Making the Rounds and Making a Difference
Robert (Bob) Novak, Associate Dean for the School of Applied Technologies of Waukesha County Technical College has been keeping MMT informed on his moldmaking program for years. Despite it continuing to grow each year, he never stops promoting.
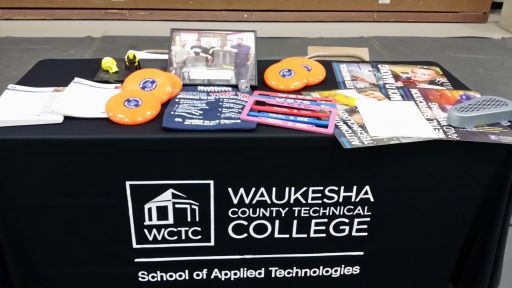
Robert (Bob) Novak, Associate Dean for the School of Applied Technologies of Waukesha County Technical College (WCTC) has been keeping me informed on his moldmaking program for years. Despite the program growing each year, he never stops promoting. He's been making the rounds to different high school job fairs with some pretty awesome moldmaking-specific posters/brochures (see below), and it's been paying off.
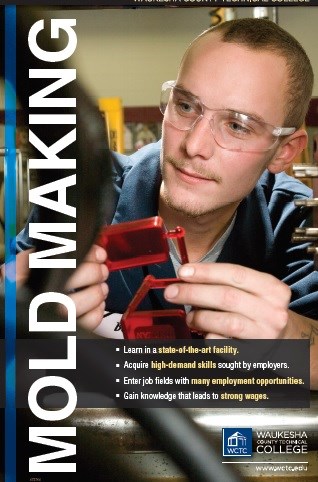
WCTC's Dual Enrollment Academy, which involves local companies and high schools, offers high school seniors the opportunity to earn technical college credits while they develop skills necessary in the real-world workforce. "Most students are employed before they graduate high school and most continue to take classes at WCTC," says Bob, "We fondly refer to our students as 'Duallys'.”
There was a definity learning curve on WCTC's part during its first year of working with high school students, but with a few adjustments to the orientation this past year went a lot smoother. The Tool & Die and Metal Fabrication/Welding courses are full and they continue to look for ways to expand the program in the future.
Bob says that one student he had in a CNC programming class when he was a high school student under WCTC's Youth Options program, went onto the Milwaukee School of Engineering (MSOE) and earned a degree. He returned to WCTC's tool and die program because he wanted to add that to his knowledge base. That student is Patrick Anderson, "I chose to attend WCTC's Tool & Die program in an attempt to bridge the gap between designers and manufacturers. Having graduated from mechanical engineering, the theory of thermodynamics, mold flow, and part design are subjects I have studied at great length. However, all those subjects are useless without being able to turn concepts into a physical product. The state of the art equipment and brilliant instructors at WCTC will enable me to take my part designs to the next level."
Here are some quotes from other students. Who knows, maybe one of these will be a future employee of your shop!
“I got into the tool and die field because I've always liked working on something where I can see the end result, and the challenges that it presents to me. It is an industry that requires both patience and boldness, with a measure twice, cut once mentality and get the need to job done on time sometimes competing with each other.” Kelly Marx
“After a long time spent looking for the right career, I came to WCTC because I wanted to move in a direction that required concrete skills in machine tool operation. I found the initial certificate classwork suited me so well that I decided to continue with the rest of the tool and die program so that I could get the highest level of training available. At the end of the first year I was referred to a mold shop that has proven to be a great fit for me and I am looking forward to beginning my apprenticeship when I graduate at the end of this semester. Now I have finally gotten into a solid career with a future because of tech school and apprenticeship.” Jason Chandler
“It’s a real privilege to be here at WCTC in the Tool & Die/Moldmaking program. Every day I drive 45 minutes from my home in Watertown, Wisconsin, to get to class and get my hands dirty in the shop. Ever since I was in high school I favored machining things over other practices like welding and fabrication. There is something different about it. It’s not beating things with a hammer until they fit, its precision machining things until they fit perfectly down to thousands of an inch. The feeling of success in this trade is just outstanding and the fact that you can see your product that you made is nothing shy of perfection.” Hunter Minning
“I chose the tool and die program because it’s a career field with a promising future. Many of our tool makers are retiring and they need young people to fill their positions. I want to make a better life for myself and my daughter in a field where the skies the limit.” Ben Melcher
“I decided to go into the Tool and Die trade as a result of my early education in engineering. I had a desire to not only design something but to be able to construct those items I designed from start to finish. After watching videos, talking with others in the trade, and viewing shops I believe this trade is a good fit for me.” Aaron Mueller
