coatings applied to protect against rust, if the issue is chronic.
Welcome! You’ve unlocked premium content.
Considerations for the specific brand or formula of a rust preventative include cost, old habit, a lack of understanding the pros and cons or just pure opinion. I bring this up so you might consider if the rust preventative you are using may be contributing to any of your issues.
Viscosity varies with each rust preventive. Some prefer to use a liquid version that is more visible. I have found that these types can cause start-up issues with scrap, as well as extra labor to clean the cavities before starting the mold for production. They also can break down the greases used on the tool and contribute to bleeding, scrap and downtime for cleaning.
For years I have used the dryer version, which does not break down grease and provides a more protective barrier against rust. It also does not require cleaning the cavities at startup and reduces start- up scrap with the barrier being removed after a couple shots. When it comes to transporting molds through different climates use a more robust protectant.
Related Content
-
How to Achieve the Best Mold Finish
A look at factors that impact the polishability of tool steels and recommendations for obtaining a high-gloss finish.
-
What Is Scientific Maintenance? Part 1
Part one of this three-part series explains how to create a scientific maintenance plan based on a toolroom’s current data collection and usage.
-
Laser Welding Versus Micro Welding
The latest battle in finely detailed restoration/repair of mold materials.