“I chose the Tool and Die program because I love to work with my hands and for the first time in my life I am actually using my head at my job, I have had jobs that require thinking in the past but nothing as stimulating and rewarding as the manufacturing industry. It is visually rewarding and makes me feel accomplished at the end of the day. I could not imagine going into another field. I love what I do.” Ivan Imes
“Moldmaking requires a lot of details, and I love working with details, so it's perfect for me.” ~Ben Pipkorn
“I chose to get in to this trade because I like to make things, especially out of metal. Being able to machine metal into different shapes, forms, almost anything really interests me and I think I've finally found my passion. Looking forward to going to work is also a plus.” Evan Hels
“I decided to get into this trade because I wanted to learn how things are made and I enjoy working with my hands. This career choice provides the knowledge and skills you can obtain to produce something you can be proud of. It also gives you challenges which I like because it helps build problem solving skills. I'm looking forward to learning more about this field in the future.” Kong Vang
“I decided to enroll in the Tool and Die Program because I like making things and being creative. I enjoy working with my hands and have always been mechanically inclined. Ever since I started this program, I feel like I am in the right career path and have a true passion for Tool and Die. I like that you're constantly learning and I enjoy the challenging aspects of this trade. In my opinion, Tool and Die is such an awesome career choice because anything you dream of, you can make. When you've worked so hard on a project and finally see the final product, it's an amazing feeling knowing that you did that. The possibilities and growth in this trade are endless and I'm excited for the road ahead of me.” Kelli McCullough
“In 1966 my grandfather, Robert Zeman, founded Zeman Tool and Manufacturing. When he passed away in April of 2012, I came to the realization that outside of my mother and two aunts (owners/office), there was no blood left on the shop floor in the company. I couldn't let the company, for lack of a better term, die with him. I was at a bit of a crossroads in my life, and figured I could be the one to allow my grandfather’s hard work live on. This "epiphany" of sorts led me to enroll in the program in the spring of 2014 and I have been enjoying it ever since.” Justin Grosskreutz
“I chose to be in this program because I like to see the final product I'm making and the step by step processes that come with it. Doing an operation on the machine that takes a lot of time to set up and prove out is what I prefer on a daily basis.” Andrew Makovec
“It's great to be behind the scenes in this world of thousands of products. Being a mold maker certainly makes you look twice at all of the plastic parts found in things we use every day. From cars and computers to toys and plastic forks, even the safety glasses I wear every day are made by molding plastic.” Evan Yoakum
“The reason I got into moldmaking is because it was a trade that I knew I could enjoy and continue to learn for the rest of my career.” Joshua Stoecker
“As a 16 year old I was hired as a plastic injection molding press operator. I became interested in what the tool room at my company was doing, and I knew tool making was a good trade to get into. I went and talked to the boss of the mold building department and he actually ended up hiring me in the tool room. I struggled at first but after my first year here at WCTC everything I learned at school and work started coming together.” Thomas Lang
"Machining runs in the family, I have 2 uncles who use to be machinists. Now one is a supervisor and the other is an engineer. My grandpa use to be a machinist, he use to work at a shop that made airplane parts. For his retirement gift they made him a lamp out of the parts he made and gave it to him.” Jacob Rosenthal
“I started to get into mechanical engineering but I didn't feel like sitting behind a desk my whole life. Then I heard about tool & die through my cousin because he just finish his apprenticeship. I toured his shop and it looked like a career I could be in. I've always liked making stuff and this is the ultimate trade for that.” Cody Rehm
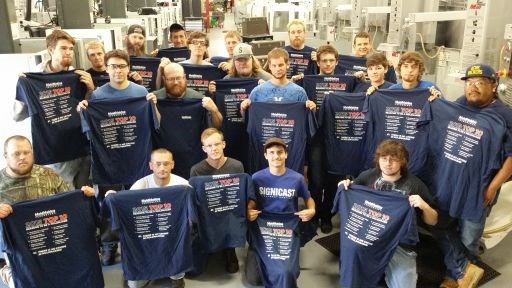
Read Next
Reasons to Use Fiber Lasers for Mold Cleaning
Fiber lasers offer a simplicity, speed, control and portability, minimizing mold cleaning risks.
Read MoreHow to Use Strategic Planning Tools, Data to Manage the Human Side of Business
Q&A with Marion Wells, MMT EAB member and founder of Human Asset Management.
Read MoreAre You a Moldmaker Considering 3D Printing? Consider the 3D Printing Workshop at NPE2024
Presentations will cover 3D printing for mold tooling, material innovation, product development, bridge production and full-scale, high-volume additive manufacturing.
Read More